A roller mill is a versatile piece of equipment used primarily in the grinding and processing of various materials, including grains, minerals, and other solids. It operates by passing the material between rotating rollers, which apply pressure to crush or grind the material into smaller particles. Roller mills are widely used in industries such as agriculture (for grain milling), mining (for ore processing), and manufacturing (for powder production). They are valued for their efficiency, precision, and ability to produce uniform particle sizes, making them essential in processes where consistency and quality are critical.
Key Points Explained:
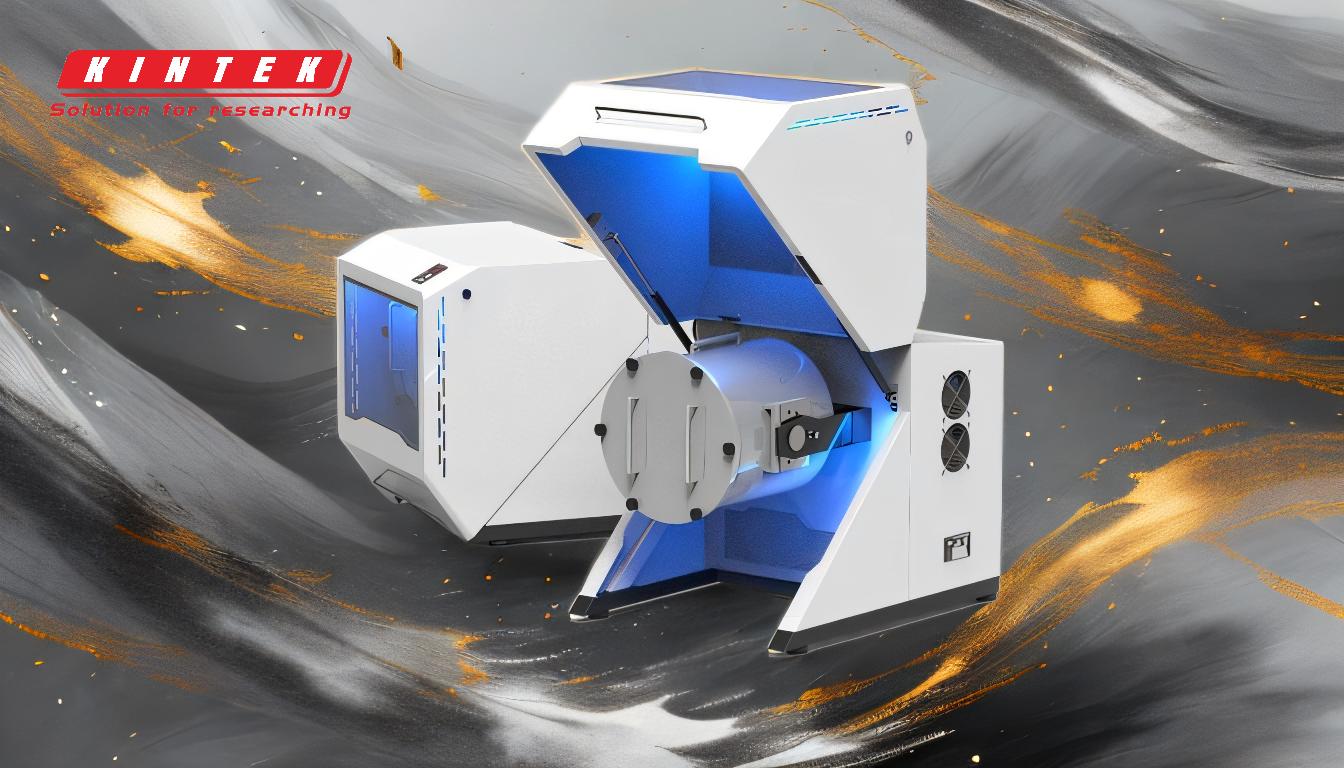
-
Primary Function of a Roller Mill
- A roller mill is designed to grind, crush, or pulverize materials into smaller, more uniform particles.
- It achieves this by passing the material between two or more rotating rollers, which apply compressive force to break down the material.
- This process is highly efficient and produces consistent results, making it ideal for applications requiring precise particle size control.
-
Applications in Agriculture
- Roller mills are extensively used in the agricultural industry for processing grains such as wheat, corn, and barley.
- They are employed in flour production, where they grind grains into fine flour while preserving the nutritional quality of the product.
- The ability to adjust the gap between rollers allows for customization of the grind, catering to different types of flour or feed requirements.
-
Applications in Mining and Mineral Processing
- In the mining industry, roller mills are used to crush and grind ores and minerals into fine powders.
- This is a critical step in the extraction of valuable metals and minerals, as it prepares the material for further processing, such as chemical leaching or smelting.
- Roller mills are preferred for their ability to handle hard and abrasive materials efficiently.
-
Applications in Manufacturing and Powder Production
- Roller mills are also used in manufacturing industries to produce powders for various applications, such as pharmaceuticals, ceramics, and chemicals.
- They are capable of producing ultra-fine powders with precise particle size distributions, which are essential for product consistency and performance.
- The versatility of roller mills allows them to process a wide range of materials, from soft to hard and brittle to ductile.
-
Advantages of Roller Mills
- Efficiency: Roller mills are energy-efficient compared to other grinding methods, as they require less power to achieve the same results.
- Precision: The adjustable gap between rollers allows for precise control over particle size, ensuring uniformity in the final product.
- Durability: Roller mills are built to withstand heavy use and can handle abrasive materials without significant wear.
- Versatility: They can process a wide variety of materials, making them suitable for multiple industries and applications.
-
Types of Roller Mills
- Vertical Roller Mills: These mills have a vertical orientation and are commonly used in cement and mineral processing industries. They are known for their high grinding efficiency and low energy consumption.
- Horizontal Roller Mills: These mills have a horizontal orientation and are often used in agriculture for grain milling. They are easy to operate and maintain.
- Three-Roll Mills: These mills feature three rollers and are used in applications requiring ultra-fine grinding, such as in the production of inks, paints, and cosmetics.
-
Considerations for Equipment Purchasers
- Material Compatibility: Ensure the roller mill is suitable for the specific materials you intend to process, as different materials may require different roller configurations.
- Particle Size Requirements: Consider the desired particle size and uniformity, as this will determine the type of roller mill and settings needed.
- Capacity and Throughput: Evaluate the mill's capacity to ensure it meets your production volume requirements.
- Maintenance and Durability: Choose a roller mill that is easy to maintain and built to withstand the demands of your industry.
- Energy Efficiency: Opt for models that offer energy savings, as this can significantly reduce operational costs over time.
In summary, roller mills are indispensable tools in various industries, offering efficient and precise grinding solutions for a wide range of materials. Their versatility, durability, and ability to produce uniform particle sizes make them a valuable investment for equipment purchasers seeking reliable and high-performance machinery.
Summary Table:
Aspect | Details |
---|---|
Primary Function | Grinds, crushes, or pulverizes materials into smaller, uniform particles. |
Applications | Agriculture (grain milling), mining (ore processing), manufacturing (powder production). |
Advantages | High efficiency, precision, durability, and versatility. |
Types | Vertical, horizontal, and three-roll mills. |
Key Considerations | Material compatibility, particle size, capacity, maintenance, energy efficiency. |
Ready to enhance your grinding process? Contact us today to find the perfect roller mill for your needs!