A fluidized bed chemical reaction is a process where a fluid (liquid or gas) is passed through a solid granular material at high velocities, causing the solid particles to suspend and behave like a fluid. This creates a fluidized bed, which enhances heat and mass transfer, making it highly efficient for chemical reactions. The process begins at the minimum fluidization velocity, where the fluid force balances the weight of the solid material. Beyond this velocity, the solid material expands and swirls, creating a dynamic environment for chemical reactions. Fluidized bed reactors are widely used in industries such as fuel production, polymer manufacturing, and waste treatment due to their efficiency, rapid reaction rates, and ability to handle large throughputs.
Key Points Explained:
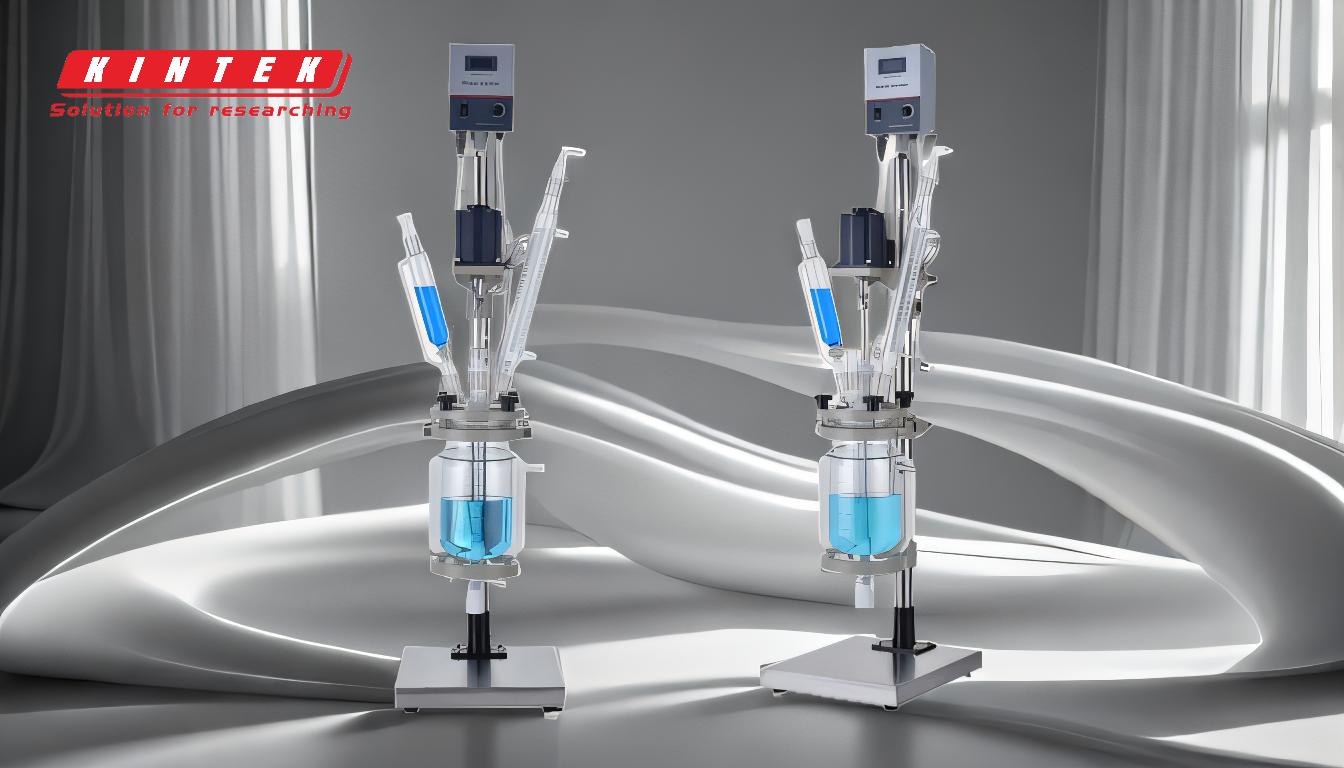
-
Definition of Fluidized Bed Chemical Reaction:
- A fluidized bed chemical reaction involves passing a fluid (gas or liquid) through a solid granular material at high velocities, causing the solid particles to suspend and behave like a fluid.
