Silicon Carbide (SiC) is a versatile material with significant applications in the energy sector due to its exceptional thermal, mechanical, and electrical properties. Historically known for its use as an abrasive material, SiC has evolved into a critical component in modern energy technologies. Its applications span from industrial heating elements and semiconductor substrates to advanced turbine components and protective coatings in nuclear energy. The material's ability to withstand extreme temperatures, resist wear, and conduct electricity efficiently makes it indispensable in energy generation, storage, and conversion systems. Below, we explore the key applications of SiC in the energy sector, highlighting its role in enhancing efficiency, durability, and performance across various energy-related technologies.
Key Points Explained:
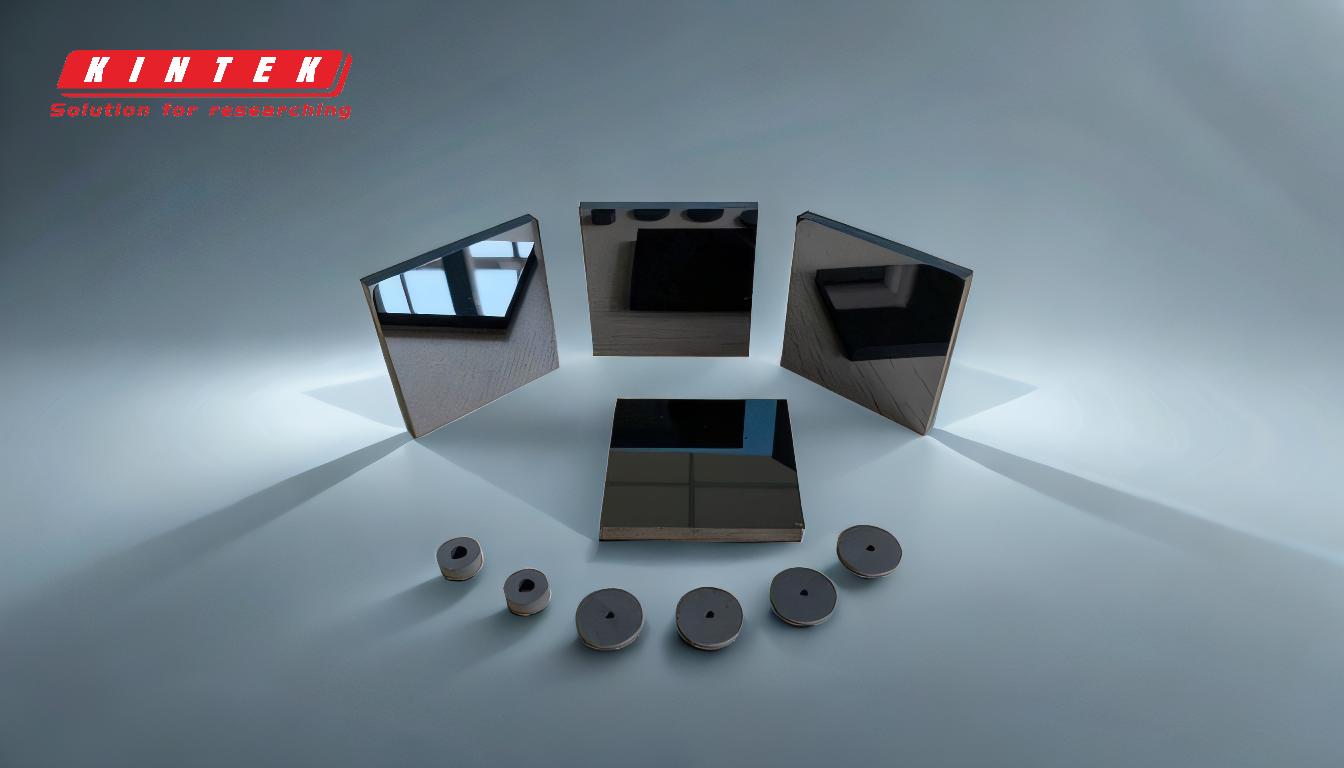
-
Resistance Heating Elements in Electric Furnaces:
- SiC is widely used in electric furnaces as resistance heating elements due to its high thermal conductivity and ability to withstand extreme temperatures (up to 1600°C).
