Ball mills and planetary ball mills are both grinding equipment used to reduce particle size, but they differ significantly in their design, operation, and performance. A standard ball mill typically rotates a cylindrical jar horizontally, relying on gravity and tumbling action to grind materials. In contrast, a planetary ball mill features jars that rotate on a disc in the opposite direction, generating higher kinetic energy and producing smaller particle sizes. Planetary ball mills are more advanced, offering features like programmable controls, enhanced grinding efficiency, and quieter operation. They are ideal for applications requiring ultrafine grinding, while standard ball mills are better suited for larger-scale, less precise grinding tasks.
Key Points Explained:
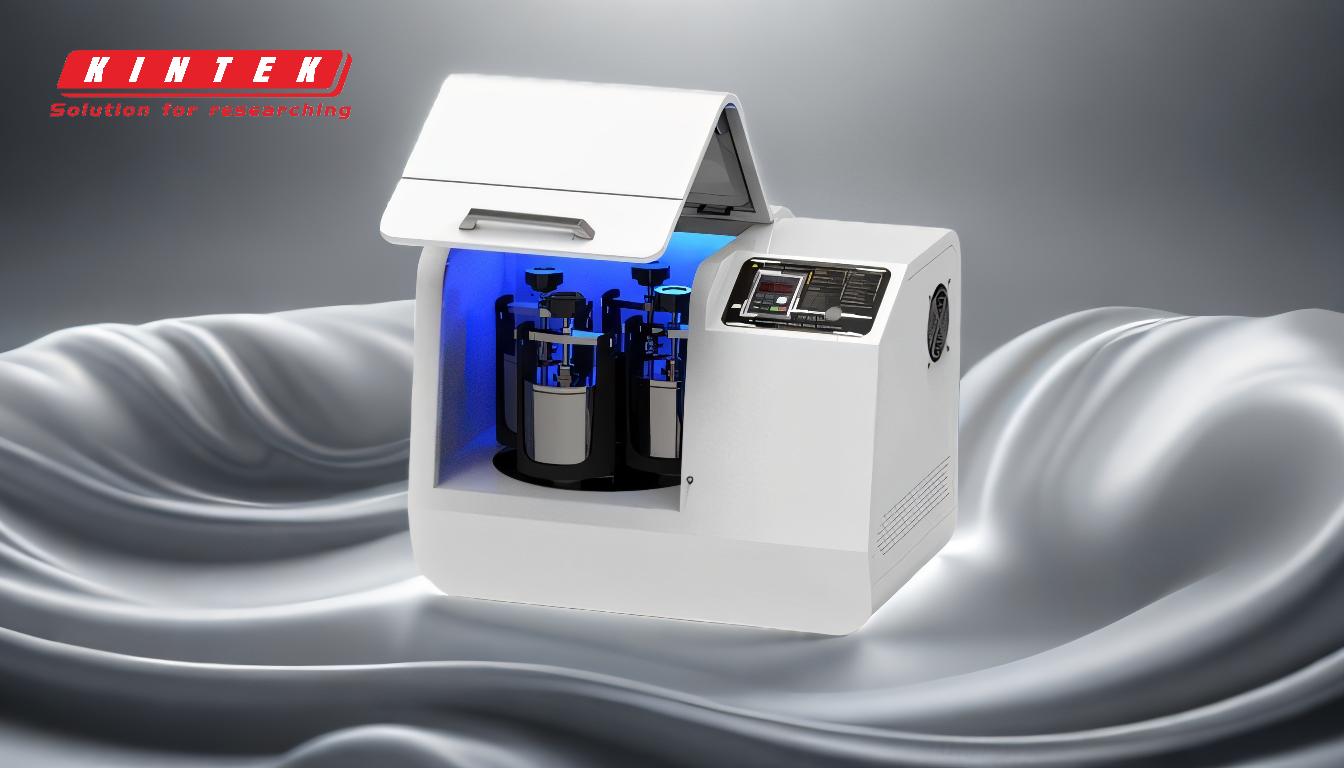
-
Operating Principle:
- Standard Ball Mill: Operates by rotating a cylindrical jar horizontally. The grinding balls inside the jar move due to gravity and tumbling action, which crushes and grinds the material.
