Evaporation and sputtering are both physical vapor deposition (PVD) techniques used to create thin films, but they differ significantly in their mechanisms, operational conditions, and outcomes. Evaporation involves heating a material until it vaporizes, forming a vapor stream that condenses on a substrate. In contrast, sputtering uses energetic ions to collide with a target material, ejecting atoms that deposit onto a substrate. Sputtering operates at higher gas pressures and provides better film adhesion and homogeneity, while evaporation offers higher deposition rates and is more suitable for high-temperature materials. Below, the key differences are explained in detail.
Key Points Explained:
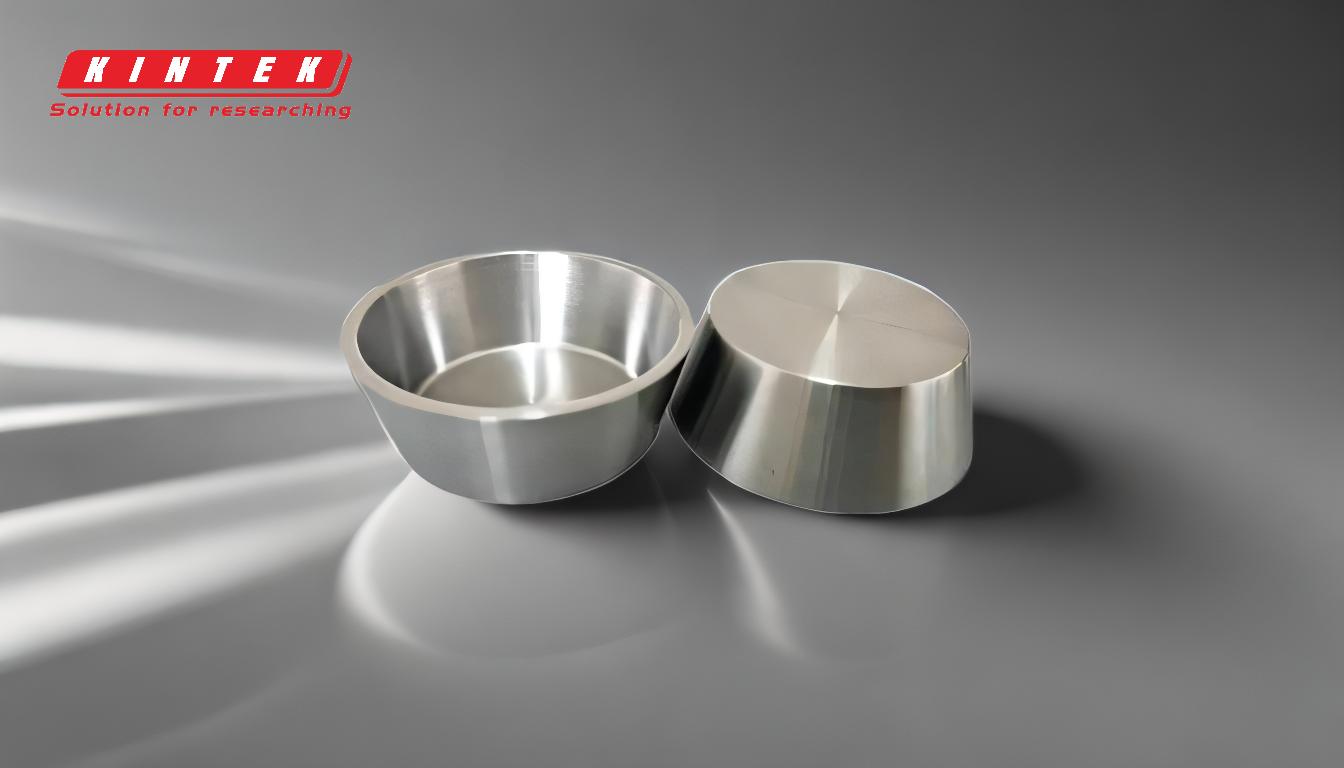
1. Mechanism of Deposition
-
Evaporation:
- Relies on thermal energy to vaporize the source material.
- The material is heated (e.g., via resistive heating or electron beam) until it reaches its vaporization temperature, creating a vapor stream.
