The operation of a ball mill is influenced by a variety of factors that determine its efficiency, productivity, and the quality of the final product. These factors include the design and dimensions of the mill, the properties of the material being ground, the characteristics of the grinding media, and operational parameters such as rotation speed and feed rate. Understanding these factors is crucial for optimizing ball mill performance and ensuring consistent output.
Key Points Explained:
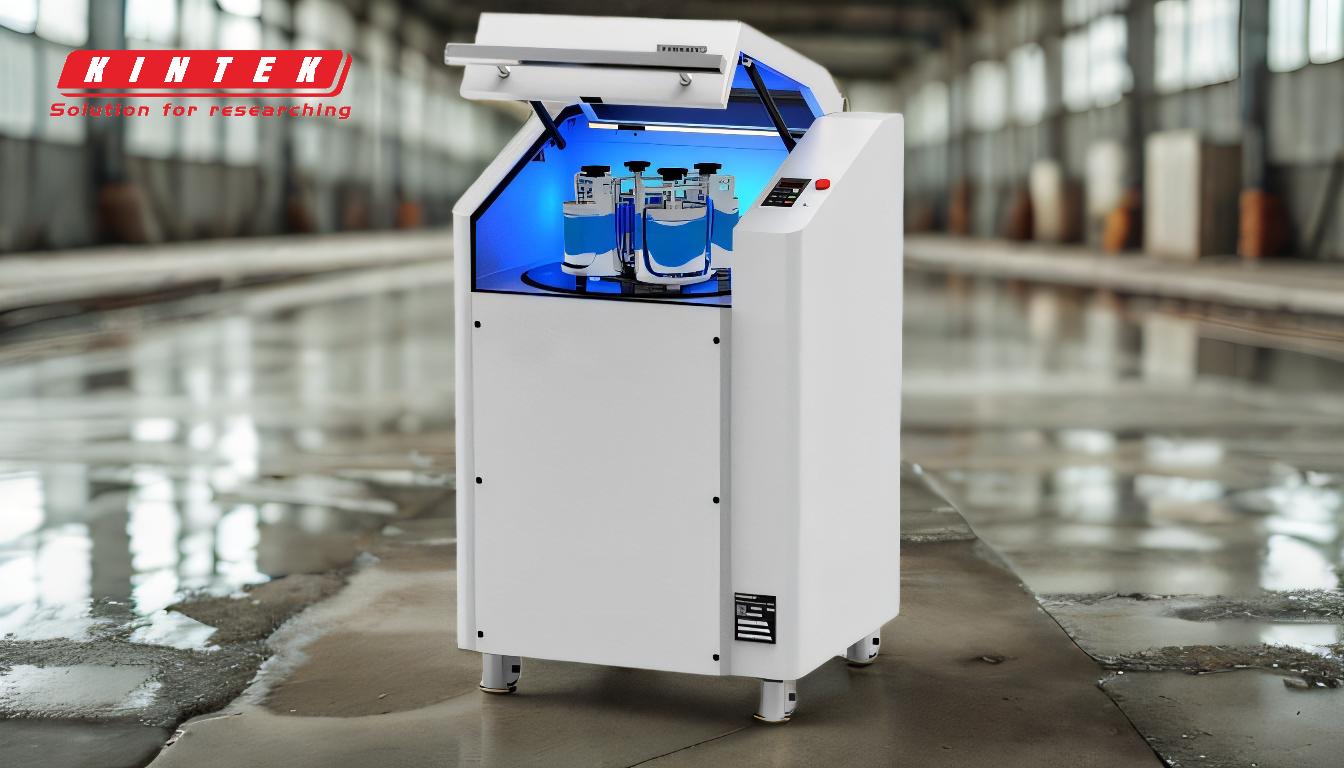
-
Drum Dimensions and Design:
- Drum Diameter and Length-to-Diameter (L:D) Ratio: The size of the drum and its L:D ratio significantly impact the grinding efficiency. An optimal L:D ratio of 1.56–1.64 ensures effective grinding by balancing the material residence time and energy consumption.
- Armor Surface Shape: The internal surface of the drum, often lined with armor, affects the movement of the grinding media and material. A well-designed surface can enhance grinding efficiency by promoting better cascading and impact forces.
-
Grinding Media Characteristics:
- Ball Size and Density: The size and density of the grinding balls influence the energy transfer and impact forces during grinding. Larger balls are more effective for coarse grinding, while smaller balls are better for fine grinding.
- Ball Filling Ratio: The percentage of the mill volume filled with grinding media (typically 30–40%) affects the grinding efficiency. Overfilling can reduce efficiency, while underfilling may lead to insufficient grinding.
-
Material Properties:
- Physical-Chemical Properties: The hardness, brittleness, and moisture content of the feed material affect how easily it can be ground. Harder materials require more energy and may necessitate adjustments in grinding media or operational parameters.
- Feed Rate and Level: The rate at which material is fed into the mill and the level of material in the vessel influence the residence time and grinding efficiency. Overloading can reduce grinding effectiveness, while underloading may lead to excessive wear on the grinding media.
-
Operational Parameters:
- Rotation Speed: The speed at which the drum rotates determines the motion of the grinding media. Optimal rotation speed ensures that the balls cascade and impact the material effectively. Too high or too low speeds can reduce grinding efficiency.
- Milling Fineness: The desired fineness of the ground product affects the grinding time and energy consumption. Finer grinding requires longer residence times and more energy.
- Timely Removal of Ground Product: Efficient removal of the ground material from the mill prevents over-grinding and ensures consistent product quality. Poor removal can lead to re-grinding and energy wastage.
-
Residence Time:
- The amount of time the material spends in the mill chamber affects the degree of grinding. Longer residence times allow for finer grinding but may also increase energy consumption and wear on the grinding media.
-
Environmental and Maintenance Factors:
- Temperature and Humidity: These can affect the material properties and the grinding process. For example, high humidity can cause material clumping.
- Maintenance of Equipment: Regular maintenance of the mill, including the armor lining and grinding media, ensures consistent performance and prevents unexpected downtime.
By carefully controlling and optimizing these factors, operators can achieve efficient and effective ball mill operation, leading to higher productivity and better-quality ground products.
Summary Table:
Factor | Key Details |
---|---|
Drum Dimensions | Optimal L:D ratio (1.56–1.64); armor surface design enhances grinding efficiency. |
Grinding Media | Ball size, density, and filling ratio (30–40%) affect grinding efficiency. |
Material Properties | Hardness, brittleness, moisture, feed rate, and level influence grinding ease. |
Operational Parameters | Rotation speed, milling fineness, and timely removal of ground product. |
Residence Time | Longer times allow finer grinding but increase energy consumption. |
Environmental Factors | Temperature, humidity, and regular maintenance ensure consistent performance. |
Optimize your ball mill operation today—contact our experts for tailored solutions!