Ceramic powder is a versatile material used in a wide range of applications across various industries. It is primarily composed of fine particles of ceramic materials, which can be processed into different forms such as coatings, composites, and bulk ceramics. Its unique properties, including high thermal stability, chemical resistance, and mechanical strength, make it suitable for use in electronics, aerospace, automotive, medical, and construction industries. Ceramic powder is also used in the production of advanced ceramics, such as piezoelectric devices, thermal barrier coatings, and bioceramics. Additionally, it plays a crucial role in traditional ceramics, including pottery, tiles, and refractory materials.
Key Points Explained:
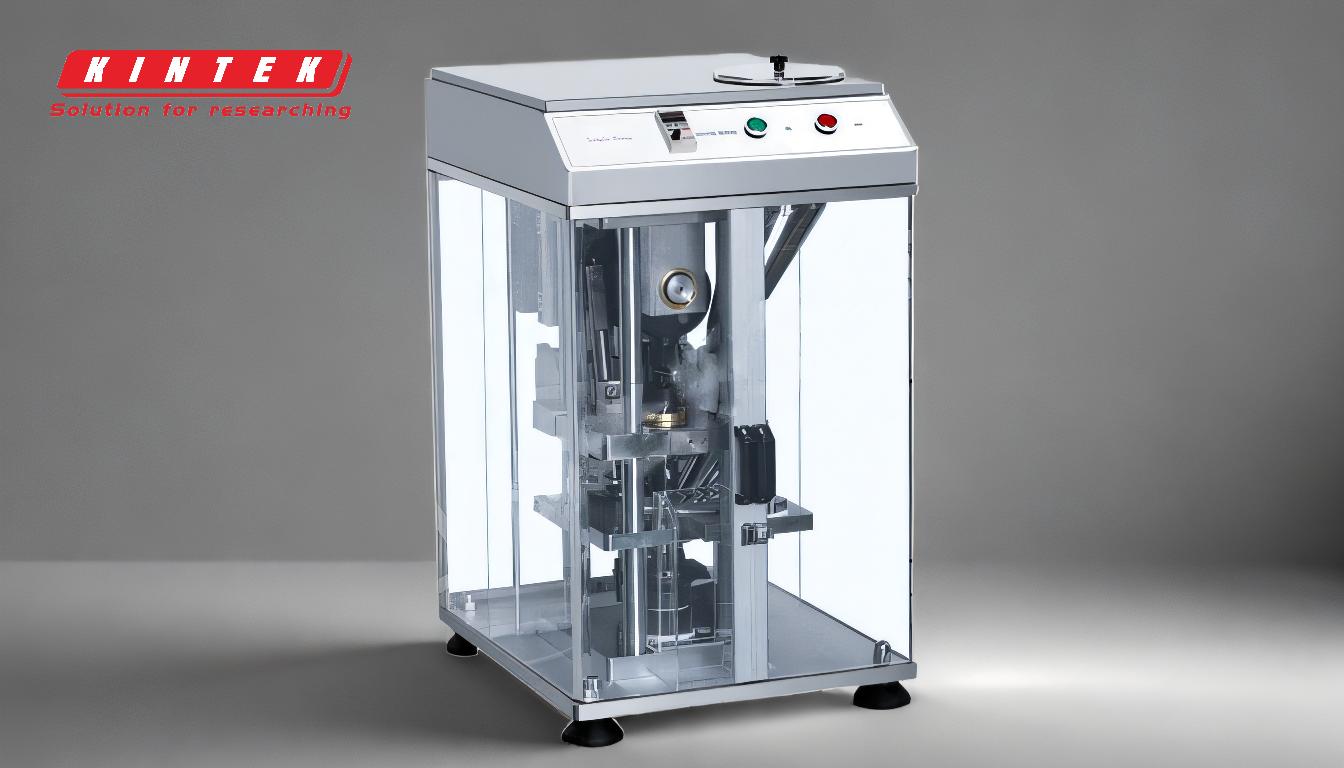
-
Composition and Properties of Ceramic Powder
- Ceramic powder is typically made from inorganic, non-metallic materials such as oxides, carbides, nitrides, or silicates.
- Its fine particle size allows for high surface area, which enhances reactivity and sintering efficiency.
- Key properties include high melting points, excellent thermal and electrical insulation, and resistance to wear and corrosion.
-
Applications in Advanced Ceramics
- Electronics: Ceramic powder is used in capacitors, insulators, and substrates for integrated circuits due to its dielectric properties.
- Piezoelectric Devices: It is essential in producing sensors, actuators, and transducers that convert mechanical energy into electrical signals.
- Thermal Barrier Coatings: Applied in aerospace and automotive industries to protect components from extreme temperatures.
- Bioceramics: Used in medical implants, such as dental crowns and bone replacements, due to its biocompatibility and durability.
-
Traditional Ceramics
- Pottery and Tiles: Ceramic powder is a fundamental material in creating decorative and functional items like pottery, tiles, and sanitaryware.
- Refractory Materials: Used in furnaces, kilns, and reactors to withstand high temperatures and harsh chemical environments.
-
Industrial and Manufacturing Uses
- Abrasive Materials: Ceramic powders are used in grinding and polishing applications due to their hardness and wear resistance.
- Coatings: Applied to surfaces to enhance durability, thermal insulation, or chemical resistance.
- Additive Manufacturing: Utilized in 3D printing to create complex ceramic components with high precision.
-
Emerging Applications
- Energy Storage: Ceramic powders are being explored for use in solid-state batteries and fuel cells.
- Environmental Applications: Used in filters and catalysts for pollution control and water purification.
- Nanotechnology: Ceramic nanoparticles are being developed for advanced materials with enhanced properties.
-
Processing Techniques
- Ceramic powder is processed using methods like sintering, hot pressing, and injection molding to form dense and durable ceramic products.
- Advanced techniques, such as spark plasma sintering, enable the production of ceramics with superior mechanical and thermal properties.
In summary, ceramic powder is a critical material in both traditional and modern industries, offering a wide range of applications due to its exceptional properties. Its role in advanced technologies and emerging fields continues to expand, making it an indispensable component in material science and engineering.
Summary Table:
Category | Applications |
---|---|
Advanced Ceramics | Electronics, piezoelectric devices, thermal barrier coatings, bioceramics |
Traditional Ceramics | Pottery, tiles, refractory materials |
Industrial Uses | Abrasive materials, coatings, additive manufacturing |
Emerging Applications | Energy storage, environmental applications, nanotechnology |
Processing Techniques | Sintering, hot pressing, injection molding, spark plasma sintering |
Unlock the potential of ceramic powder for your next project—contact us today to learn more!