Sputtering is a physical process used in chemistry and materials science to deposit thin films onto substrates. It involves bombarding a solid target material with high-energy particles (typically ions of an inert gas like argon) in a vacuum environment. The collision of these ions with the target causes atoms or molecules from the target to be ejected and deposited onto a nearby substrate, forming a thin, uniform film. This process is widely used in industries such as semiconductor manufacturing, optics, and surface finishing due to its ability to produce high-quality coatings with excellent adhesion, density, and uniformity.
Key Points Explained:
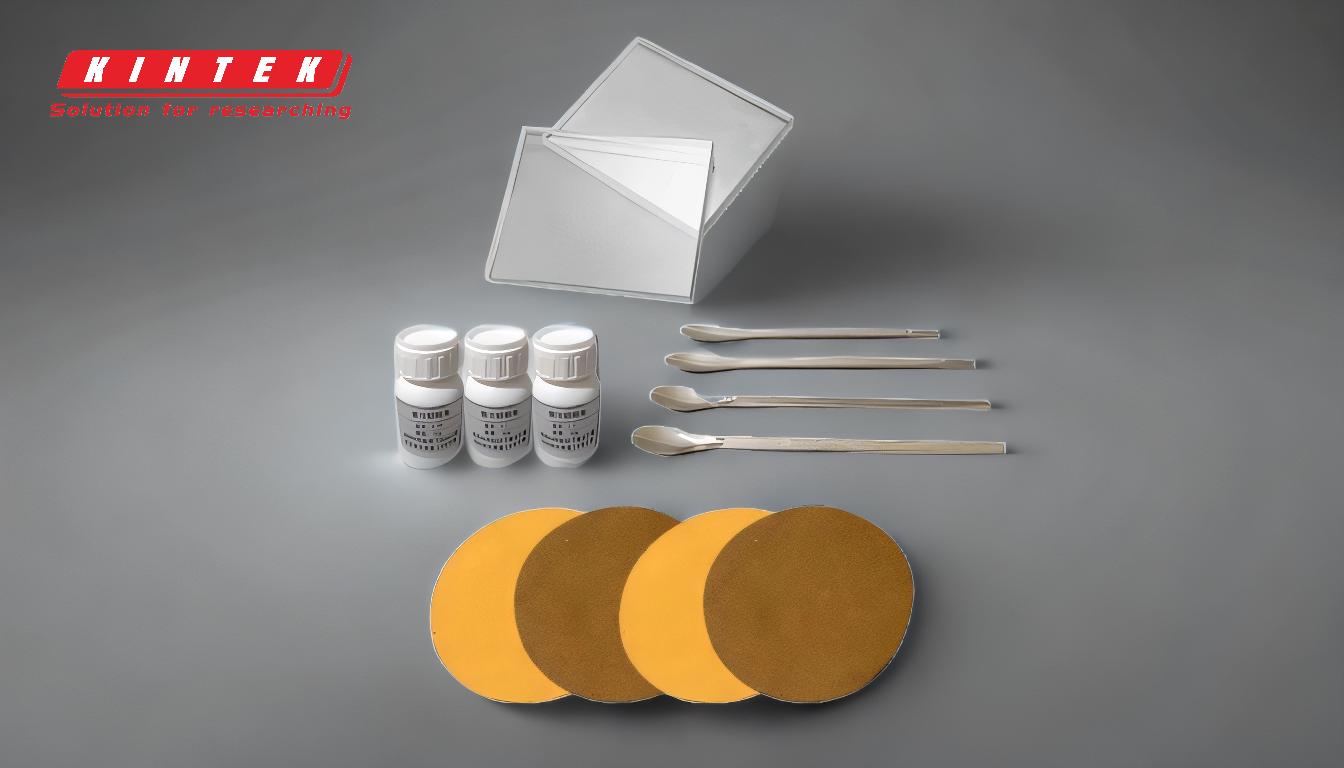
-
Definition of Sputtering:
- Sputtering is a process where particles (ions or neutral atoms/molecules) bombard the surface of a solid target, causing atoms or molecules near the surface to gain enough energy to escape.
- This phenomenon occurs under vacuum conditions, making it a form of vacuum sputtering.
-
Mechanism of Sputtering:
- High-energy particles (usually ions of an inert gas like argon) are accelerated toward a target material.
- Upon collision, energy is transferred to the target atoms, causing them to be ejected from the surface.
- The ejected atoms or molecules travel in a straight line and deposit onto a substrate, forming a thin film.
-
Types of Sputtering:
- Physical Sputtering: The most common type, where momentum transfer from incident ions causes target atoms to be ejected.
- Other types include reactive sputtering, magnetron sputtering, and ion beam sputtering, each with specific applications and advantages.
-
Equipment and Process:
- A vacuum chamber is essential to maintain the low-pressure environment required for sputtering.
- The chamber contains a target material (cathode) and a substrate to be coated.
- An inert gas (e.g., argon) is introduced into the chamber, and a high voltage is applied to ionize the gas.
- The positively charged ions are accelerated toward the negatively charged target, causing sputtering.
-
Applications of Sputtering:
- Semiconductor Industry: Used for depositing thin films in integrated circuits and microelectronics.
- Optics: Produces anti-reflective coatings, mirrors, and optical filters.
- Surface Finishing: Enhances the durability and appearance of materials.
- Space Technology: Naturally occurring sputtering in space affects spacecraft materials, but controlled sputtering is used for protective coatings.
-
Advantages of Sputtering:
- Uniformity: Produces highly uniform thin films.
- Adhesion: Ensures strong adhesion between the film and substrate.
- Versatility: Can deposit a wide range of materials, including metals, alloys, and ceramics.
- Precision: Allows for precise control over film thickness and composition.
-
Challenges and Considerations:
- Vacuum Requirements: Requires specialized equipment to maintain a vacuum, increasing operational costs.
- Energy Consumption: High-energy processes can be energy-intensive.
- Target Erosion: The target material erodes over time, requiring periodic replacement.
-
Comparison with Other Thin Film Deposition Methods:
- Sputtering is a type of Physical Vapor Deposition (PVD), which also includes methods like evaporation.
- Compared to evaporation, sputtering offers better adhesion and uniformity, especially for complex materials.
By understanding these key points, one can appreciate the importance of sputtering in modern technology and its role in advancing industries that rely on high-quality thin films.
Summary Table:
Aspect | Details |
---|---|
Definition | A process where high-energy particles eject atoms from a target to form thin films. |
Mechanism | Ions (e.g., argon) collide with a target, ejecting atoms onto a substrate. |
Types | Physical, reactive, magnetron, and ion beam sputtering. |
Applications | Semiconductors, optics, surface finishing, and space technology. |
Advantages | Uniformity, strong adhesion, versatility, and precision. |
Challenges | Vacuum requirements, energy consumption, and target erosion. |
Ready to explore sputtering solutions for your industry? Contact us today to learn more!