Mold makers are skilled professionals responsible for designing, creating, and repairing molds and models used in industrial manufacturing processes. These molds are essential for mass-producing plastic or metal components and products with precision and consistency. Mold makers utilize a combination of traditional craftsmanship and modern technologies, such as computer-aided design (CAD) and industrial machinery, to ensure the molds meet exact specifications. Their work is critical in industries like automotive, aerospace, consumer goods, and electronics, where high-quality, identical parts are required. Mold makers also troubleshoot and repair molds to maintain production efficiency and product quality.
Key Points Explained:
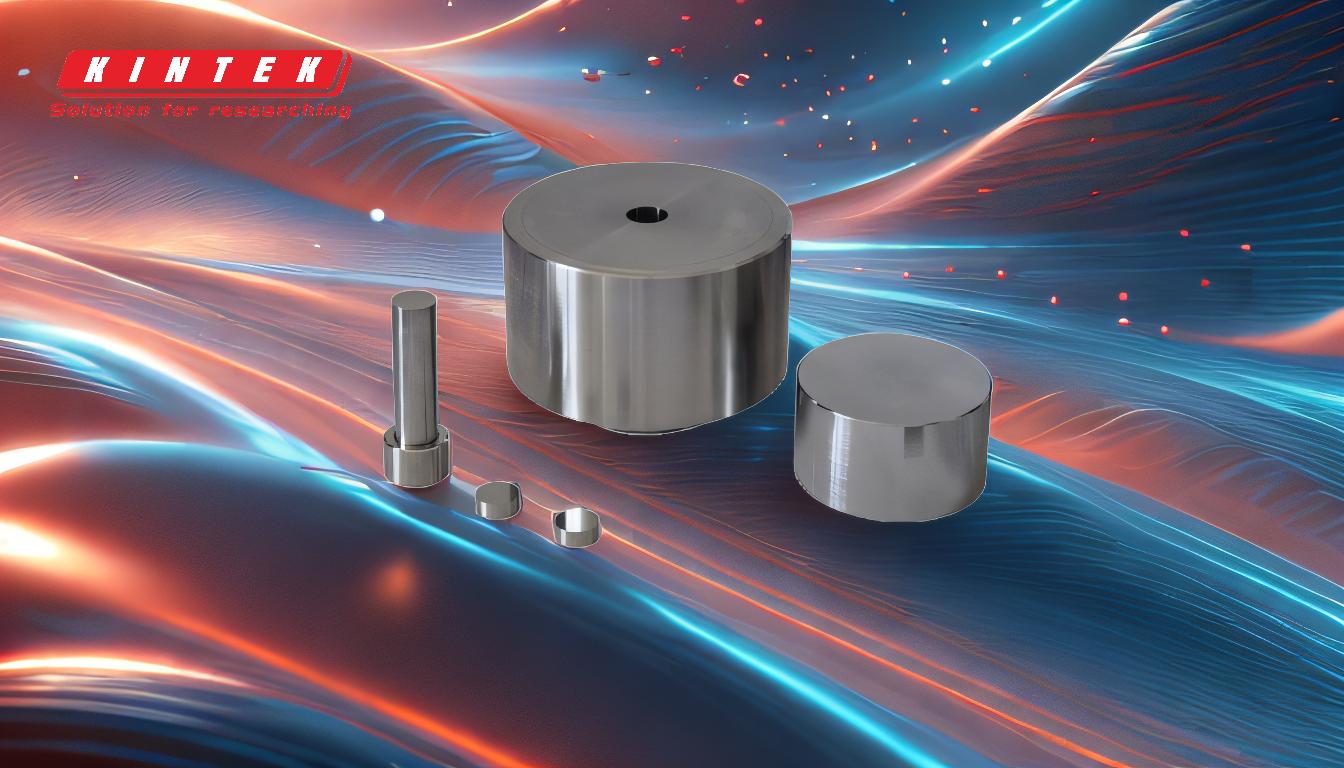
-
Designing Molds
- Mold makers begin by designing molds based on the specifications provided by engineers or clients.
- They use computer-aided design (CAD) software to create detailed blueprints, ensuring the mold will produce the desired shape and dimensions of the final product.
- The design process includes considerations for material flow, cooling systems, and ejection mechanisms to optimize the mold's performance.
-
Creating Molds
- Once the design is finalized, mold makers use advanced machinery, such as CNC (Computer Numerical Control) machines, to fabricate the mold.
- They work with materials like steel, aluminum, or composite alloys, selecting the appropriate material based on the production requirements and durability needs.
- Precision is critical during this stage to ensure the mold can produce identical parts consistently.
-
Repairing and Maintaining Molds
- Over time, molds can wear out or become damaged due to repeated use. Mold makers inspect, repair, and maintain molds to extend their lifespan and ensure consistent product quality.
- This involves troubleshooting issues like cracks, warping, or misalignment and using tools like welding, grinding, or polishing to restore the mold's functionality.
-
Utilizing Technology
- Modern mold makers rely heavily on technology, including CAD software, CNC machines, and 3D printing, to enhance precision and efficiency.
- They may also use simulation software to test the mold's performance before production, reducing the risk of errors and costly revisions.
-
Collaborating with Other Professionals
- Mold makers often work closely with engineers, designers, and production teams to ensure the mold meets the project's requirements.
- They provide input during the design phase to improve manufacturability and address potential challenges in the production process.
-
Ensuring Quality and Precision
- The primary goal of a mold maker is to produce molds that consistently create high-quality, identical parts.
- They conduct rigorous testing and inspection to verify the mold's accuracy and functionality before it is used in mass production.
-
Adapting to Industry Needs
- Mold makers must stay updated with advancements in materials, technologies, and manufacturing processes to remain competitive.
- They often specialize in specific industries, such as automotive or medical devices, tailoring their skills to meet the unique demands of those sectors.
-
Problem-Solving Skills
- Mold makers are problem solvers who identify and address issues during the mold creation and production process.
- Whether it's adjusting the design, repairing a damaged mold, or optimizing the manufacturing process, their expertise ensures smooth and efficient production.
By combining technical expertise, precision craftsmanship, and advanced technology, mold makers play a vital role in the manufacturing industry, enabling the production of high-quality, mass-produced components and products.
Summary Table:
Key Responsibilities | Details |
---|---|
Designing Molds | Use CAD software to create detailed blueprints, optimizing material flow and cooling systems. |
Creating Molds | Fabricate molds using CNC machines, selecting materials like steel or aluminum for durability. |
Repairing and Maintaining Molds | Inspect and repair molds to extend lifespan and ensure consistent quality. |
Utilizing Technology | Leverage CAD, CNC, 3D printing, and simulation software for precision and efficiency. |
Ensuring Quality and Precision | Conduct rigorous testing to verify mold accuracy and functionality. |
Adapting to Industry Needs | Stay updated with advancements in materials and technologies for competitive edge. |
Need precision molds for your manufacturing needs? Contact our experts today to get started!