Pressure switches and vacuum switches are both critical components in various industrial and mechanical systems, but they serve different purposes and operate under different conditions. A pressure switch is designed to monitor and control systems that operate under positive pressure, triggering actions when the pressure exceeds or falls below a set threshold. In contrast, a vacuum switch is specifically tailored for systems that operate under negative pressure (vacuum), activating or deactivating processes based on vacuum level changes. Understanding their differences is essential for selecting the right switch for specific applications, ensuring optimal performance and safety.
Key Points Explained:
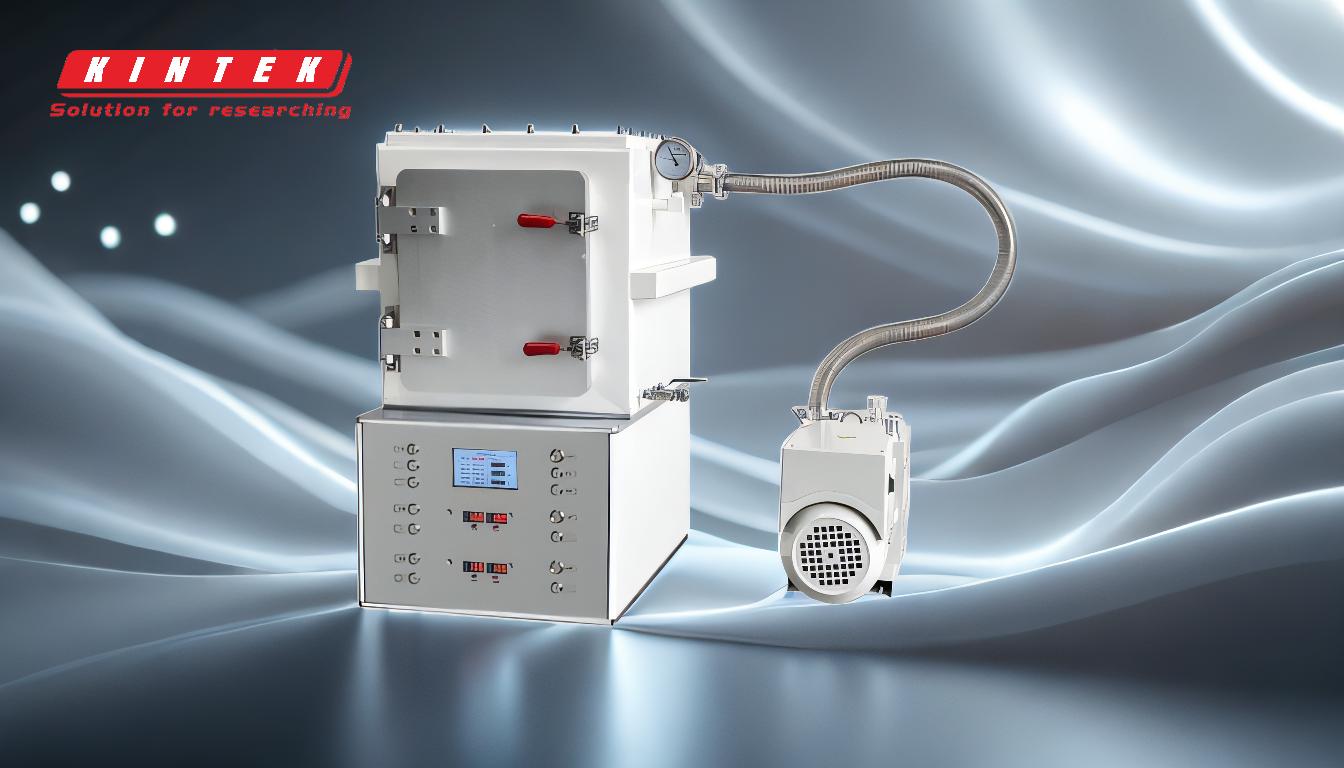
-
Definition and Functionality:
- Pressure Switch: A pressure switch detects positive pressure in a system and activates or deactivates a circuit when the pressure reaches a predetermined level. It is commonly used in applications like hydraulic systems, air compressors, and water pumps.
- Vacuum Switch: A vacuum switch monitors negative pressure (vacuum) and triggers actions when the vacuum level deviates from a set point. It is often used in vacuum pumps, HVAC systems, and industrial suction systems.
-
Operating Principles:
- Pressure Switch: Operates by sensing the force exerted by a fluid or gas under positive pressure. When the pressure exceeds or drops below the set threshold, the switch's internal mechanism (such as a diaphragm or piston) moves, opening or closing an electrical circuit.
- Vacuum Switch: Functions similarly but is calibrated to respond to negative pressure. It detects the absence of pressure (vacuum) and activates when the vacuum level reaches the desired range.
-
Applications:
- Pressure Switch: Widely used in systems where maintaining specific pressure levels is critical, such as in compressed air systems, hydraulic presses, and boiler controls.
- Vacuum Switch: Essential in applications requiring precise vacuum control, such as vacuum packaging, semiconductor manufacturing, and medical suction devices.
-
Design and Construction:
- Pressure Switch: Typically built with robust materials to withstand high-pressure environments. It often includes a diaphragm or bellows mechanism to detect pressure changes.
- Vacuum Switch: Designed to handle low-pressure environments and may include specialized components like vacuum chambers or sensors to accurately measure negative pressure.
-
Calibration and Sensitivity:
- Pressure Switch: Calibrated for positive pressure ranges, with sensitivity tailored to the specific application. It may include adjustable set points for flexibility.
- Vacuum Switch: Calibrated for negative pressure ranges, with sensitivity optimized for detecting subtle changes in vacuum levels.
-
Safety Considerations:
- Pressure Switch: Ensures safety by preventing over-pressurization or under-pressurization in systems, which could lead to equipment failure or hazards.
- Vacuum Switch: Protects systems from vacuum-related issues, such as loss of suction or contamination, which could compromise performance or safety.
-
Selection Criteria:
- Pressure Switch: Choose based on the pressure range, accuracy, and compatibility with the system's media (liquid or gas).
- Vacuum Switch: Select based on the required vacuum range, response time, and suitability for the specific application environment.
Understanding these differences helps in making informed decisions when selecting the appropriate switch for a given system, ensuring efficiency, reliability, and safety.
Summary Table:
Aspect | Pressure Switch | Vacuum Switch |
---|---|---|
Functionality | Detects positive pressure, activates/deactivates circuits at set thresholds. | Monitors negative pressure, triggers actions based on vacuum level changes. |
Operating Principle | Responds to force exerted by fluid/gas under positive pressure. | Calibrated for negative pressure, detects absence of pressure (vacuum). |
Applications | Hydraulic systems, air compressors, water pumps, boiler controls. | Vacuum pumps, HVAC systems, semiconductor manufacturing, medical suction devices. |
Design | Robust materials, diaphragm/bellows mechanism for pressure detection. | Specialized components like vacuum chambers/sensors for accurate measurement. |
Calibration | Calibrated for positive pressure ranges, adjustable set points. | Calibrated for negative pressure ranges, optimized for subtle vacuum changes. |
Safety | Prevents over-pressurization or under-pressurization, ensuring system safety. | Protects against vacuum-related issues like loss of suction or contamination. |
Selection Criteria | Pressure range, accuracy, compatibility with system media (liquid/gas). | Vacuum range, response time, suitability for specific application environments. |
Need help selecting the right switch for your application? Contact our experts today for personalized guidance!