- Planetary Ball Mill: Features jars mounted on a rotating disc that moves in the opposite direction to the jar rotation. This dual rotation generates higher kinetic energy, resulting in more intense grinding action.
-
Grinding Efficiency:
- Standard Ball Mill: Suitable for coarse to medium grinding. The grinding action is less intense, making it ideal for materials that do not require ultrafine particle sizes.
- Planetary Ball Mill: Provides significantly higher grinding energy due to the opposing rotation of the jars and disc. This allows for the production of much smaller particle sizes, making it ideal for applications requiring ultrafine or nano-sized particles.
-
Design and Features:
- Standard Ball Mill: Typically simpler in design, with fewer advanced features. It is often used for larger-scale operations due to its straightforward mechanism.
- Planetary Ball Mill: Includes advanced features such as an LCD control panel, programmable milling segments, and safety mechanisms. It also has a special gear design for reduced noise and vibration, making it more user-friendly and precise.
-
Capacity:
- Standard Ball Mill: Available in a wide range of capacities, from small laboratory sizes to industrial-scale models capable of handling several hundred liters.
- Planetary Ball Mill: Generally designed for smaller-scale operations, focusing on precision and high-energy grinding rather than large-volume processing.
-
Applications:
- Standard Ball Mill: Commonly used in industries like mining, ceramics, and construction for grinding ores, clinker, and other bulk materials.
- Planetary Ball Mill: Preferred in research and development, pharmaceuticals, and materials science for applications requiring ultrafine grinding, such as nanoparticle production and advanced material synthesis.
-
Energy Consumption:
- Standard Ball Mill: Generally consumes less energy per unit volume compared to planetary ball mills, making it more cost-effective for large-scale operations.
- Planetary Ball Mill: Consumes more energy due to its high-speed rotation and intense grinding action, but this is justified by its ability to produce finer particles.
-
Noise and Vibration:
- Standard Ball Mill: Can be noisy and produce significant vibration, especially at higher speeds.
- Planetary Ball Mill: Designed with features to minimize noise and vibration, making it more suitable for laboratory environments where quiet operation is essential.
-
Customization:
- Standard Ball Mill: Limited customization options, typically available in standard sizes and configurations.
- Planetary Ball Mill: Offers customization options such as different power supply voltages (110V, 220V, or 380V) and programmable milling segments, allowing for greater flexibility in operation.
By understanding these differences, equipment and consumable purchasers can make informed decisions based on their specific grinding needs, whether for large-scale industrial applications or precise laboratory research.
Summary Table:
Aspect | Standard Ball Mill | Planetary Ball Mill |
---|---|---|
Operating Principle | Rotates horizontally; relies on gravity and tumbling action. | Jars rotate on a disc in opposite directions, generating higher kinetic energy. |
Grinding Efficiency | Suitable for coarse to medium grinding. | Ideal for ultrafine or nano-sized particle production. |
Design & Features | Simple design, fewer advanced features. | Advanced features like LCD controls, programmable milling, and reduced noise. |
Capacity | Available in small to industrial-scale sizes. | Designed for smaller-scale, precision-focused operations. |
Applications | Mining, ceramics, construction. | R&D, pharmaceuticals, materials science, and nanoparticle production. |
Energy Consumption | Lower energy consumption per unit volume. | Higher energy consumption due to intense grinding action. |
Noise & Vibration | Noisy and vibrates at higher speeds. | Minimized noise and vibration for quiet lab operations. |
Customization | Limited customization options. | Customizable power supply and programmable milling segments. |
Need help choosing the right grinding equipment for your needs? Contact our experts today for personalized advice!