Film uniformity refers to the consistency of a thin film's properties, particularly thickness, across the entire surface of a substrate, such as a wafer. Good uniformity ensures that the film's thickness is nearly identical at every point on the substrate, which is critical for the performance and reliability of semiconductor devices and other applications. Uniformity can also extend to other film properties, such as the index of refraction, depending on the specific application. Achieving high uniformity is essential to avoid over- or under-specifying requirements, which can impact manufacturing efficiency and product quality.
Key Points Explained:
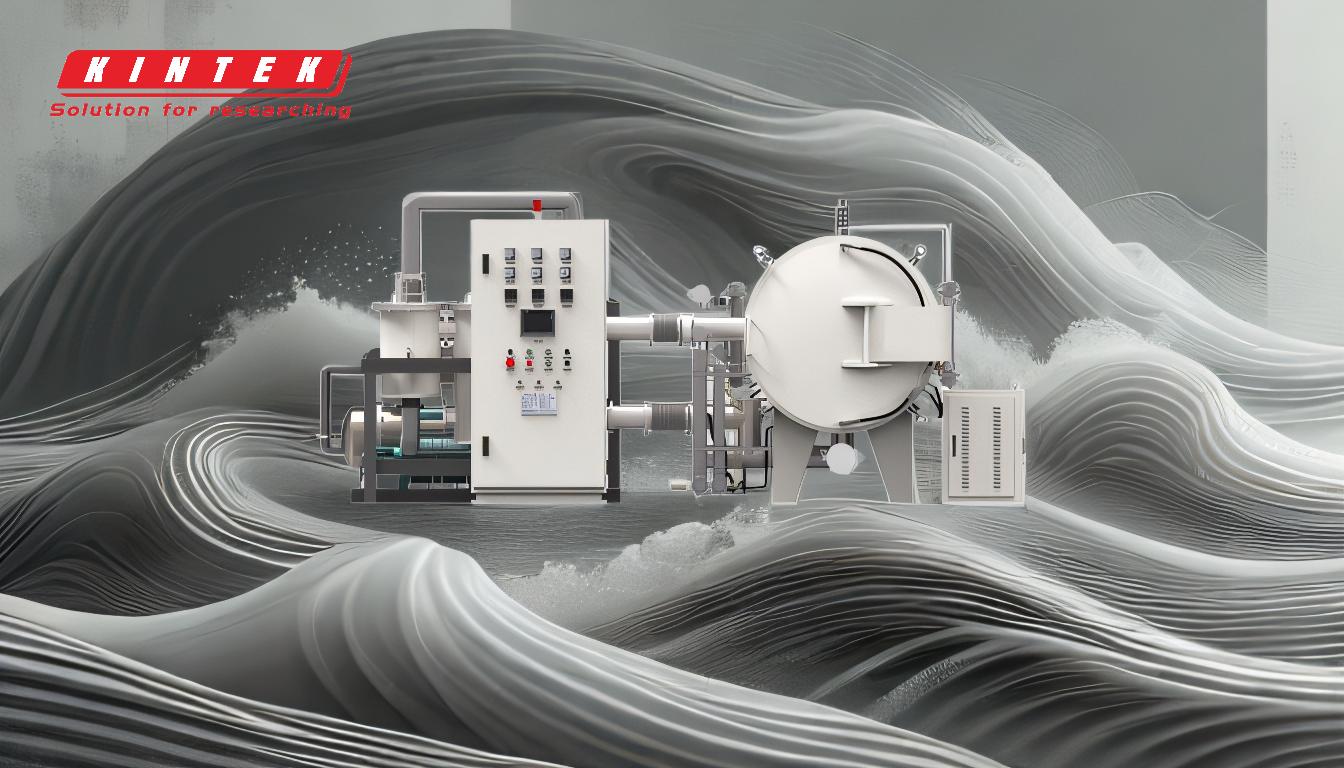
-
Definition of Film Uniformity:
- Film uniformity refers to the consistency of a thin film's thickness and other properties across the entire substrate.
- It ensures that the film's thickness is nearly identical at every location on the wafer or substrate.
-
Importance of Uniformity:
- Uniformity is critical for the performance and reliability of semiconductor devices.
- Variations in film thickness can lead to defects, reduced yield, and inconsistent device performance.
- It is also important in optical applications, where uniformity in properties like the index of refraction affects light transmission and reflection.
-
Factors Affecting Uniformity:
- Deposition Process: The method used to deposit the thin film (e.g., chemical vapor deposition, physical vapor deposition) can influence uniformity.
- Substrate Conditions: Surface roughness, temperature, and cleanliness of the substrate can affect how uniformly the film is deposited.
- Equipment Calibration: Proper calibration of deposition equipment is essential to achieve consistent film thickness.
- Process Parameters: Variables such as deposition rate, pressure, and gas flow rates must be carefully controlled.
-
Measurement of Uniformity:
- Uniformity is typically measured using techniques such as ellipsometry, profilometry, or optical interferometry.
- These methods provide detailed maps of film thickness across the substrate, allowing for precise evaluation of uniformity.
-
Applications and Specifications:
- Different applications have varying requirements for film uniformity. For example, semiconductor manufacturing often requires extremely high uniformity, while other applications may tolerate more variation.
- Over-specifying uniformity can increase manufacturing costs, while under-specifying can lead to product failures.
-
Challenges in Achieving Uniformity:
- Achieving high uniformity is particularly challenging for large substrates or complex geometries.
- Edge effects, where the film thickness varies near the edges of the substrate, are a common issue.
-
Strategies to Improve Uniformity:
- Optimizing deposition parameters and equipment design can enhance uniformity.
- Using advanced techniques like atomic layer deposition (ALD) can provide better control over film thickness.
- Regular maintenance and calibration of deposition equipment are essential to maintain uniformity over time.
By understanding and addressing these key points, manufacturers can ensure that their thin films meet the necessary uniformity requirements for their specific applications, ultimately improving product quality and performance.
Summary Table:
Aspect | Details |
---|---|
Definition | Consistency of a thin film's thickness and properties across a substrate. |
Importance | Critical for semiconductor performance, optical applications, and yield. |
Factors Affecting | Deposition process, substrate conditions, equipment calibration, parameters. |
Measurement | Ellipsometry, profilometry, optical interferometry. |
Applications | Semiconductor manufacturing, optical coatings, and more. |
Challenges | Edge effects, large substrates, complex geometries. |
Improvement Strategies | Optimize parameters, use ALD, maintain equipment calibration. |
Need help achieving optimal film uniformity? Contact our experts today for tailored solutions!