Reactive sputtering is a specialized thin-film deposition technique where a reactive gas (e.g., oxygen or nitrogen) is introduced into the sputtering chamber to chemically react with the target material, forming compounds like oxides or nitrides. This process is widely used in industries such as aerospace, automotive, medical, and semiconductors for applications like optical coatings, barrier layers, and thin-film resistors. It allows precise control over film composition and properties, making it essential for producing high-performance materials like aluminum oxide (Al2O3) and titanium nitride (TiN). Reactive sputtering is particularly valuable for creating functional coatings with tailored electrical, thermal, and mechanical properties.
Key Points Explained:
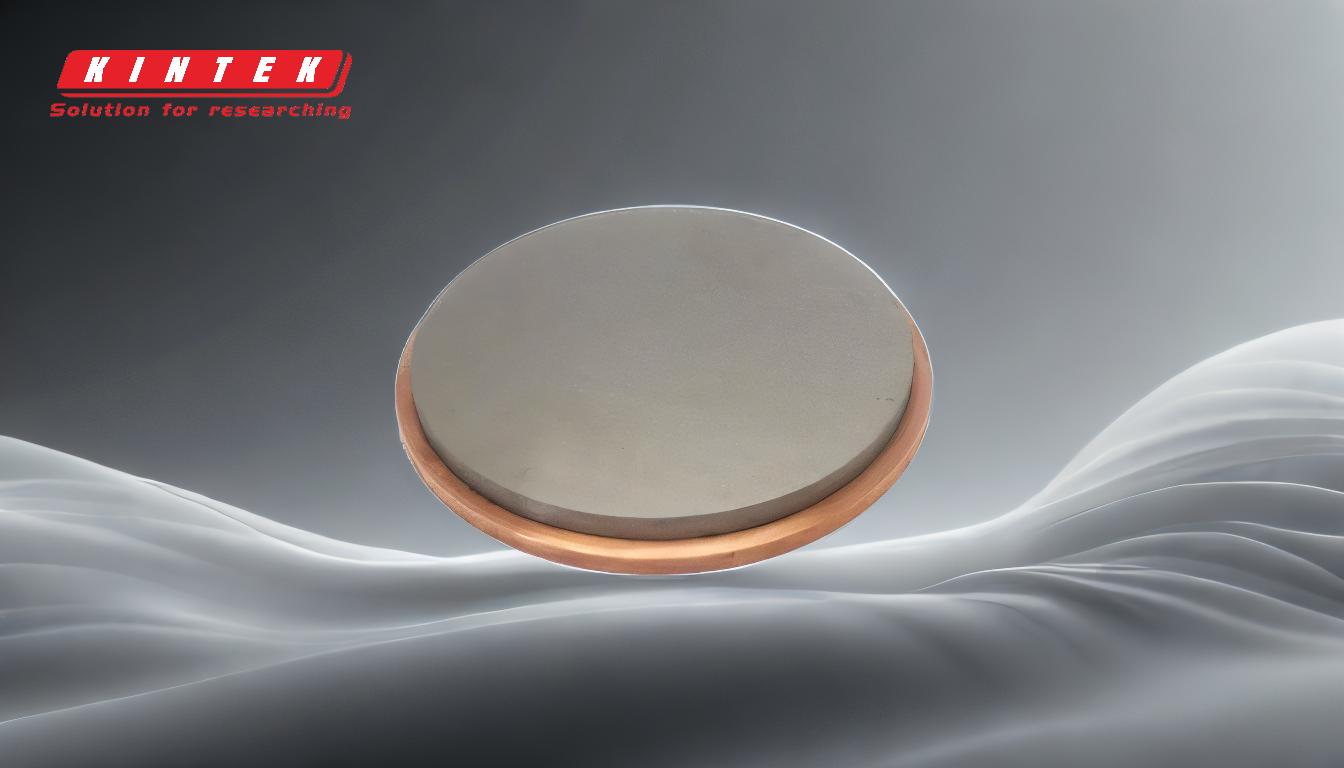
-
Fundamentals of Reactive Sputtering:
- Reactive sputtering is a variation of the plasma sputtering process.
- It involves introducing a reactive gas (e.g., oxygen, nitrogen) into the sputtering chamber alongside an inert gas like argon.
- The reactive gas chemically bonds with the target material (e.g., aluminum, titanium) to form compounds (e.g., oxides, nitrides) that are deposited as thin films on a substrate.
-
Key Applications:
- Optical Coatings: Used in the production of high-efficiency windows, optical lenses, and anti-reflective coatings.
- Semiconductors and Electronics: Deposits thin films for semiconductors, resistors, and dielectrics, such as tantalum nitride (TaN) for thin-film resistors.
- Barrier Layers: Creates protective coatings like titanium nitride (TiN) for wear resistance and corrosion protection.
- Decorative and Functional Coatings: Used in hardware and consumer goods for both aesthetic and functional purposes.
-
Advantages of Reactive Sputtering:
- Precise Control: Allows for the creation of films with specific stoichiometry and structure, enabling tailored properties like electrical conductivity, thermal conductivity, and mechanical strength.
- Versatility: Can deposit a wide range of materials, including oxides, nitrides, and carbides, for diverse applications.
- High-Quality Films: Produces uniform, dense, and adherent coatings with excellent performance characteristics.
-
Industries Utilizing Reactive Sputtering:
- Aerospace and Defense: For durable, high-performance coatings on critical components.
- Automotive: Enhances the durability and functionality of engine parts and decorative elements.
- Medical: Used in biocompatible coatings for implants and medical devices.
- Energy and Lighting: Improves the efficiency of solar panels and LED components.
- Consumer Goods: Provides functional and decorative coatings for everyday items.
-
Examples of Reactive Sputtering in Action:
- Aluminum Oxide (Al2O3): Formed by reacting aluminum with oxygen, used for its hardness and insulating properties.
- Titanium Nitride (TiN): Created by reacting titanium with nitrogen, known for its wear resistance and golden appearance.
- Tantalum Nitride (TaN): Used in thin-film resistors for its stability and precise electrical properties.
-
Process Considerations:
- Gas Selection: The choice of reactive gas (e.g., oxygen, nitrogen, acetylene) depends on the desired film composition.
- Target Material: The target material must be compatible with the reactive gas to form the desired compound.
- Control Parameters: Factors like gas flow rate, pressure, and power must be carefully controlled to achieve the desired film properties.
-
Future Trends:
- Nanotechnology: Reactive sputtering is increasingly used to modify the properties of metallic nanofilms for advanced applications.
- Sustainability: Development of eco-friendly reactive gases and processes to reduce environmental impact.
- Automation: Integration of advanced control systems for higher precision and efficiency in film deposition.
By leveraging reactive sputtering, industries can produce high-quality, functional coatings with tailored properties, making it a cornerstone of modern materials engineering.
Summary Table:
Aspect | Details |
---|---|
Process | Reactive gas (e.g., oxygen, nitrogen) reacts with target material to form compounds like oxides or nitrides. |
Applications | Optical coatings, semiconductors, barrier layers, decorative coatings. |
Advantages | Precise control, versatility, high-quality films. |
Industries | Aerospace, automotive, medical, energy, consumer goods. |
Examples | Aluminum oxide (Al2O3), titanium nitride (TiN), tantalum nitride (TaN). |
Future Trends | Nanotechnology, sustainability, automation. |
Unlock the potential of reactive sputtering for your industry—contact us today to learn more!