Diamond-like carbon (DLC) coatings are primarily composed of carbon, with a unique structure that combines both sp3 (diamond-like) and sp2 (graphite-like) carbon bonds. The base material is essentially an amorphous form of carbon, often hydrogenated, which gives it its distinctive properties. The sp3 bonds contribute to the hardness and durability similar to diamond, while the sp2 bonds provide some flexibility and lubrication, similar to graphite. This combination results in a material with high hardness, low friction, and excellent wear and chemical resistance. DLC coatings are widely used in industries such as automotive and machinery for components like bearings, camshafts, and power trains, where energy efficiency and durability are critical.
Key Points Explained:
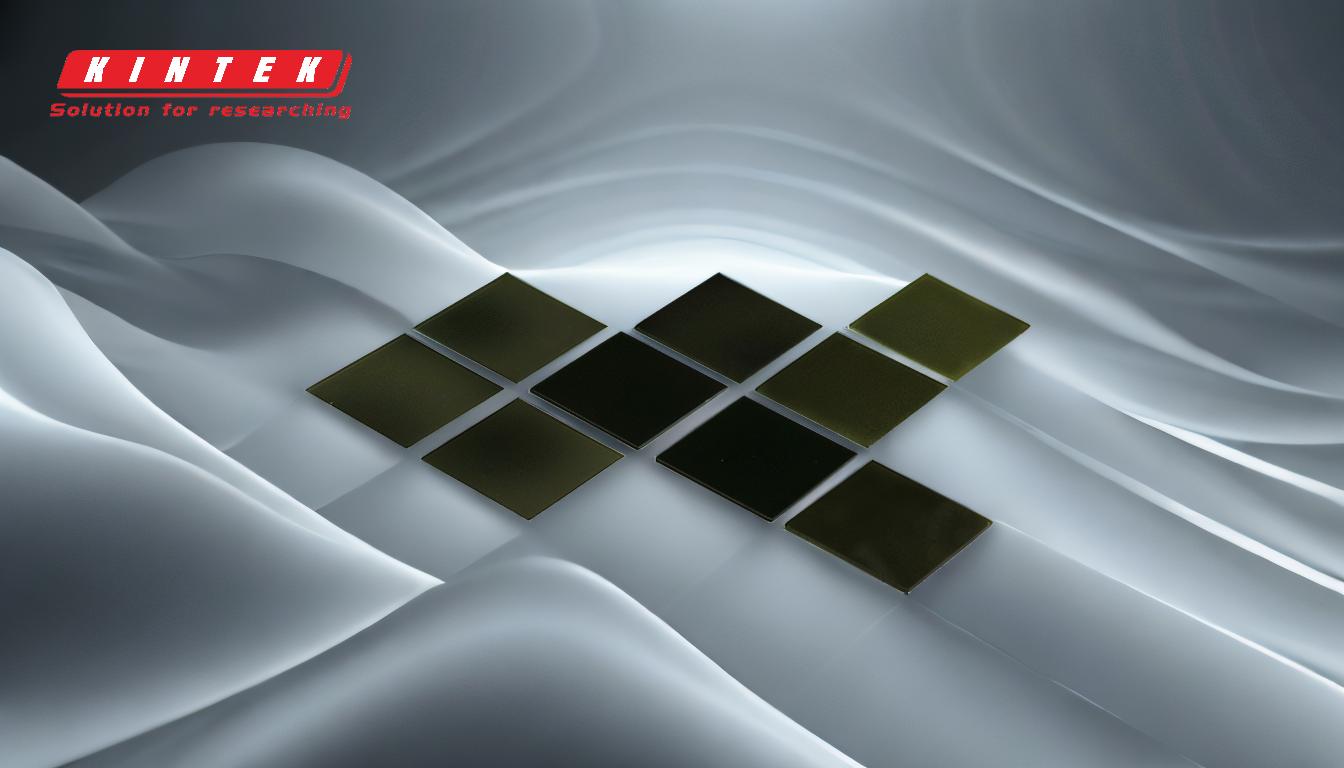
-
Base Material of DLC Coating:
- DLC coatings are fundamentally composed of carbon, specifically in an amorphous form.
- This carbon can be either pure or hydrogenated, meaning it may contain hydrogen atoms bonded within the carbon matrix.
-
Bonding Structure:
- The carbon atoms in DLC coatings form two types of bonds: sp3 (diamond-like) and sp2 (graphite-like).
- sp3 Bonds: These are tetrahedral bonds, similar to those found in diamond, contributing to the high hardness and durability of the coating.
- sp2 Bonds: These are trigonal bonds, similar to those in graphite, providing some flexibility and lubricating properties.
- The ratio of sp3 to sp2 bonds can vary, influencing the specific properties of the DLC coating.
- The carbon atoms in DLC coatings form two types of bonds: sp3 (diamond-like) and sp2 (graphite-like).
-
Amorphous Nature:
- Unlike crystalline forms of carbon (such as diamond or graphite), DLC is amorphous, meaning it lacks a long-range ordered structure.
- This amorphous nature allows for a combination of properties from both diamond and graphite, making DLC coatings versatile in their applications.
-
Hydrogenated Variants:
- Some DLC coatings contain hydrogen, which can further modify their properties.
- Hydrogenated DLC (a-C:H) typically has a higher sp3 content, enhancing hardness and wear resistance.
-
Properties of DLC Coatings:
- High Hardness: DLC coatings typically have a hardness ranging from 1500 to 3000 HV (Vickers hardness), making them extremely resistant to wear.
- Low Coefficient of Friction: The presence of sp2 bonds reduces friction, making DLC coatings ideal for sliding applications.
- Chemical Inertness: DLC coatings are resistant to corrosion and chemical attack, making them suitable for harsh environments.
- Surface Smoothness: The coatings provide a very smooth surface, which further reduces friction and wear.
-
Deposition Process:
- DLC coatings are typically deposited using plasma-enhanced chemical vapor deposition (PECVD) or other similar techniques.
- During the process, hydrocarbons (compounds of hydrogen and carbon) are introduced into a plasma, where they break down and recombine on the substrate surface to form the DLC coating.
-
Applications:
- Automotive Industry: Used in components like camshafts, bearings, and power trains to reduce friction and improve energy efficiency.
- Machinery: Applied to parts that require high wear resistance and low friction, such as gears and sliding components.
- Other Industries: Also used in medical devices, cutting tools, and consumer electronics for their protective and performance-enhancing properties.
In summary, the base material of DLC coatings is carbon, with a unique combination of sp3 and sp2 bonds that give it a blend of diamond-like hardness and graphite-like lubrication. This makes DLC coatings highly valuable in applications requiring durability, low friction, and resistance to wear and corrosion.
Summary Table:
Key Aspect | Details |
---|---|
Base Material | Amorphous carbon, often hydrogenated |
Bonding Structure | Combination of sp3 (diamond-like) and sp2 (graphite-like) bonds |
Properties | High hardness (1500-3000 HV), low friction, chemical inertness, smoothness |
Deposition Process | Plasma-enhanced chemical vapor deposition (PECVD) |
Applications | Automotive, machinery, medical devices, cutting tools, consumer electronics |
Learn how DLC coatings can enhance your products—contact our experts today!