- The vapor condenses on the substrate to form a thin film.
-
Sputtering:
- Involves bombarding a target material with energetic ions (usually argon ions) in a plasma environment.
- The collision ejects atoms or clusters from the target, which then deposit onto the substrate.
- This process is non-thermal and relies on momentum transfer rather than heat.
2. Operational Conditions
-
Evaporation:
- Requires a high vacuum environment (very low pressure) to minimize gas-phase collisions and ensure a direct line-of-sight trajectory for the vapor.
- Suitable for materials with high vaporization temperatures.
-
Sputtering:
- Operates at higher gas pressures (5-15 mTorr), where sputtered particles undergo gas-phase collisions before reaching the substrate.
- The presence of gas helps thermalize the particles, leading to better film quality.
3. Deposition Rate
-
Evaporation:
- Typically has a higher deposition rate due to the robust vapor stream produced by thermal vaporization.
- Shorter run times make it more efficient for certain applications.
-
Sputtering:
- Generally has a lower deposition rate, except for pure metals.
- The process is slower because it ejects single atoms or small clusters at a time.
4. Film Quality and Characteristics
-
Evaporation:
- Produces films with larger grain sizes and less homogeneity.
- Films may have lower adhesion due to the lack of energetic particle bombardment.
-
Sputtering:
- Results in films with smaller grain sizes, better homogeneity, and higher adhesion.
- The energetic nature of sputtered particles enhances film density and adhesion.
5. Energy of Deposited Species
-
Evaporation:
- The vaporized particles have low energy, leading to less dense films.
- This can result in higher levels of absorbed gas in the film.
-
Sputtering:
- Sputtered particles have higher energy, leading to denser films with fewer defects.
- The higher energy also reduces the amount of absorbed gas in the film.
6. Scalability and Automation
-
Evaporation:
- Less scalable for large-area coatings due to the line-of-sight nature of the process.
- Limited automation capabilities compared to sputtering.
-
Sputtering:
- Highly scalable and can be automated for large-scale production.
- Suitable for coating complex geometries due to the non-line-of-sight nature of the process.
7. Material Compatibility
-
Evaporation:
- Ideal for high-temperature materials that can withstand thermal vaporization.
- Can create alloys by co-evaporating multiple materials.
-
Sputtering:
- Compatible with a wide range of materials, including metals, alloys, and ceramics.
- Sequential sputtering can be used to create multilayer coatings.
8. Applications
-
Evaporation:
- Commonly used in applications requiring high deposition rates, such as optical coatings and metallization.
-
Sputtering:
- Preferred for applications requiring high-quality, dense films, such as semiconductor manufacturing and protective coatings.
In summary, evaporation and sputtering are distinct PVD techniques with unique advantages and limitations. Evaporation excels in high deposition rates and simplicity, making it suitable for specific high-temperature applications. Sputtering, on the other hand, offers superior film quality, scalability, and versatility, making it ideal for advanced industrial applications. The choice between the two depends on the specific requirements of the coating process, including material properties, film quality, and production scale.
Summary Table:
Aspect | Evaporation | Sputtering |
---|---|---|
Mechanism | Thermal energy vaporizes the material. | Energetic ions bombard the target, ejecting atoms. |
Operational Conditions | High vacuum environment, suitable for high-temperature materials. | Higher gas pressures (5-15 mTorr), better film quality. |
Deposition Rate | Higher deposition rates, shorter run times. | Lower deposition rates, except for pure metals. |
Film Quality | Larger grain sizes, less homogeneity, lower adhesion. | Smaller grain sizes, better homogeneity, higher adhesion. |
Energy of Deposited Species | Low-energy particles, less dense films. | High-energy particles, denser films with fewer defects. |
Scalability | Less scalable, limited automation. | Highly scalable, suitable for large-scale and complex geometries. |
Material Compatibility | Ideal for high-temperature materials and alloy creation. | Compatible with metals, alloys, ceramics, and multilayer coatings. |
Applications | Optical coatings, metallization. | Semiconductor manufacturing, protective coatings. |
Need help choosing the right PVD technique for your project? Contact our experts today for personalized guidance!