Pulverized particles refer to materials that have been broken down into extremely small particles through processes such as crushing, grinding, or beating. This reduction in size is often done to achieve a fine, powdery consistency, which can be useful in various industrial, scientific, or commercial applications. The term "pulverized" emphasizes the thoroughness of the process, resulting in particles that are often microscopic or near-microscopic in size. This fine state can enhance properties like surface area, reactivity, or solubility, making pulverized particles valuable in fields such as pharmaceuticals, construction, and materials science.
Key Points Explained:
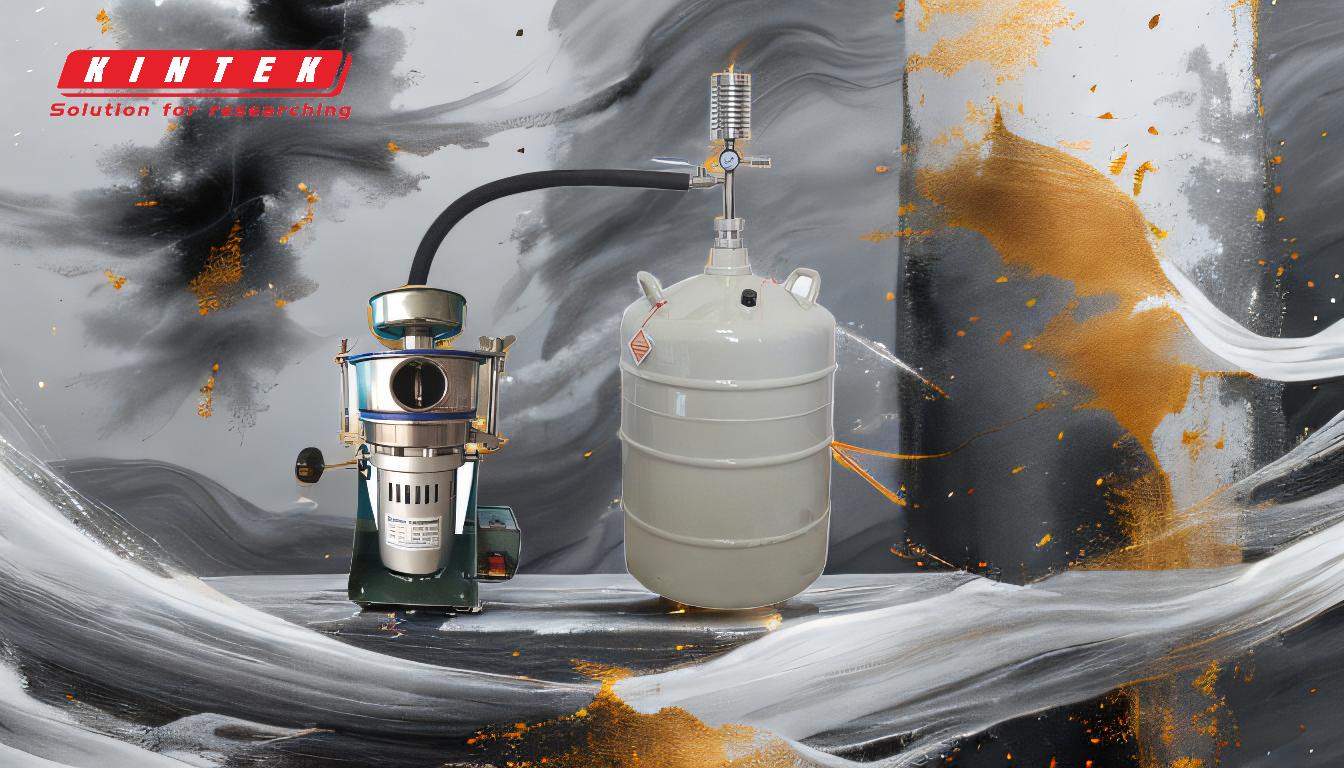
-
Definition of Pulverized Particles:
- Pulverized particles are materials that have been reduced to very small particles through mechanical processes like crushing, grinding, or beating.
- The goal is to achieve a fine, powdery consistency, often resulting in particles that are microscopic or near-microscopic in size.
-
Processes Involved in Pulverization:
- Crushing: Applying force to break down larger materials into smaller pieces.
- Grinding: Using abrasive forces to further reduce particle size, often resulting in a fine powder.
- Beating: Repeated mechanical impact to break apart materials into smaller particles.
- These processes can be performed using specialized equipment like ball mills, hammer mills, or pulverizers.
-
Characteristics of Pulverized Particles:
- Small Size: Particles are often in the micrometer or nanometer range.
- High Surface Area: The fine size increases the surface area relative to volume, which can enhance chemical reactivity or solubility.
- Uniformity: Pulverization often results in a more consistent particle size distribution, which is important for many applications.
-
Applications of Pulverized Particles:
- Pharmaceuticals: Fine particles can improve drug delivery and absorption rates.
- Construction: Pulverized materials like cement or limestone are used in building materials.
- Materials Science: Fine powders are used in manufacturing processes like 3D printing or coatings.
- Agriculture: Pulverized fertilizers or pesticides can be more evenly distributed and absorbed by plants.
-
Advantages of Pulverized Particles:
- Enhanced Reactivity: Smaller particles react more quickly due to increased surface area.
- Improved Mixing: Fine powders can be more easily blended with other materials.
- Efficient Use: Smaller particles can be used more efficiently in processes like combustion or chemical reactions.
-
Considerations for Equipment and Consumable Purchasers:
- Equipment Selection: Choose pulverizing equipment based on the material properties (e.g., hardness, moisture content) and desired particle size.
- Energy Efficiency: Evaluate the energy consumption of pulverizing processes, as finer grinding often requires more energy.
- Safety: Fine particles can pose health risks (e.g., inhalation hazards), so consider safety measures like dust collection systems.
- Cost: Balance the cost of pulverization equipment and processes with the benefits of achieving finer particles.
By understanding the concept of pulverized particles and their applications, purchasers can make informed decisions about the equipment and consumables needed for their specific requirements.
Summary Table:
Aspect | Details |
---|---|
Definition | Materials reduced to microscopic particles via crushing, grinding, or beating. |
Processes | Crushing, grinding, beating using equipment like ball mills or pulverizers. |
Characteristics | Small size, high surface area, uniformity in particle distribution. |
Applications | Pharmaceuticals, construction, materials science, agriculture. |
Advantages | Enhanced reactivity, improved mixing, efficient use in processes. |
Purchasing Considerations | Equipment selection, energy efficiency, safety measures, cost analysis. |
Ready to optimize your processes with pulverized particles? Contact our experts today for tailored solutions!