A ball mill operates based on the principles of Impact and Attrition. It consists of a rotating cylinder filled with grinding media, such as steel balls or rods. As the cylinder rotates, the grinding media are tossed around, colliding with the material to be ground. This process reduces the material's size through repeated impacts and frictional forces. Ball mills can operate horizontally or vertically, and their efficiency depends on achieving the critical speed, where the grinding media rotate along the inner walls of the cylinder. Planetary ball mills, a specialized type, use centrifugal and Coriolis forces to enhance grinding efficiency by rotating jars in opposite directions.
Key Points Explained:
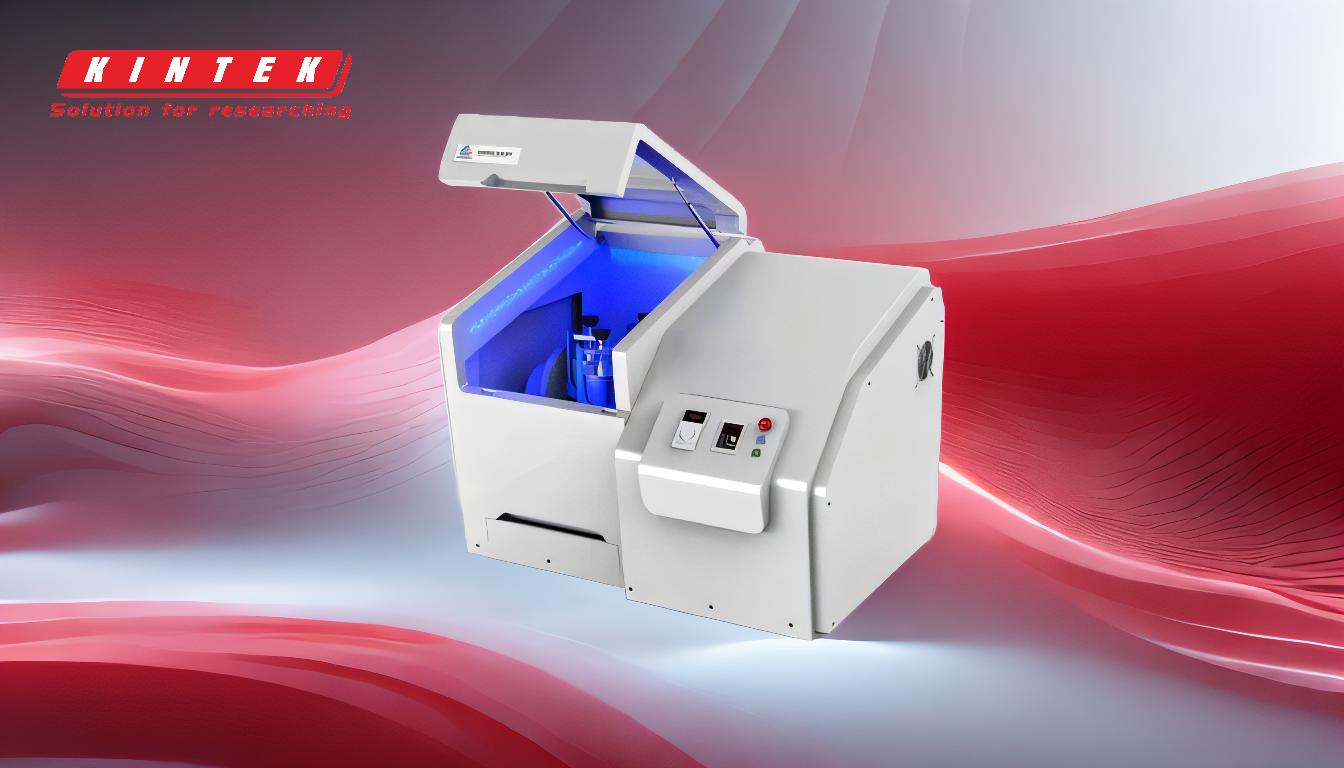
-
Principle of Operation: Impact and Attrition
- Impact: This refers to the force exerted when heavy grinding media (balls or rods) collide with the material. The pressure from these collisions breaks down the material into smaller particles.
- Attrition: This involves the reduction of material size through repeated collisions and friction between the grinding media and the material. It is a gradual process that results in fine particles.
-
Mechanism of a Ball Mill
- The ball mill consists of a horizontally or vertically mounted rotating cylinder.
- Grinding media (steel balls, rods, or ceramic balls) are placed inside the cylinder.
- As the cylinder rotates, the grinding media are lifted to a certain height and then fall, creating impact forces that grind the material.
- The rotation speed is critical. If the speed is too low, the balls will not achieve the necessary height to create effective impact. If the speed is too high, the balls will stick to the walls due to centrifugal force, reducing grinding efficiency.
-
Critical Speed
- Critical speed is the rotational speed at which the grinding media begin to rotate along the inner walls of the cylinder.
- Achieving critical speed ensures that the grinding media cascade and impact the material effectively.
- If the mill operates below critical speed, the grinding media will not generate enough force to grind the material efficiently.
-
Types of Ball Mills
- Horizontal Ball Mills: These are the most common type, with a horizontally mounted cylinder. They are suitable for coarse and fine grinding.
- Vertical Ball Mills: These have a vertically mounted cylinder and are often used for finer grinding or when space is limited.
- Planetary Ball Mills: These are high-energy mills where grinding jars rotate on their own axis while orbiting around a central point. This dual rotation creates strong centrifugal and Coriolis forces, enhancing grinding efficiency.
-
Planetary Ball Mills
- Planetary ball mills use multiple grinding jars, each mounted on a rotating platform (sun wheel).
- As the sun wheel rotates, each jar rotates in the opposite direction, creating a high-energy grinding environment.
- The centrifugal and Coriolis forces generated by this motion accelerate the grinding balls, resulting in faster and more efficient grinding.
-
Applications of Ball Mills
- Ball mills are widely used in industries such as mining, ceramics, pharmaceuticals, and material science.
- They are used for grinding ores, chemicals, and other materials into fine powders.
- Planetary ball mills are particularly useful for laboratory-scale grinding and nanomaterial synthesis due to their high efficiency.
-
Advantages and Limitations
-
Advantages:
- Versatile and capable of grinding a wide range of materials.
- Can produce fine and ultrafine powders.
- Planetary ball mills offer high energy efficiency and rapid grinding.
-
Limitations:
- High energy consumption, especially for large-scale operations.
- Wear and tear of grinding media and mill liners can be significant.
- Noise and vibration can be issues in some setups.
-
Advantages:
By understanding these principles and mechanisms, equipment and consumable purchasers can make informed decisions about the type of ball mill best suited for their specific needs, ensuring optimal performance and cost-effectiveness.
Summary Table:
Aspect | Details |
---|---|
Principles | Impact and attrition for material size reduction. |
Mechanism | Rotating cylinder with grinding media (balls/rods) for grinding. |
Critical Speed | Optimal rotation speed for effective grinding. |
Types | Horizontal, Vertical, and Planetary Ball Mills. |
Applications | Mining, ceramics, pharmaceuticals, material science, and nanomaterial synthesis. |
Advantages | Versatile, produces fine powders, high efficiency (especially planetary mills). |
Limitations | High energy consumption, wear and tear, noise, and vibration. |
Need help selecting the right ball mill for your application? Contact our experts today for personalized advice!