Mold maintenance refers to the systematic process of inspecting, cleaning, repairing, and optimizing molds used in manufacturing processes, particularly in injection molding. It ensures that molds remain in optimal condition, prolonging their lifespan, maintaining product quality, and minimizing downtime. Regular maintenance involves addressing wear and tear, preventing defects, and ensuring the molds operate efficiently. This process is critical for industries relying on precision molding, as it reduces production costs, avoids unexpected breakdowns, and ensures consistent output. Effective mold maintenance combines preventive measures, timely repairs, and thorough documentation to track the mold's performance and history.
Key Points Explained:
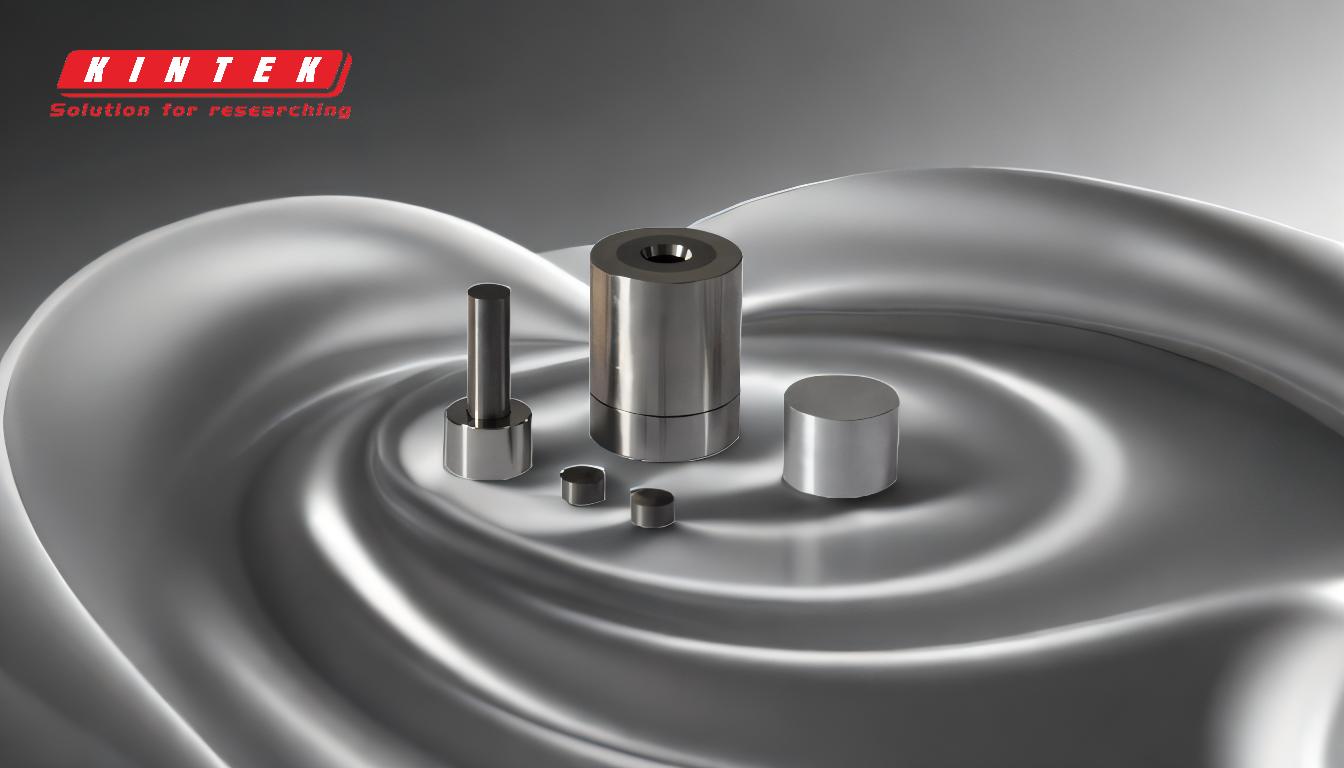
-
Definition and Purpose of Mold Maintenance:
- Mold maintenance involves a series of activities aimed at preserving the functionality and longevity of molds.