- Its electrical conductivity can be tailored, making it ideal for thermistors (temperature-sensitive resistors) and varistors (voltage-sensitive resistors), which are critical in temperature and voltage regulation in energy systems.
- Applications include industrial heating processes, such as metal smelting and ceramic sintering, where energy efficiency and durability are paramount.
-
Semiconductor Substrates for Power Electronics:
- SiC is a key material in the production of semiconductor substrates, particularly for power electronics used in energy conversion systems.
- Its wide bandgap (3.26 eV) allows for higher voltage tolerance, faster switching speeds, and lower energy losses compared to traditional silicon-based semiconductors.
- This makes SiC essential in renewable energy systems, such as solar inverters and wind turbine converters, where efficient energy conversion is critical.
-
Turbine Components and Heat Exchangers:
- SiC is used in fixed and moving turbine components, such as seals, bearings, and hot gas flow liners, due to its exceptional wear resistance and thermal stability.
- In heat exchangers, SiC's high thermal conductivity and corrosion resistance improve energy transfer efficiency in high-temperature environments, such as in nuclear reactors and industrial processes.
-
Protective Coatings in Nuclear Energy:
- SiC-based materials are used as protective coatings for nuclear fuel particles, providing a barrier against radiation and high temperatures.
- This enhances the safety and longevity of nuclear reactors, contributing to the efficient and sustainable generation of nuclear energy.
-
Industrial Furnaces and Sintering Applications:
- In the ceramic and metallurgy industries, SiC is used for receiving capsules and muffles in sintering processes, where it ensures uniform heat distribution and energy efficiency.
- Its durability and thermal properties make it ideal for high-temperature industrial furnaces, reducing energy consumption and maintenance costs.
-
Light-Emitting Diodes (LEDs) and Energy-Efficient Lighting:
- SiC substrates are used in the production of LEDs, which are highly energy-efficient lighting solutions.
- The material's ability to handle high power densities and thermal loads makes it suitable for advanced LED applications, contributing to energy savings in lighting systems.
-
Rocket Engines and High-Performance Applications:
- SiC is used in rocket engine components due to its ability to withstand extreme temperatures and mechanical stress.
- This ensures reliable performance in energy-intensive aerospace applications, where efficiency and durability are critical.
-
Energy Storage and Conversion Systems:
- SiC is increasingly being integrated into energy storage systems, such as batteries and supercapacitors, due to its high electrical conductivity and thermal stability.
- In electric vehicles (EVs), SiC-based power electronics improve charging efficiency and extend battery life, supporting the transition to sustainable transportation.
By leveraging the unique properties of SiC, the energy sector can achieve significant advancements in efficiency, reliability, and sustainability. Its applications in heating, power electronics, turbines, nuclear energy, and lighting underscore its importance as a material that drives innovation in energy technologies.
Summary Table:
Application | Key Benefits |
---|---|
Resistance Heating Elements | High thermal conductivity, withstands extreme temperatures (up to 1600°C). |
Semiconductor Substrates | Wide bandgap for higher voltage tolerance, faster switching, lower energy loss. |
Turbine Components & Heat Exchangers | Exceptional wear resistance, thermal stability, and corrosion resistance. |
Protective Coatings in Nuclear Energy | Enhances safety and longevity of nuclear reactors. |
Industrial Furnaces & Sintering | Ensures uniform heat distribution, reduces energy consumption. |
LEDs & Energy-Efficient Lighting | Handles high power densities, contributes to energy savings. |
Rocket Engines | Withstands extreme temperatures and mechanical stress. |
Energy Storage & Conversion Systems | Improves charging efficiency and extends battery life in EVs. |
Unlock the potential of Silicon Carbide for your energy applications—contact our experts today!