High-density plasma chemical vapor deposition (HDP-CVD) is an advanced variant of the CVD process that utilizes high-density plasma to enhance the deposition of thin films on substrates. This process is particularly effective for creating high-quality, uniform, and conformal coatings, especially in semiconductor manufacturing. The high-density plasma increases the ionization and dissociation of gaseous precursors, leading to more efficient reactions and better control over film properties. The process involves the introduction of gaseous precursors into a chamber, their activation via high-density plasma, surface reactions leading to deposition, and the removal of byproducts. HDP-CVD is known for its ability to deposit films at lower temperatures compared to traditional CVD, making it suitable for temperature-sensitive substrates.
Key Points Explained:
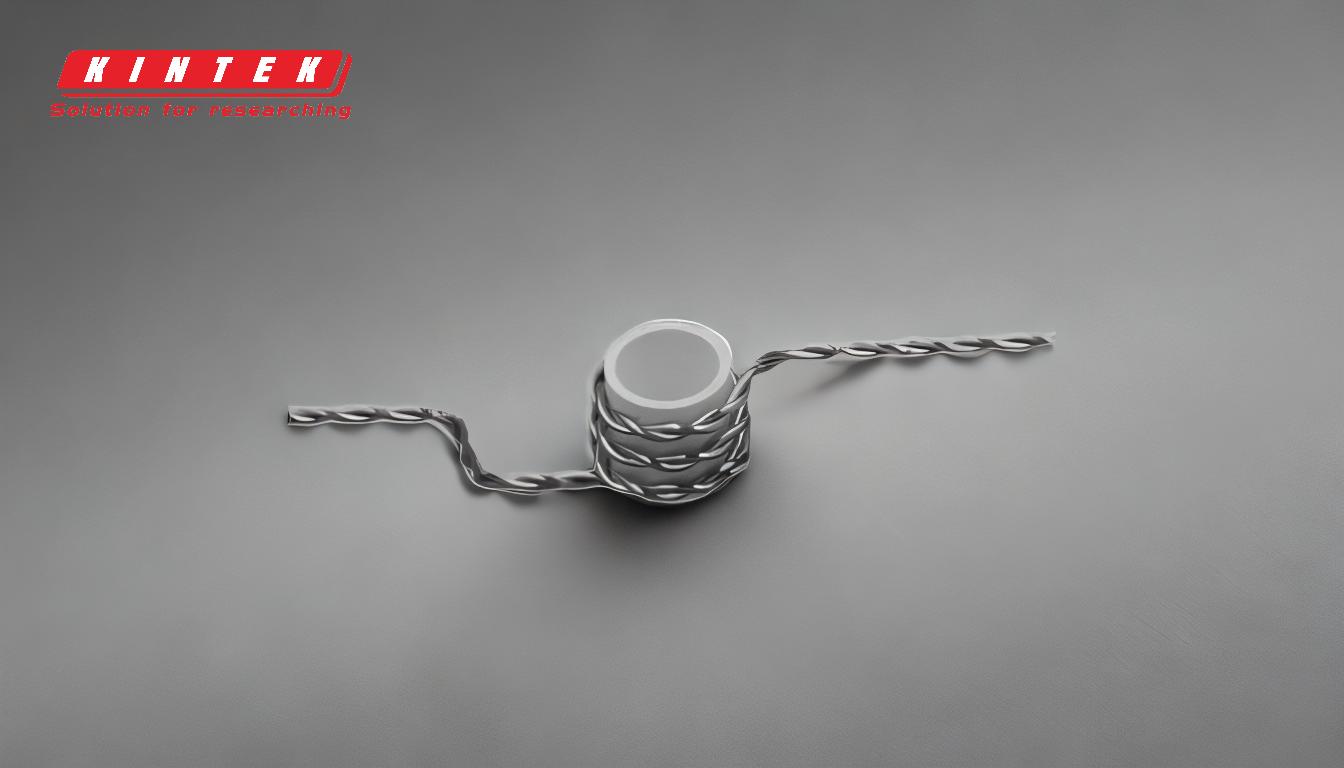
-
Introduction of Reactants:
- Gaseous precursors are introduced into a reaction chamber containing the substrate. These precursors are typically volatile compounds that can easily decompose or react under the right conditions.
- The choice of precursors depends on the desired material to be deposited, such as silicon dioxide, silicon nitride, or other compounds.
-
Activation of Reactants:
- In HDP-CVD, the activation of reactants is achieved through high-density plasma. This plasma is generated using methods such as inductively coupled plasma (ICP) or electron cyclotron resonance (ECR).
- The high-density plasma ionizes and dissociates the gaseous precursors, creating highly reactive species that are more likely to react on the substrate surface.
-
Surface Reaction and Deposition:
- The activated precursors react at the substrate surface, forming the desired material. The high-density plasma ensures that the reactions occur uniformly and conformally across the substrate.
- This step is crucial for achieving high-quality films with precise thickness and composition. The high-energy plasma also allows for deposition at lower temperatures, which is beneficial for temperature-sensitive substrates.
-
Removal of Byproducts:
- After the deposition, volatile or non-volatile byproducts are removed from the reaction chamber. This is typically done through gas flow, ensuring that the chamber is clean for the next deposition cycle.
- Efficient removal of byproducts is essential to prevent contamination and ensure the quality of the deposited film.
-
Advantages of HDP-CVD:
- Lower Temperature Deposition: HDP-CVD allows for deposition at lower temperatures compared to traditional CVD, making it suitable for temperature-sensitive substrates.
- High-Quality Films: The high-density plasma ensures uniform and conformal coatings, leading to high-quality films with precise thickness and composition.
- Enhanced Reactivity: The high-energy plasma increases the reactivity of the precursors, leading to more efficient reactions and better control over film properties.
-
Applications:
- HDP-CVD is widely used in the semiconductor industry for depositing dielectric layers, such as silicon dioxide and silicon nitride, in integrated circuits.
- It is also used in the fabrication of microelectromechanical systems (MEMS) and other advanced materials where precise and uniform coatings are required.
In summary, high-density plasma chemical vapor deposition (HDP-CVD) is a sophisticated technique that leverages high-density plasma to enhance the deposition of thin films. It offers several advantages over traditional CVD, including lower temperature deposition, high-quality films, and enhanced reactivity, making it a valuable process in advanced manufacturing and semiconductor industries.
Summary Table:
Key Aspect | Details |
---|---|
Process Overview | Uses high-density plasma to enhance thin film deposition on substrates. |
Key Steps | 1. Introduction of reactants 2. Activation via plasma 3. Surface reaction & deposition 4. Byproduct removal |
Advantages | - Lower temperature deposition - High-quality, uniform films - Enhanced reactivity |
Applications | Semiconductor manufacturing, MEMS fabrication, and advanced materials. |
Interested in learning more about HDP-CVD for your applications? Contact our experts today!