- Its primary purpose is to prevent defects in manufactured products, reduce downtime, and extend the mold's operational life.
- By maintaining molds, manufacturers can ensure consistent product quality and avoid costly replacements or repairs.
-
Key Components of Mold Maintenance:
- Inspection: Regular visual and functional inspections are conducted to identify signs of wear, damage, or misalignment. This includes checking for cracks, corrosion, or any abnormalities in the mold's surface or structure.
- Cleaning: Molds are cleaned to remove residues, such as plastic, grease, or debris, which can affect product quality. Cleaning methods may include ultrasonic cleaning, chemical cleaning, or manual scrubbing.
- Repair and Replacement: Damaged components, such as ejector pins, cooling channels, or cavities, are repaired or replaced to restore the mold's functionality.
- Lubrication: Proper lubrication of moving parts, such as slides and ejector systems, is essential to reduce friction and prevent wear.
- Documentation: Detailed records of maintenance activities, including inspection results, repairs, and cleaning schedules, are maintained to track the mold's history and performance.
-
Types of Mold Maintenance:
- Preventive Maintenance: Scheduled maintenance activities performed to prevent potential issues before they occur. This includes regular inspections, cleaning, and lubrication.
- Corrective Maintenance: Repairs and adjustments made in response to identified issues, such as defects or malfunctions.
- Predictive Maintenance: Advanced techniques, such as monitoring mold performance using sensors or data analytics, to predict and address potential problems before they escalate.
-
Benefits of Mold Maintenance:
- Extended Mold Lifespan: Regular maintenance reduces wear and tear, ensuring molds last longer and perform efficiently.
- Improved Product Quality: Well-maintained molds produce consistent, high-quality products with fewer defects.
- Cost Savings: Preventive maintenance reduces the need for expensive repairs or replacements and minimizes production downtime.
- Enhanced Efficiency: Properly maintained molds operate smoothly, reducing cycle times and improving overall productivity.
-
Challenges in Mold Maintenance:
- Complexity: Molds can have intricate designs, making maintenance tasks time-consuming and requiring specialized skills.
- Downtime: Maintenance activities may require halting production, which can impact schedules and output.
- Cost: While maintenance saves money in the long run, it requires an initial investment in tools, equipment, and skilled personnel.
-
Best Practices for Effective Mold Maintenance:
- Develop a Maintenance Schedule: Create a detailed plan outlining inspection, cleaning, and repair tasks at regular intervals.
- Train Personnel: Ensure maintenance staff are well-trained in mold inspection, cleaning, and repair techniques.
- Use High-Quality Tools and Materials: Invest in durable cleaning agents, lubricants, and replacement parts to ensure effective maintenance.
- Monitor Mold Performance: Implement systems to track mold performance and identify trends or issues early.
- Collaborate with Mold Designers: Work closely with mold designers to understand the mold's specifications and maintenance requirements.
By following these practices, manufacturers can optimize their mold maintenance processes, ensuring reliable production and high-quality outputs.
Summary Table:
Aspect | Details |
---|---|
Definition | Systematic process of inspecting, cleaning, repairing, and optimizing molds. |
Purpose | Prevent defects, reduce downtime, and extend mold lifespan. |
Key Components | Inspection, cleaning, repair, lubrication, and documentation. |
Types | Preventive, corrective, and predictive maintenance. |
Benefits | Extended lifespan, improved quality, cost savings, and enhanced efficiency. |
Challenges | Complexity, downtime, and initial cost. |
Best Practices | Maintenance schedule, trained personnel, quality tools, and performance monitoring. |
Optimize your mold maintenance process—contact us today for expert guidance!