Sintered iron is a material created through the sintering process, which involves compacting and heating iron powder particles below their melting point to form a solid structure. This method is particularly useful for metals with high melting points, as it avoids the need to reach those extreme temperatures. Sintering enhances the material's properties by reducing porosity and improving strength, making it suitable for various industrial applications, including 3D printing and filtration systems. The process allows for precise control over the material's characteristics, resulting in consistent and high-quality products.
Key Points Explained:
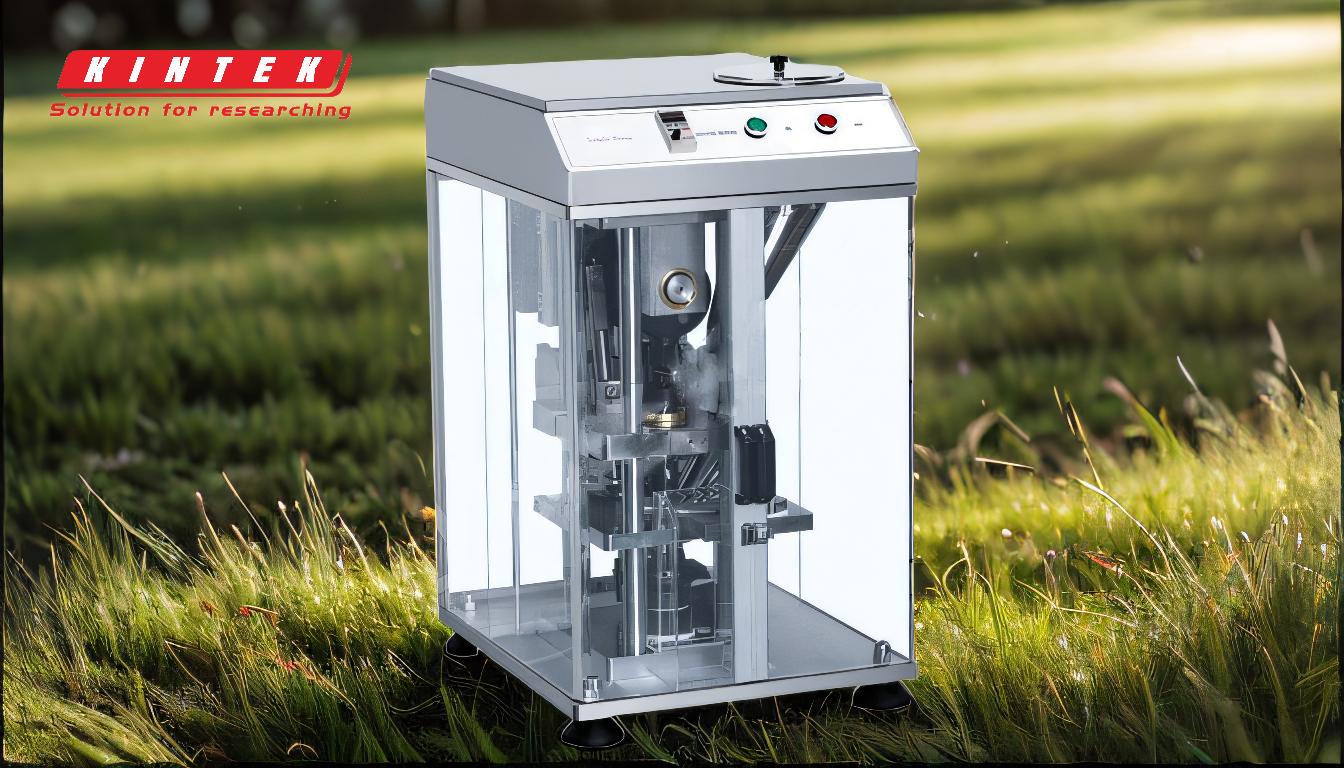
-
Definition of Sintered Iron:
- Sintered iron is produced by compacting iron powder and heating it below its melting point. This process bonds the particles together, forming a solid structure without liquefying the metal. The result is a material with improved mechanical properties and reduced porosity.
-
Sintering Process:
- The sintering process involves several steps:
- Compaction: Iron powder is pressed into a desired shape using high pressure.
- Heating: The compacted powder is heated in a controlled environment, typically in a furnace, at temperatures below the melting point of iron.
- Bonding: The heat causes the particles to bond at their contact points, creating a cohesive structure.
- This method is energy-efficient and allows for precise control over the material's properties.
- The sintering process involves several steps:
-
Advantages of Sintered Iron:
- Improved Properties: Sintering reduces the porosity of the material, enhancing its strength, durability, and wear resistance.
- Energy Efficiency: Since sintering occurs below the melting point, it consumes less energy compared to traditional melting processes.
- Customization: The process allows for the creation of complex shapes and custom forms, making it ideal for applications like 3D printing.
- Consistency: Sintering provides uniform properties throughout the material, ensuring high-quality and reliable products.
-
Applications of Sintered Iron:
- 3D Printing: Sintered iron is used in additive manufacturing to create custom metal parts with intricate designs. The process offers greater control over the final product's shape and properties.
- Filtration Systems: Sintered iron is utilized in filters, such as pe filters, due to its porous structure and ability to trap contaminants.
- Industrial Components: The material is commonly used in the production of gears, bearings, and other mechanical parts that require high strength and durability.
-
Comparison with Other Materials:
- Sintered iron offers several advantages over traditional cast iron or wrought iron:
- Lower Production Costs: The sintering process is more cost-effective for producing complex shapes.
- Enhanced Performance: The reduced porosity and improved bonding result in better mechanical properties.
- Versatility: Sintered iron can be tailored to meet specific requirements, making it suitable for a wide range of applications.
- Sintered iron offers several advantages over traditional cast iron or wrought iron:
In summary, sintered iron is a versatile and high-performance material produced through the sintering process. Its unique properties make it an excellent choice for various industrial applications, offering advantages in terms of energy efficiency, customization, and consistency.
Summary Table:
Aspect | Details |
---|---|
Definition | Iron powder compacted and heated below melting point to form solid structures. |
Process Steps | Compaction → Heating → Bonding |
Advantages | Improved strength, energy efficiency, customization, and consistency. |
Applications | 3D printing, filtration systems, gears, bearings, and industrial components. |
Comparison | Lower costs, enhanced performance, and versatility vs. traditional iron. |
Interested in using sintered iron for your industrial needs? Contact us today to learn more!