Sputter coating is a versatile nanotechnology process that transforms solid materials into microscopic particles, which are then deposited as thin films on various surfaces. This technique is widely used across multiple industries, including healthcare, electronics, and energy. In the medical field, sputter coating enhances the performance of implants through methods like ion-assisted deposition. In electronics, it plays a crucial role in semiconductor and computer chip production, as well as in the manufacturing of components for displays and solar cells. Additionally, sputter coating is integral to creating anti-reflective glass, decorative coatings, and even computer hard disks. The process has evolved from simple DC diode sputtering to more advanced methods, addressing challenges like low deposition rates and material limitations.
Key Points Explained:
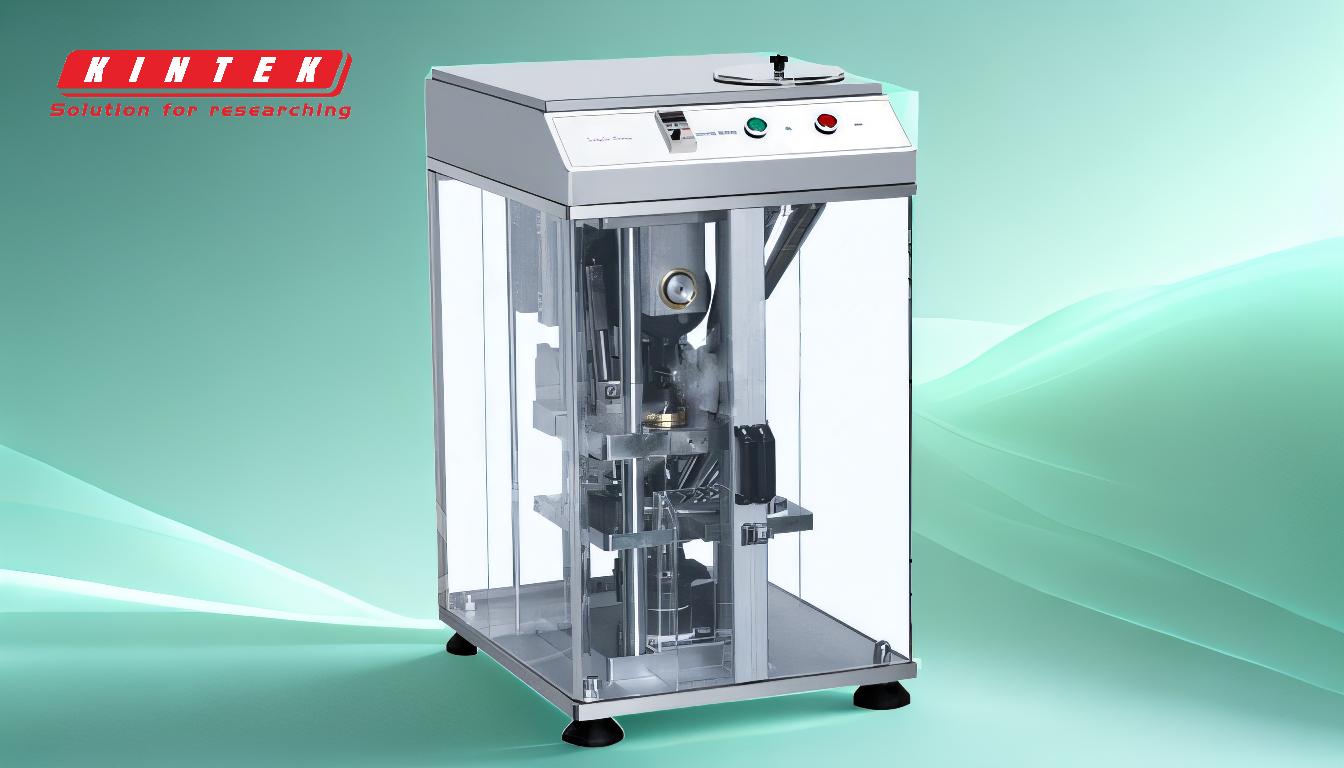
-
What is Sputter Coating?
- Sputter coating is a nanotechnology-based process that converts solid materials into microscopic particles, which are then applied as thin films onto surfaces. This process often requires specialized chilling to manage the heat generated during the transformation.
-
Applications in the Healthcare Industry
- Sputter coating is used in medical implants through advanced methods like ion-assisted deposition. This application enhances the durability and functionality of implants, driving demand in the healthcare sector.
-
Role in Semiconductor and Electronics Manufacturing
- Sputter deposition is critical in the production of semiconductors and computer chips. It is also used in creating components for TFT-LCD displays, such as source, drain, and gate electrodes, as well as transparent films and electrodes for color filters.
-
Commercial and Industrial Uses
- The technology is employed in a wide range of commercial applications, including:
- Architectural and anti-reflective glass coatings.
- Solar technology, particularly in the production of thin-film solar cells.
- Display web coating for electronic devices.
- Automotive and decorative coatings.
- Tool bit coatings for enhanced durability.
- Production of computer hard disks.
- Integrated circuit processing.
- Metal coatings for CDs and DVDs.
- The technology is employed in a wide range of commercial applications, including:
-
Historical and Technological Evolution
- Sputter coating began with simple DC diode sputtering, which, while straightforward, had limitations such as low deposition rates and an inability to coat insulating materials. Advances like DC triple sputtering and quadrupole sputtering have improved ionization and discharge stability, though challenges like low plasma concentration and deposition rates persist.
-
Future Trends and Innovations
- Recent advancements include the use of sputter films in transparent and metal electrodes for thin-film solar cells, highlighting the technology's growing role in renewable energy. Continued innovation in sputter coating methods is expected to address current limitations and expand its applications further.
By understanding these key points, equipment and consumable purchasers can better appreciate the versatility and importance of sputter coating across various industries, ensuring informed decision-making when selecting technologies for specific applications.
Summary Table:
Key Aspect | Details |
---|---|
What is Sputter Coating? | Converts solid materials into microscopic particles for thin film deposition. |
Healthcare Applications | Enhances medical implants via ion-assisted deposition. |
Electronics Manufacturing | Critical for semiconductors, computer chips, and display components. |
Commercial Uses | Anti-reflective glass, solar cells, decorative coatings, and hard disks. |
Technological Evolution | Advanced from DC diode to quadrupole sputtering for better performance. |
Future Trends | Expanding use in renewable energy and transparent electrodes. |
Interested in how sputter coating can benefit your industry? Contact us today to learn more!