A vibrating sieve, also known as a vibrating screen or vibrating screener, is a mechanical device designed to separate, classify, and filter materials based on particle size. It operates by using a combination of gravity, vibration, and a tilted sieve surface to move materials in a specific direction, allowing particles of different sizes to be sorted efficiently. Vibrating sieves are widely used across various industries, including food processing, pharmaceuticals, mining, construction, and agriculture, for tasks such as separating solids from liquids, removing impurities, controlling particle size distribution, and ensuring product quality. They are versatile tools that can handle both dry and wet materials, making them essential for processes like particle size analysis, safety screening, and granularity quality control.
Key Points Explained:
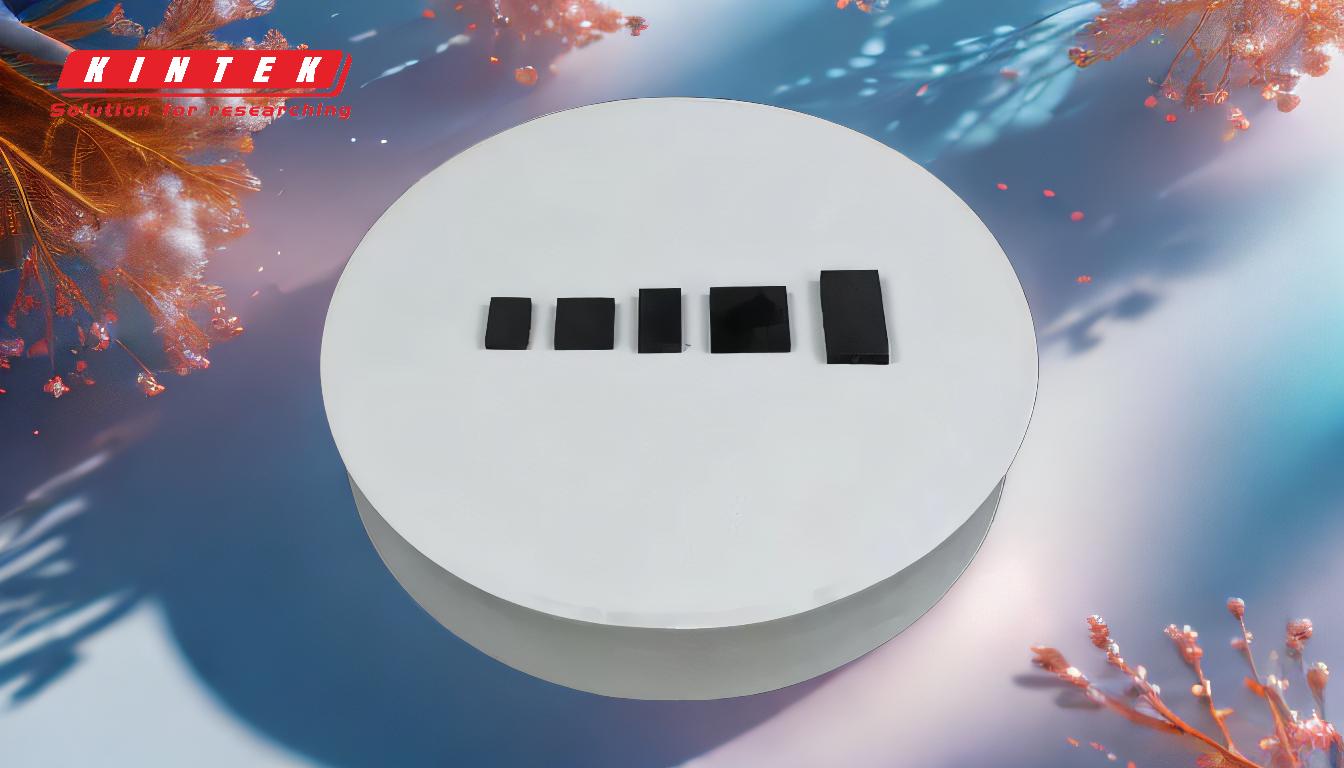
-
Primary Function of a Vibrating Sieve
- A vibrating sieve is designed to separate, classify, and filter materials based on particle size.
- It uses a combination of gravity, vibration, and a tilted sieve surface to move materials across the screen.
