Chemical vapor deposition (CVD) is a critical process in nanotechnology, enabling the fabrication of high-purity nanostructures with precise control over material properties. The process involves introducing gaseous reactants into a reaction chamber, where they chemically react on a heated substrate to form a thin film. Key parameters such as substrate type, temperature, and gas composition can be adjusted to tailor the material's properties. CVD is versatile, allowing the production of simple thin films, complex hybrid structures, and nanomaterials like nanotubes. It is widely used in industries such as nanoelectronics, medicine, and space technology due to its ability to create materials with specific functionalities.
Key Points Explained:
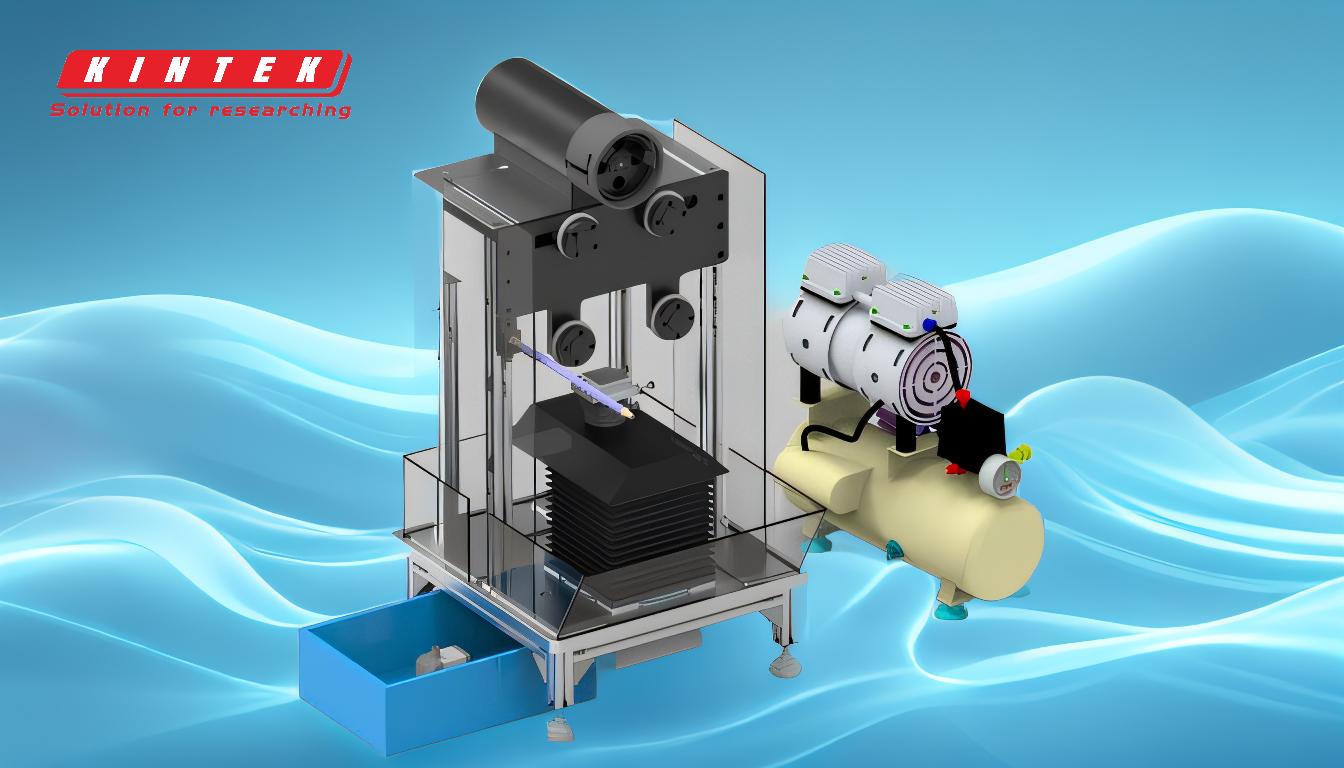
-
Definition and Purpose of CVD:
- CVD is a process used to deposit thin films of materials onto a substrate through chemical reactions of gaseous precursors.
- It is essential in nanotechnology for creating high-purity, precise nanostructures such as nanotubes, thin films, and hybrid materials.
-
Key Components of the CVD Process:
- Reaction Chamber: A controlled environment where the chemical reactions occur.
- Gaseous Precursors: Reactive gases (e.g., carbon, hydrogen, oxygen) or volatile compounds (e.g., halides, hydrides) that decompose or react on the substrate.
- Substrate: The surface onto which the material is deposited. It can be a wafer, diamond seed, or other materials.
- Temperature Control: The substrate is heated to high temperatures (typically 800–1400 °C) to facilitate the chemical reaction and deposition.
-
Steps in the CVD Process:
- Gas Introduction: Precursor gases are introduced into the reaction chamber, often using carrier gases.
- Chemical Reaction: The gases react on or near the heated substrate, forming a solid material.
- Film Deposition: The reaction products deposit onto the substrate, forming a thin film or nanostructure.
- Waste Gas Removal: By-products and unreacted gases are pumped out of the chamber.
-
Parameters Influencing CVD:
- Substrate Type: Determines the compatibility and adhesion of the deposited material.
- Temperature: Controls the reaction kinetics and the quality of the deposited film.
- Gas Composition: Affects the chemical reactions and the properties of the final material.
- Pressure and Flow Rate: Influence the uniformity and deposition rate of the film.
-
Applications of CVD in Nanotechnology:
- Nanotubes and Nanowires: CVD is widely used to grow single-walled and multi-walled carbon nanotubes.
- Thin Films: Essential for creating coatings in electronics, optics, and protective layers.
- Hybrid Structures: Enables the fabrication of complex materials like intermetallic oxides and multicomponent layers.
- Nanoelectronics: Used in the production of semiconductor devices and integrated circuits.
- Medicine and Space: CVD materials are used in biomedical devices and space technology due to their durability and functionality.
-
Advantages of CVD:
- High Purity: Produces materials with minimal impurities.
- Precision: Allows precise control over film thickness and composition.
- Versatility: Can deposit a wide range of materials, including metals, non-metals, and polymers.
- Scalability: Suitable for both laboratory-scale research and industrial production.
-
Challenges and Considerations:
- High Temperatures: Requires energy-intensive heating, which can limit substrate options.
- Cost: Equipment and precursor gases can be expensive.
- Complexity: Optimizing parameters for specific materials can be challenging.
- Safety: Handling reactive gases and high temperatures requires stringent safety measures.
-
Future Prospects:
- CVD continues to evolve with advancements in precursor chemistry, reactor design, and process control.
- Emerging applications include flexible electronics, energy storage devices, and advanced coatings for extreme environments.
In summary, CVD is a foundational technology in nanotechnology, offering unparalleled control over material synthesis and enabling the development of innovative materials for diverse applications. Its adaptability and precision make it indispensable in modern science and industry.
Summary Table:
Aspect | Details |
---|---|
Definition | A process to deposit thin films via chemical reactions of gaseous precursors. |
Key Components | Reaction chamber, gaseous precursors, substrate, temperature control. |
Steps | Gas introduction, chemical reaction, film deposition, waste gas removal. |
Key Parameters | Substrate type, temperature, gas composition, pressure, flow rate. |
Applications | Nanotubes, thin films, hybrid structures, nanoelectronics, medicine, space. |
Advantages | High purity, precision, versatility, scalability. |
Challenges | High temperatures, cost, complexity, safety concerns. |
Future Prospects | Flexible electronics, energy storage, advanced coatings. |
Ready to explore how CVD can revolutionize your projects? Contact our experts today!