A biochar reactor is a specialized equipment used in the pyrolysis process to convert biomass into biochar, a carbon-rich material. It typically consists of several key components, including a kettle body, a kettle cover, a jacket, a stirrer, a transmission device, and a shaft sealing device. These components work together to ensure efficient and controlled pyrolysis, which is essential for producing high-quality biochar. The reactor's design allows for precise temperature control, uniform heating, and effective mixing of biomass, all of which are crucial for optimizing the biochar production process.
Key Points Explained:
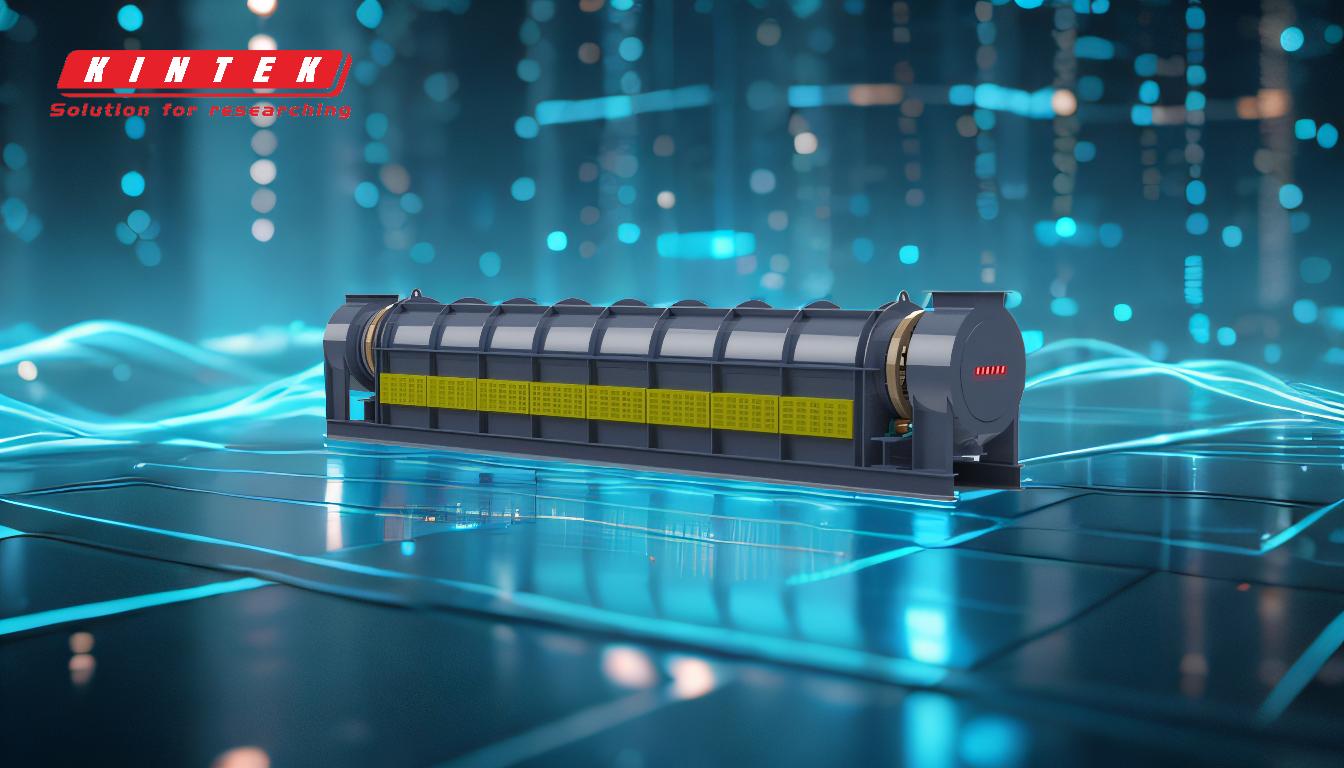
-
Kettle Body:
- The kettle body is the main chamber of the reactor where the biomass is loaded and the pyrolysis process takes place. It is designed to withstand high temperatures and pressures, ensuring the safety and efficiency of the process.
- The material of the kettle body is usually made of high-quality stainless steel or other heat-resistant alloys to endure the harsh conditions of pyrolysis.
-
Kettle Cover:
- The kettle cover seals the top of the reactor, preventing the escape of gases and maintaining the necessary pressure inside the chamber. It often includes ports for loading biomass and for the insertion of temperature probes or other monitoring devices.
- The cover is typically equipped with a locking mechanism to ensure a tight seal, which is crucial for maintaining the integrity of the pyrolysis process.
-
Jacket:
- The jacket surrounds the kettle body and is used to circulate a heating medium, such as thermal oil or steam, to provide uniform heating to the biomass. This ensures that the pyrolysis process occurs evenly throughout the biomass, leading to consistent biochar quality.
- The jacket also helps in cooling the reactor after the process is complete, which is important for safety and for preparing the reactor for the next batch.
-
Stirrer:
- The stirrer is a mechanical device that mixes the biomass inside the reactor, ensuring that all parts of the material are exposed to the same temperature and conditions. This is critical for achieving uniform pyrolysis and preventing hot spots or uneven heating.
- The stirrer is usually driven by a motor and can be designed with various blade configurations to optimize the mixing process for different types of biomass.
-
Transmission Device:
- The transmission device includes the motor and gearbox that drive the stirrer. It is responsible for providing the necessary torque and speed to ensure effective mixing of the biomass.
- The transmission device is designed to operate reliably under high temperatures and continuous operation, which are typical conditions in a biochar reactor.
-
Shaft Sealing Device:
- The shaft sealing device is crucial for preventing the leakage of gases and maintaining the pressure inside the reactor. It seals the area where the stirrer shaft passes through the kettle cover.
- High-quality seals are used to ensure that the reactor remains airtight, which is essential for the efficient and safe operation of the pyrolysis process.
In summary, a biochar reactor is a complex piece of equipment designed to facilitate the pyrolysis of biomass into biochar. Each component plays a vital role in ensuring the process is efficient, safe, and produces high-quality biochar. Understanding the function and importance of each part can help in selecting the right reactor for specific biochar production needs.
Summary Table:
Component | Function |
---|---|
Kettle Body | Main chamber for pyrolysis; withstands high temperatures and pressures. |
Kettle Cover | Seals the reactor, maintains pressure, and includes ports for monitoring. |
Jacket | Circulates heating medium for uniform heating and cooling. |
Stirrer | Mixes biomass for even pyrolysis and prevents hot spots. |
Transmission Device | Drives the stirrer with reliable torque and speed. |
Shaft Sealing Device | Prevents gas leakage and maintains reactor pressure. |
Ready to optimize your biochar production? Contact us today to find the perfect biochar reactor for your needs!