- The vibration motor generates mechanical vibrations that cause particles to move in a specific direction, allowing smaller particles to pass through the sieve mesh while larger particles are retained.
-
Applications Across Industries
- Food Processing: Used to screen raw materials, remove impurities, and ensure consistent particle size in food products.
- Pharmaceuticals and Chemicals: Filters powdered and granular materials, ensuring product purity and consistency.
- Mining and Metallurgy: Screens ores and minerals, separating valuable materials from waste.
- Construction: Screens sand, gravel, and cement to ensure proper particle size for building materials.
- Agriculture: Separates seeds, grains, and soil particles for quality control and processing.
- Ceramics and 3D Printing: Filters materials like alumina and quartz sand to ensure fine particle size for manufacturing.
-
Types of Vibrating Sieves
- Rotary Vibrating Sieves: Ideal for fine particle separation and classification, widely used in industries like ceramics and water treatment.
- Three-Dimensional Vibrating Screeners: Suitable for both dry and wet sieving, used in particle analysis across industries such as pharmaceuticals, food, and cosmetics.
- Laboratory Sieves: Used for particle size distribution analysis, sample preparation, and fractioning in research and quality control.
- Sieve Shakers: Designed for particle size analysis, capable of handling coarse materials and wet sieve analysis.
-
Key Benefits of Vibrating Sieves
- Efficiency: Quickly separates materials, improving production efficiency.
- Versatility: Can handle a wide range of materials, including powders, aggregates, and liquids.
- Precision: Ensures accurate particle size classification, enhancing product quality.
- Durability: Built to withstand harsh industrial environments, ensuring long-term reliability.
-
Working Mechanism
- The sieve surface is tilted, allowing gravity to assist in material movement.
- A vibration motor generates mechanical vibrations, causing particles to move across the screen.
- Smaller particles pass through the sieve mesh, while larger particles are retained or directed to a separate outlet.
- The intensity and frequency of vibration can be adjusted to suit different materials and applications.
-
Industrial Importance
- Vibrating sieves play a critical role in ensuring product quality and consistency across industries.
- They help remove impurities, waste materials, and foreign objects, improving the purity of the final product.
- By controlling particle size distribution, they optimize processes such as mixing, blending, and coating.
-
Examples of Specific Uses
- Food Industry: Screening flour, sugar, and spices to ensure uniform particle size and remove contaminants.
- Pharmaceuticals: Filtering active pharmaceutical ingredients (APIs) to meet strict quality standards.
- Mining: Separating valuable minerals from waste rock during ore processing.
- Agriculture: Cleaning and grading seeds and grains for storage or further processing.
- Ceramics: Filtering raw materials like alumina to ensure fine particle size for manufacturing.
-
Considerations for Equipment Selection
- Material Properties: Consider the type of material (dry, wet, abrasive, etc.) and its particle size range.
- Sieve Mesh Size: Choose the appropriate mesh size based on the desired particle size separation.
- Capacity Requirements: Ensure the sieve can handle the required throughput for your application.
- Durability and Maintenance: Select a sieve made from materials that can withstand the operating environment and are easy to clean and maintain.
-
Future Trends and Innovations
- Automation: Integration with automated systems for real-time monitoring and control.
- Advanced Materials: Use of durable and corrosion-resistant materials for longer lifespan.
- Energy Efficiency: Development of energy-efficient vibration motors to reduce operational costs.
- Customization: Tailored designs to meet specific industry requirements and improve performance.
By understanding the functions, applications, and benefits of vibrating sieves, equipment and consumable purchasers can make informed decisions to optimize their processes and achieve high-quality results.
Summary Table:
Aspect | Details |
---|---|
Primary Function | Separates, classifies, and filters materials based on particle size. |
Applications | Food processing, pharmaceuticals, mining, construction, agriculture, etc. |
Types | Rotary, 3D vibrating, laboratory sieves, sieve shakers. |
Key Benefits | Efficiency, versatility, precision, durability. |
Working Mechanism | Uses gravity, vibration, and tilted sieve surfaces for material movement. |
Industrial Importance | Ensures product quality, removes impurities, and optimizes processes. |
Ready to enhance your material separation process? Contact us today to find the perfect vibrating sieve for your needs!