PVD (Physical Vapor Deposition) and CVD (Chemical Vapor Deposition) are advanced coating technologies with distinct applications across various industries. PVD is widely used in decorative and functional coatings for jewelry, hardware, and consumer goods, offering durability and aesthetic appeal. CVD, on the other hand, is favored in industrial applications such as machine tools, medical devices, and automotive components, as well as in producing high-performance materials like artificial diamonds. Both techniques are critical in semiconductor manufacturing, where they enable the precise deposition of thin layers for electronic devices. Their differences in process, material compatibility, and environmental impact make them suitable for specific use cases.
Key Points Explained:
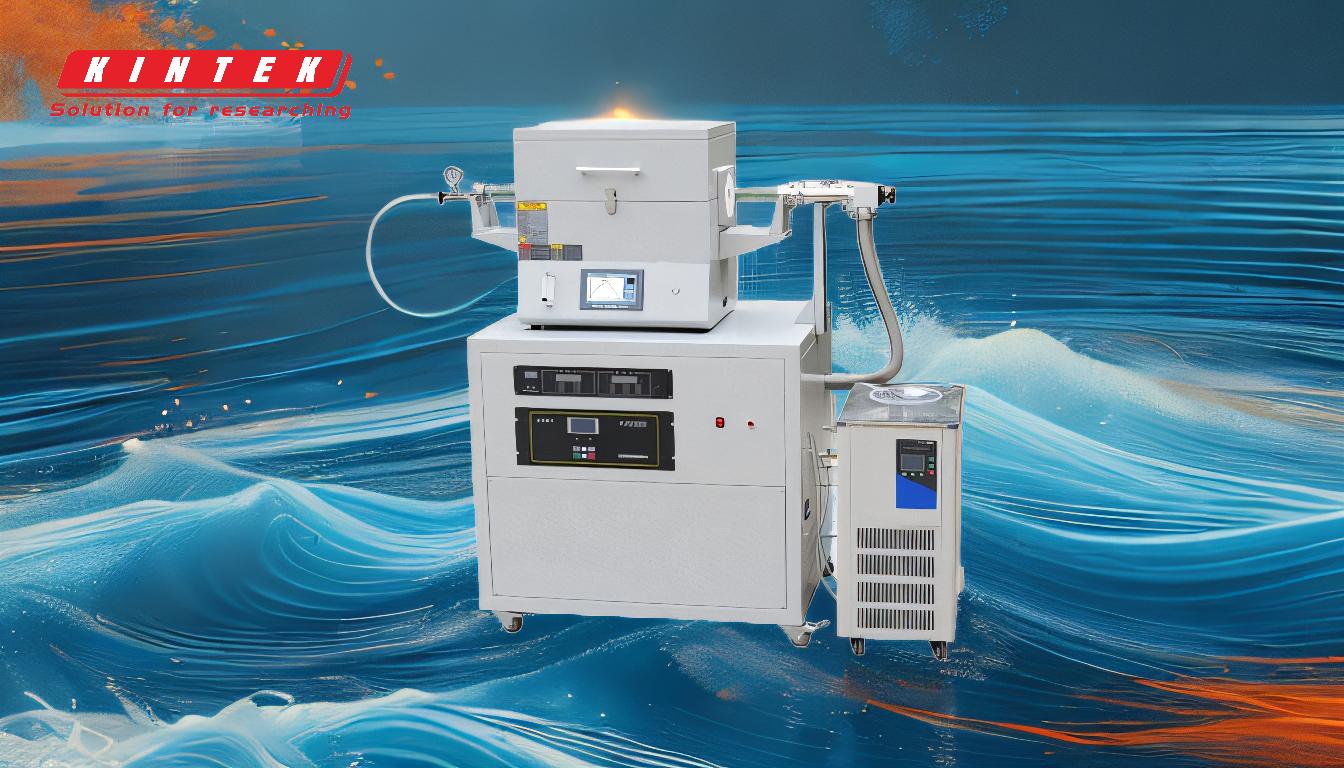
-
Applications of PVD:
- Decorative and Functional Coatings: PVD is extensively used in industries like jewelry, door and window hardware, kitchen and bathroom fixtures, lamps, marine supplies, and handicrafts. Its ability to create thin, smooth, and durable coatings makes it ideal for enhancing both aesthetics and functionality.
- Durability and Temperature Resistance: PVD coatings are known for their durability and ability to withstand high temperatures, making them suitable for applications requiring long-lasting performance.
- Environmental Friendliness: PVD is an environmentally friendly process as it does not involve chemical reactions that produce harmful byproducts.
-
Applications of CVD:
- Industrial and High-Performance Coatings: CVD is primarily used in industrial applications such as machine tools, medical instruments, and automotive components. Its ability to deposit thicker and rougher coatings makes it suitable for high-stress environments.
- Artificial Diamond Production: CVD is a key technology in producing artificial diamonds, which are used in cutting tools, abrasives, and high-performance electronics.
- Semiconductor Manufacturing: CVD is critical in the semiconductor industry for depositing thin layers of n-type and p-type materials, enabling the creation of structural junctions in electronic devices.
-
Comparison of PVD and CVD:
- Process Differences: PVD uses physical methods to deposit coatings, involving the transformation of a substance's states without chemical reactions. In contrast, CVD relies on chemical reactions to deposit layers, which can result in the production of new substances.
- Material Compatibility: PVD is limited to solid coating materials, while CVD can use gaseous precursors, allowing it to be applied to a wider range of materials.
- Temperature Requirements: PVD operates at relatively low temperatures (250°C~450°C), whereas CVD requires higher temperatures (450°C to 1050°C), making it less suitable for temperature-sensitive substrates.
-
Environmental Impact:
- PVD: As a physical process, PVD is more environmentally friendly, as it does not produce harmful byproducts or consume old materials.
- CVD: The chemical reactions involved in CVD can result in pollution, making it less favorable in environmentally conscious applications.
-
Semiconductor Industry:
- Both PVD and CVD are indispensable in the semiconductor industry for creating thin layers of materials required for electronic devices. PVD is often used for metal deposition, while CVD is preferred for depositing dielectric and semiconductor layers.
By understanding the distinct applications and characteristics of PVD and CVD, manufacturers and purchasers can make informed decisions about which technology best suits their specific needs.
Summary Table:
Aspect | PVD | CVD |
---|---|---|
Applications | Decorative and functional coatings (jewelry, hardware, consumer goods) | Industrial coatings (machine tools, medical devices, automotive) |
Process | Physical vapor deposition (no chemical reactions) | Chemical vapor deposition (involves chemical reactions) |
Material Compatibility | Limited to solid materials | Can use gaseous precursors, wider material range |
Temperature Range | 250°C~450°C | 450°C~1050°C |
Environmental Impact | Environmentally friendly (no harmful byproducts) | Can produce pollution due to chemical reactions |
Semiconductor Use | Metal deposition | Dielectric and semiconductor layer deposition |
Need help choosing between PVD and CVD for your project? Contact our experts today for personalized advice!