Activated carbon is a highly porous material widely used for adsorption of contaminants from air and water. Over time, the adsorption capacity of activated carbon diminishes as its pores become saturated with adsorbed substances. Regeneration of spent activated carbon is essential to restore its adsorption capacity and extend its usable life. A common method for regenerating spent activated carbon is chemical regeneration, which involves using chemicals such as hydrochloric acid and hot water to remove adsorbed contaminants and restore the carbon's porosity.
Key Points Explained:
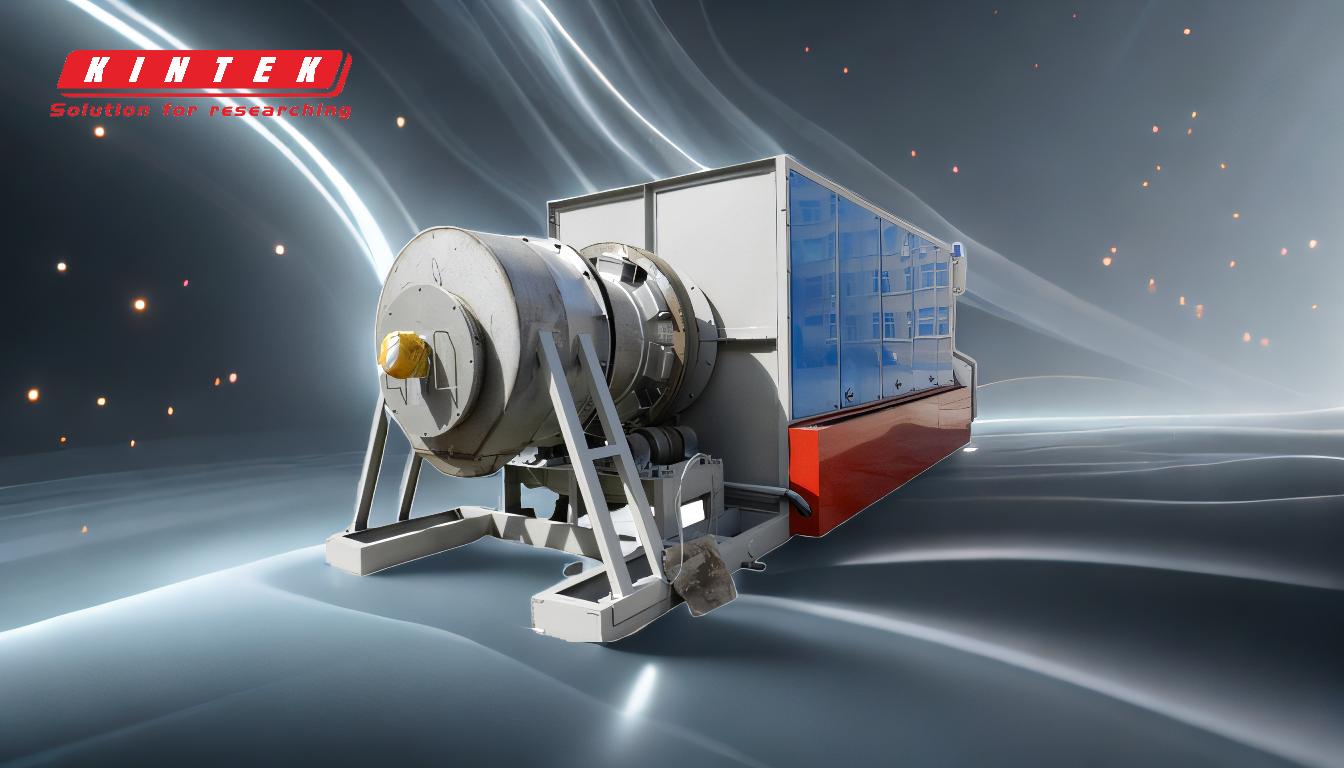
-
What is Activated Carbon and Why Regenerate It?
- Activated carbon is a porous material with a large surface area, making it effective for adsorbing contaminants from gases and liquids.
- Over time, the pores of activated carbon become filled with adsorbed substances, reducing its effectiveness.
- Regeneration restores the adsorption capacity of spent activated carbon, making it reusable and cost-effective.
-
Chemical Regeneration as a Common Method
- Chemical regeneration is a widely used method for restoring spent activated carbon.
- This process involves treating the carbon with chemicals to desorb and remove the contaminants trapped in its pores.
-
Role of Hydrochloric Acid in Chemical Regeneration
- Hydrochloric acid (HCl) is a strong acid commonly used in chemical regeneration.
- It helps dissolve and remove inorganic contaminants, such as metal ions, that may be adsorbed on the carbon surface.
- The acid treatment also helps break down organic contaminants, making them easier to wash away.
-
Use of Hot Water in the Regeneration Process
- Hot water is often used in conjunction with hydrochloric acid to enhance the regeneration process.
- The heat from the water increases the mobility of adsorbed molecules, making it easier for them to detach from the carbon surface.
- Hot water also helps flush out dissolved contaminants from the carbon pores.
-
Advantages of Chemical Regeneration
- Cost-Effectiveness: Chemical regeneration is often more economical than replacing the carbon entirely.
- Environmental Benefits: Reusing activated carbon reduces waste and the need for new carbon production.
- Efficiency: Chemical regeneration can restore a significant portion of the carbon's adsorption capacity, depending on the type and concentration of contaminants.
-
Limitations of Chemical Regeneration
- Chemical Waste: The process generates chemical waste, which must be properly treated and disposed of to avoid environmental harm.
- Selective Effectiveness: Chemical regeneration may not be equally effective for all types of contaminants, particularly complex organic compounds.
- Carbon Loss: Repeated chemical regeneration can lead to some loss of carbon material over time.
-
Applications of Regenerated Activated Carbon
- Regenerated activated carbon can be reused in various applications, including:
- Water treatment (e.g., removing organic pollutants, chlorine, and heavy metals).
- Air purification (e.g., capturing volatile organic compounds and odors).
- Industrial processes (e.g., solvent recovery and gas separation).
- Regenerated activated carbon can be reused in various applications, including:
-
Alternative Regeneration Methods
- While chemical regeneration is common, other methods include:
- Thermal Regeneration: Heating the carbon to high temperatures to burn off adsorbed contaminants.
- Steam Regeneration: Using steam to desorb volatile contaminants.
- Biological Regeneration: Utilizing microorganisms to degrade adsorbed organic contaminants.
- While chemical regeneration is common, other methods include:
In conclusion, chemical regeneration using hydrochloric acid and hot water is a practical and effective method for restoring the adsorption capacity of spent activated carbon. This method offers a balance of cost-effectiveness, efficiency, and environmental benefits, making it a preferred choice in many industries. However, it is essential to consider the specific contaminants and operational requirements when selecting a regeneration method.
Summary Table:
Key Aspect | Details |
---|---|
What is Activated Carbon? | Porous material used for adsorbing contaminants from air and water. |
Why Regenerate? | Restores adsorption capacity, making it reusable and cost-effective. |
Chemical Regeneration | Uses hydrochloric acid and hot water to remove contaminants. |
Advantages | Cost-effective, environmentally friendly, and efficient. |
Limitations | Generates chemical waste, selective effectiveness, and potential carbon loss. |
Applications | Water treatment, air purification, and industrial processes. |
Alternative Methods | Thermal, steam, and biological regeneration. |
Need help regenerating activated carbon? Contact our experts today for tailored solutions!