A reactor in pyrolysis is the central component where the thermal decomposition of materials occurs in the absence of oxygen. It is designed to facilitate the cracking of raw materials into smaller molecules, producing oil, gas, and other byproducts. The reactor's design, rotation mechanism, and heat management are critical for efficient pyrolysis. Supporting rollers and driving devices ensure smooth operation, while specific reactor types, such as fluidized bed reactors or ablative reactors, cater to different pyrolysis processes. The reactor's quality and functionality directly impact the safety, efficiency, and output of the pyrolysis system.
Key Points Explained:
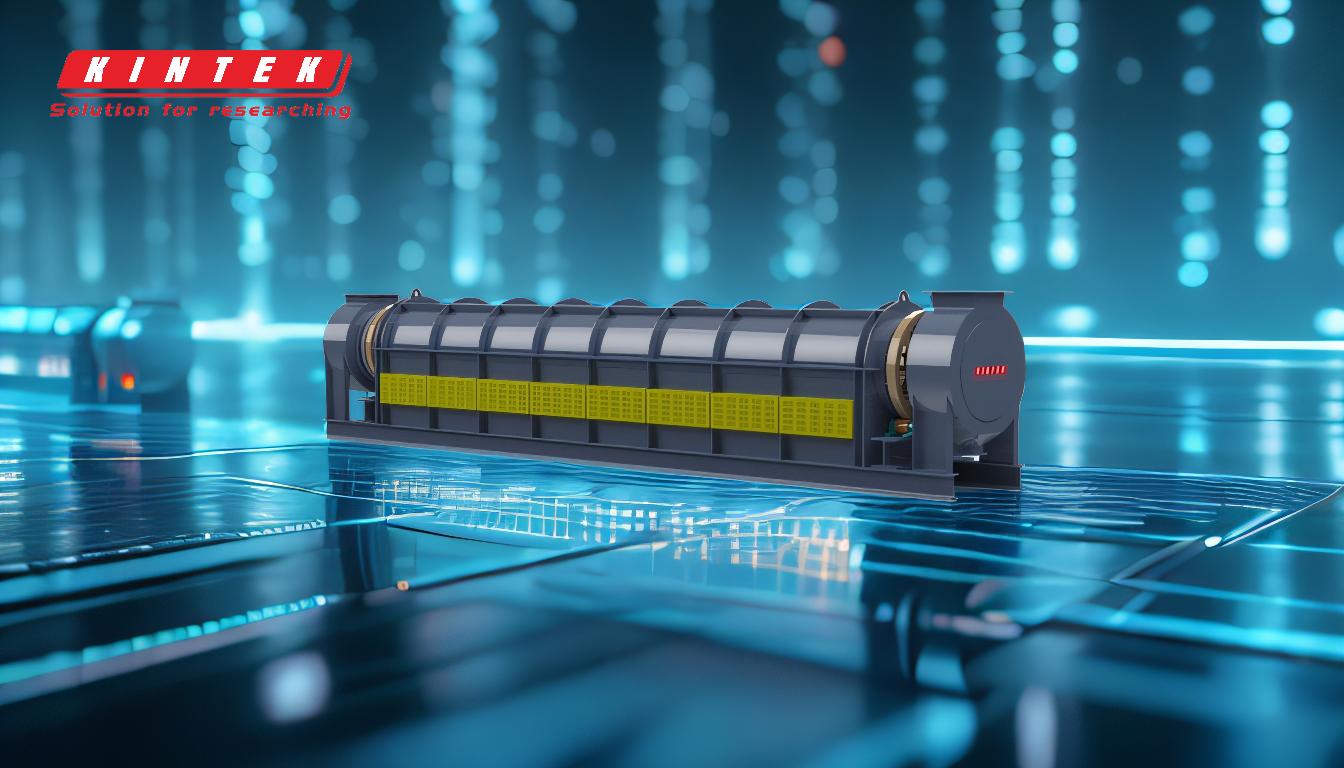
-
Core Function of the Reactor:
- The reactor is the heart of the pyrolysis system, where raw materials undergo thermal cracking in the absence of oxygen. This process breaks down large organic molecules into smaller ones, producing oil, gas, and fine coke.
- The absence of oxygen prevents combustion, reducing CO₂ emissions and ensuring energy-rich reaction products.
-
Design and Rotation Mechanism:
- The reactor rotates under the power of a driving device, which includes a motor, reducer, and spring base. This rotation ensures uniform heat distribution and efficient cracking of materials.
- Forward and reverse rotation can be controlled via an electric control cabinet, optimizing the pyrolysis process.
-
Supporting Components:
- Supporting rollers bear the weight of the reactor and its contents. For instance, in a 10T pyrolysis plant, rollers must support up to 20T, ensuring stability and safety.
- The driving device's cylindrical gear reducer and spring compensation system ensure smooth operation and perfect gear meshing.
-
Types of Reactors:
- Fluidized Bed Reactor: Separates waste flows into two zones—a bed section (low oxygen for drying, pyrolysis, and gasification) and a free section (secondary air addition for further burning). This design ensures efficient pyrolysis with minimal emissions.
- Ablative Pyrolysis Reactor: Operates as a pressure-driven system, requiring an external heat supply of 450-600°C. It is ideal for fast pyrolysis of biomass without needing excessive heat.
-
Heat Management and Temperature Control:
- The reactor must maintain precise temperatures (e.g., 475-550°C for flash pyrolysis) to ensure effective cracking without combustion.
- Heat is supplied externally, and the reactor's design ensures optimal heat absorption by the raw materials.
-
Impact on Safety and Efficiency:
- The reactor's quality and design directly influence the pyrolysis unit's normal operation, safety of personnel, and equipment durability.
- Properly designed reactors minimize risks, such as overheating or mechanical failures, while maximizing output efficiency.
-
Applications and Output:
- Reactors are used in various pyrolysis applications, including waste management, biomass conversion, and energy production.
- The output includes oil, gas, and fine coke, which can be further processed or used as energy sources.
By understanding these key points, a purchaser of pyrolysis equipment can make informed decisions about reactor selection, ensuring optimal performance, safety, and efficiency for their specific needs.
Summary Table:
Key Aspect | Details |
---|---|
Core Function | Thermal cracking of raw materials in the absence of oxygen. |
Design & Rotation | Rotates for uniform heat distribution; controlled via electric cabinet. |
Supporting Components | Supporting rollers and driving devices ensure stability and smooth operation. |
Types of Reactors | Fluidized bed reactors and ablative reactors for different processes. |
Heat Management | Maintains precise temperatures (e.g., 475-550°C) for effective cracking. |
Safety & Efficiency | High-quality design minimizes risks and maximizes output efficiency. |
Applications | Used in waste management, biomass conversion, and energy production. |
Discover the right pyrolysis reactor for your needs—contact our experts today!