The cheapest molding process typically depends on the specific requirements of the project, such as the material, complexity, and volume of production. However, injection molding is often considered one of the most cost-effective methods for high-volume production due to its efficiency and scalability. For low-volume or prototype production, compression molding or rotational molding might be more economical. Each process has its own advantages and limitations, so the choice should align with the project's needs, including material compatibility, part complexity, and desired production speed.
Key Points Explained:
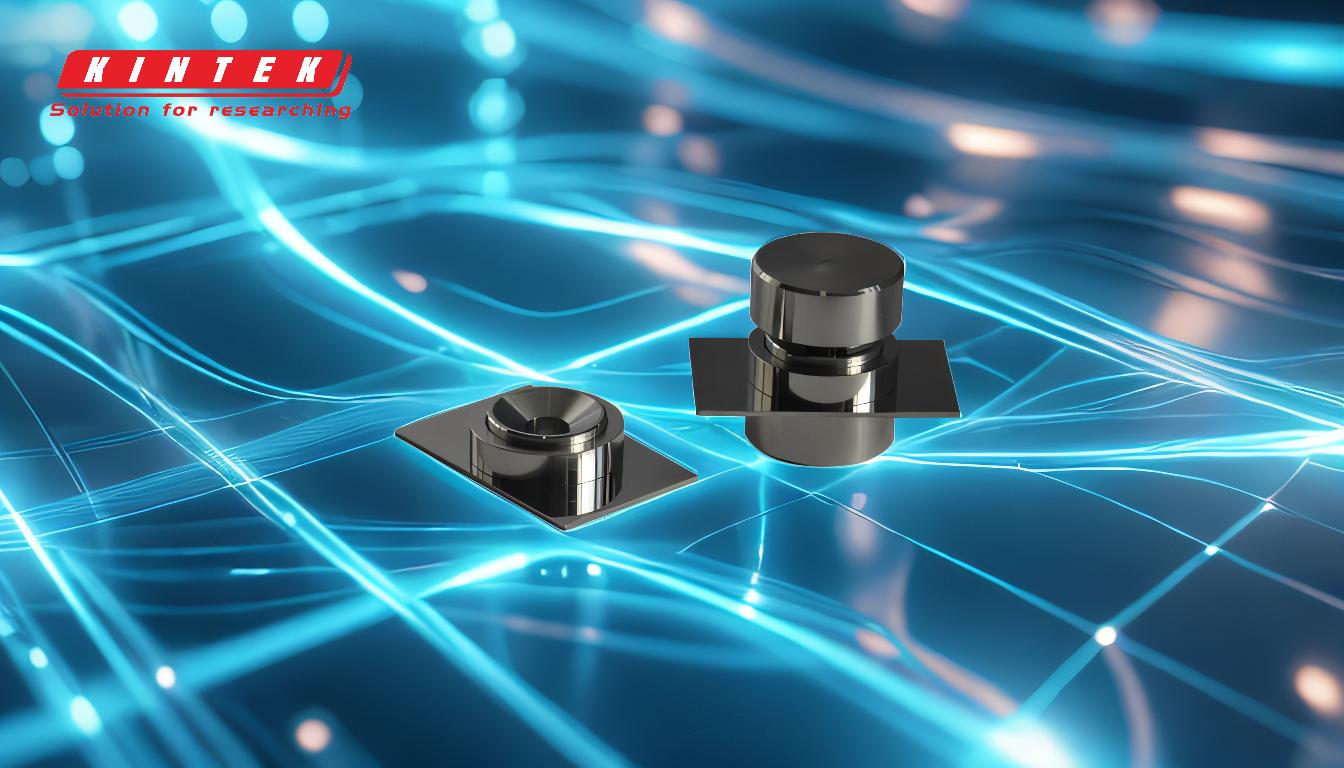
-
Injection Molding
- Cost-Effectiveness for High Volumes: Injection molding is highly efficient for mass production, as it allows for rapid production cycles and minimal material waste. The initial tooling costs can be high, but the per-unit cost decreases significantly with higher volumes.
- Material Versatility: This process works well with a wide range of materials, including plastics, metals, and composites, making it adaptable to various industries.
- Precision and Repeatability: Injection molding produces high-precision parts with consistent quality, which is ideal for industries requiring tight tolerances.
-
Compression Molding
- Lower Tooling Costs: Compression molding typically has lower upfront tooling costs compared to injection molding, making it a more affordable option for smaller production runs.
- Suitable for Thermosetting Materials: This process is ideal for materials like rubber and thermosetting plastics, which cannot be processed using injection molding.
- Simpler Equipment: The machinery used in compression molding is generally less complex and less expensive, reducing overall costs.
-
Rotational Molding
- Cost-Effective for Large, Hollow Parts: Rotational molding is ideal for producing large, hollow parts like tanks or containers. The process uses relatively inexpensive molds and is well-suited for low to medium production volumes.
- Material Efficiency: This method minimizes material waste, as the material is evenly distributed within the mold during the rotational process.
- Low Initial Investment: The equipment and tooling costs for rotational molding are lower compared to other methods, making it a budget-friendly option for certain applications.
-
Blow Molding
- Economical for Hollow Plastic Products: Blow molding is a cost-effective solution for producing hollow plastic products like bottles and containers. It is particularly efficient for high-volume production.
- Fast Production Cycles: The process allows for quick production cycles, reducing labor costs and increasing output.
- Material Savings: Blow molding uses less material compared to other methods, as it only requires a thin layer of material to form the product.
-
Factors Influencing Cost
- Material Selection: The type of material used significantly impacts the overall cost. Some materials are more expensive or require specialized processing, which can increase costs.
- Part Complexity: More complex parts may require more expensive molds or additional processing steps, driving up costs.
- Production Volume: High-volume production typically reduces per-unit costs, while low-volume or custom production may be more expensive per unit.
- Tooling and Equipment: The initial investment in molds and machinery can vary widely depending on the process, affecting the overall cost-effectiveness.
-
Choosing the Right Process
- Evaluate Project Requirements: Consider factors such as production volume, part complexity, material type, and budget constraints when selecting a molding process.
- Consult with Experts: Engaging with manufacturers or engineers can help identify the most cost-effective solution for your specific needs.
- Prototype Testing: For new projects, creating prototypes using different molding processes can provide insights into cost, quality, and feasibility before committing to full-scale production.
By carefully analyzing these factors, you can determine the most economical molding process for your project, balancing upfront costs with long-term efficiency and quality.
Summary Table:
Molding Process | Best For | Key Advantages |
---|---|---|
Injection Molding | High-volume production | Cost-effective for mass production, material versatility, high precision |
Compression Molding | Low-volume or thermosetting materials | Lower tooling costs, simpler equipment, suitable for rubber and thermosetting plastics |
Rotational Molding | Large, hollow parts | Low initial investment, material efficiency, ideal for tanks and containers |
Blow Molding | Hollow plastic products | Economical for bottles and containers, fast production cycles, material savings |
Need help choosing the right molding process for your project? Contact our experts today for personalized advice!