- This process begins at the minimum fluidization velocity, where the fluid force balances the weight of the solid material, creating a fluidized bed.
-
Mechanism of Fluidization:
- Fluidization occurs when the fluid velocity exceeds the minimum fluidization velocity, causing the solid particles to expand and swirl.
- This dynamic environment enhances heat and mass transfer, making it highly efficient for chemical reactions.
-
Components of a Fluidized Bed Reactor:
- Bed Material: Typically inert materials like sand are used at the bottom of the reactor to provide fluid dynamic stability and assist in heat transfer.
- Fluid: A gas, often pure nitrogen, is introduced at the bottom to maintain an inert atmosphere, prevent unwanted chemical reactions, and fluidize the particles.
- Heat Transfer: The bed material efficiently transfers heat to the substrate undergoing chemical reactions, ensuring uniform temperature distribution.
-
Types of Fluidized Bed Reactors:
- Bubbling Fluidized Bed Reactors: Operate at lower gas velocities, suitable for processes requiring moderate heat transfer and reaction rates.
- Circulating Fluidized Bed Reactors: Operate at higher gas velocities, leading to more attrited char and higher char content in products like bio-oil. They are suitable for very large throughputs and often use recirculated heated sand from a secondary char combustor.
-
Applications of Fluidized Bed Reactors:
- Fuel Production: Used in the production of gasoline, other fuels, and coal gasification.
- Polymer Manufacturing: Employed in the production of industrially important polymers such as rubber, vinyl chloride, polyethylene, styrenes, and polypropylene.
- Waste Treatment: Utilized in water and waste treatment processes, offering cleaner and more efficient solutions compared to traditional reactor technologies.
- Bio-oil Production: Maximize the production of liquid products like bio-oil by using inert elements such as sand to provide fluid dynamic stability and assist in biomass heating.
-
Advantages of Fluidized Bed Reactors:
- Rapid Reaction and Heat Transfer: The dynamic environment of the fluidized bed ensures rapid chemical reactions and efficient heat transfer.
- Wide Contact Area: The fluidized bed provides a large contact area between the fluid and solid particles, enhancing the reaction efficiency.
- High Comparative Velocity: The high velocity of the fluid ensures uniform mixing and prevents the formation of hot spots, leading to consistent product quality.
- Scalability: Fluidized bed reactors are highly scalable, making them suitable for both laboratory-scale experiments and large-scale industrial applications.
-
Challenges and Considerations:
- Erosion and Attrition: The high velocity of the fluid can cause erosion and attrition of the solid particles, leading to the need for frequent maintenance and replacement of bed materials.
- Gas Distribution: Ensuring uniform gas distribution is critical to maintaining the fluidized state and achieving consistent reaction rates.
- Temperature Control: Precise temperature control is necessary to prevent unwanted side reactions and ensure the desired product quality.
In summary, fluidized bed chemical reactions are a versatile and efficient method for conducting chemical reactions in various industrial applications. The unique properties of fluidized beds, such as rapid heat and mass transfer, wide contact area, and scalability, make them an attractive choice for industries ranging from fuel production to polymer manufacturing and waste treatment. However, careful consideration of challenges such as erosion, gas distribution, and temperature control is essential to maximize the benefits of fluidized bed reactors.
Summary Table:
Aspect | Details |
---|---|
Definition | Fluid passes through solid granular material, creating a fluidized bed. |
Mechanism | Exceeds minimum fluidization velocity, enhancing heat and mass transfer. |
Components | Bed material (e.g., sand), fluid (e.g., nitrogen), and heat transfer system. |
Types | Bubbling and circulating fluidized bed reactors. |
Applications | Fuel production, polymer manufacturing, waste treatment, and bio-oil. |
Advantages | Rapid reaction, wide contact area, high velocity, and scalability. |
Challenges | Erosion, gas distribution, and temperature control. |
Interested in optimizing your chemical processes with fluidized bed reactors? Contact our experts today to learn more!