The cold isostatic press (CIP) process is a powder compaction method used to create solid, homogeneous materials from powdered substances. It involves placing a powder-filled elastomeric mold into a pressure chamber filled with a liquid medium, such as water or oil. Pressure is uniformly applied from all directions, typically ranging from 100 to 600 MPa, to compact the powder into a dense, solid "green body." This process is based on Pascal’s law, ensuring uniform pressure distribution. The resulting compact exhibits minimal distortion or cracking and is suitable for further machining or sintering. CIP is ideal for producing parts with complex shapes or large height-to-diameter ratios, offering high green density and structural integrity.
Key Points Explained:
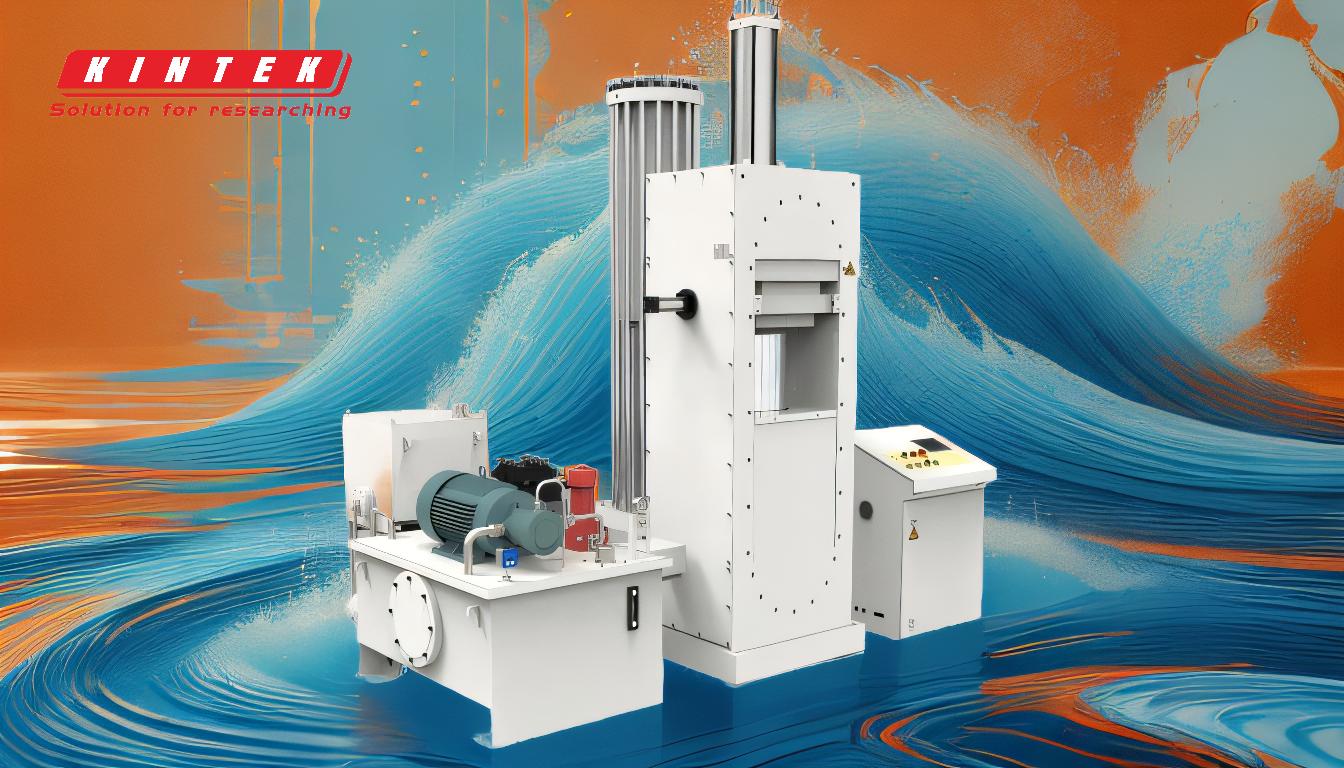
-
Definition and Purpose of Cold Isostatic Pressing (CIP):
- CIP is a powder compaction technique used to create solid, homogeneous materials from powdered substances.
- It is particularly useful for producing high-integrity billets or preforms that exhibit minimal distortion or cracking during subsequent firing or sintering processes.
-
Process Overview:
- A powder-filled elastomeric mold (or vacuumed sample) is placed into a pressure chamber.
- The chamber is filled with a liquid medium, typically water with a corrosion inhibitor or oil.
- Pressure is applied uniformly from all directions, typically ranging from 100 to 600 MPa, to compact the powder into a dense, solid "green body."
-
Working Principle:
- The process is based on Pascal’s law, which states that pressure applied to an enclosed fluid is transmitted uniformly in all directions.
- This ensures that the powder is compacted evenly, resulting in a uniform green density and structural integrity.
-
Pressure Application:
- The pressure is applied using an external pump, and the pressure chamber is designed to withstand cyclic loading and fatigue failure.
- The pressure is held for a specific duration, typically ranging from 30 seconds to 5 minutes, depending on the material and desired outcome.
-
Liquid Medium:
- The liquid medium used in the process can be water, oil, or a glycol mixture.
- The choice of liquid depends on the material being processed and the required pressure range.
-
Temperature Conditions:
- The process is conducted at room temperature or slightly higher temperatures (<93°C).
- This ensures that the powder particles bond mechanically without undergoing significant thermal deformation.
-
Resulting Green Body:
- The compacted powder forms a "green body" with sufficient strength for handling and further processing.
- The green body is then typically sintered or subjected to hot isostatic pressing (HIP) to achieve final strength and density.
-
Advantages of CIP:
- Uniform green density, even for parts with complex shapes or large height-to-diameter ratios.
- Minimal distortion or cracking during firing or sintering.
- Suitable for a wide range of materials, including metals, ceramics, and composites.
-
Applications:
- CIP is widely used in industries such as aerospace, automotive, and medical devices.
- It is particularly useful for producing parts with complex geometries or those requiring high structural integrity.
-
Post-Processing:
- After compaction, the green body may require machining or additional processing before sintering.
- The liquid medium is removed, and the elastomeric mold returns to its original shape, allowing the product to be retrieved.
-
Pressure Cycle:
- The pressing cycle involves placing the sealed bag with parts into the liquid medium, ensuring the correct liquid level, and closing the CIP.
- The pressure is increased to the desired level, and any significant drop in pressure is checked to ensure proper assembly and sealing.
-
Material Considerations:
- The choice of powder material and elastomeric mold is critical for achieving the desired properties in the final product.
- The process is adaptable to a wide range of materials, making it versatile for various applications.
In summary, the cold isostatic press process is a versatile and efficient method for compacting powdered materials into solid, homogeneous forms. Its ability to apply uniform pressure from all directions ensures high-quality, distortion-free compacts suitable for further processing. This makes CIP an essential technique in industries requiring high-integrity components with complex geometries.
Summary Table:
Key Aspect | Details |
---|---|
Process | Powder-filled elastomeric mold is pressurized uniformly (100-600 MPa). |
Working Principle | Based on Pascal’s law for uniform pressure distribution. |
Liquid Medium | Water, oil, or glycol mixture. |
Temperature | Room temperature or slightly higher (<93°C). |
Resulting Green Body | Dense, solid compacts with minimal distortion or cracking. |
Advantages | Uniform density, complex shapes, high structural integrity. |
Applications | Aerospace, automotive, medical devices, and more. |
Discover how CIP can enhance your manufacturing process—contact our experts today!