Batch and continuous reactors for pyrolysis differ significantly in terms of operation, efficiency, design complexity, and cost. Batch reactors operate in cycles, requiring repeated heating and cooling, which impacts thermal efficiency and product quality stability. They are simpler in design, offer flexibility in feeding methods, and have lower investment and operating costs. Continuous reactors, on the other hand, operate without interruption, ensuring higher efficiency, consistent product quality, and larger single-machine capacity. However, they require more rigorous material pretreatment, have more complex equipment designs, and involve higher investment and operational costs. Continuous reactors also demand better equipment matching and automatic control capabilities, making them more suitable for high-volume, stable operations.
Key Points Explained:
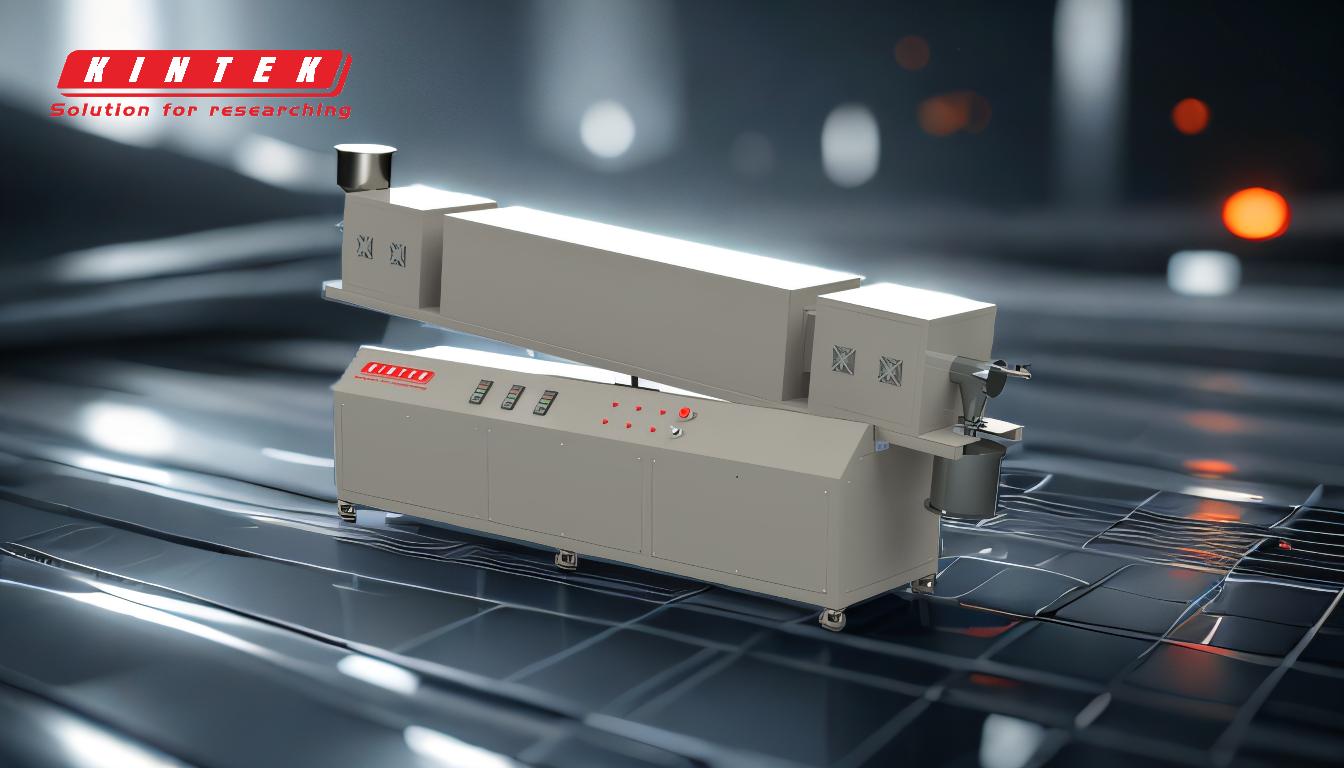
-
Operation Mode:
- Batch Reactors: Operate in cycles, involving stages of feeding, pyrolysis, and discharging slag. This cyclic process requires repeated heating and cooling, which reduces thermal efficiency and makes it challenging to maintain consistent product quality.
- Continuous Reactors: Operate without interruption, allowing for continuous feeding, pyrolysis, and slag discharge. This ensures higher efficiency and consistent product quality, as the system maintains a stable high-temperature environment.
-
Efficiency and Product Quality:
- Batch Reactors: Cyclic heating and cooling lead to lower thermal efficiency and variability in product quality. The need to repeatedly heat and cool the retort reduces overall efficiency.
- Continuous Reactors: Maintain a constant high-temperature environment, resulting in higher thermal efficiency and more stable product quality. The continuous operation eliminates the inefficiencies associated with cyclic processes.
-
Design Complexity and Equipment Requirements:
- Batch Reactors: Simpler in design, requiring less complex equipment and lower levels of automation. This makes them more versatile and easier to adapt to various applications without significant redesign.
- Continuous Reactors: More complex in design, requiring advanced equipment matching and automatic control capabilities. The integration of feeding, pyrolysis, and slag discharge systems increases design complexity but enhances operational efficiency.
-
Material Pretreatment:
- Batch Reactors: Offer more flexibility in feeding methods and require simpler material pretreatment. This reduces the initial preparation work and associated costs.
- Continuous Reactors: Require more rigorous material pretreatment, such as cutting and shredding waste tires, to ensure smooth operation. This increases the initial preparation work and costs but is necessary for continuous feeding and processing.
-
Investment and Operational Costs:
- Batch Reactors: Lower investment and operating costs due to simpler design and less stringent material pretreatment requirements. This makes them more accessible for smaller-scale operations or applications with variable feedstocks.
- Continuous Reactors: Higher investment and operational costs due to more complex equipment, advanced automation, and rigorous material pretreatment. However, the higher efficiency and consistent product quality can offset these costs in high-volume, stable operations.
-
Capacity and Work Intensity:
- Batch Reactors: Typically have smaller single-machine capacity and higher work intensity due to the cyclic nature of operation. This limits their suitability for large-scale, continuous production.
- Continuous Reactors: Have larger single-machine capacity and lower work intensity, making them more suitable for large-scale, continuous production. The continuous operation reduces labor requirements and increases overall productivity.
-
Heating Methods:
- Batch Reactors: Use conduction heating, which is less efficient and can lead to uneven heating and cooling cycles.
- Continuous Reactors: Use hot air heating, which provides more uniform and efficient heating, contributing to higher thermal efficiency and consistent product quality.
In summary, the choice between batch and continuous reactors for pyrolysis depends on the specific requirements of the operation, including the scale of production, desired product quality, available investment, and the complexity of material pretreatment. Batch reactors are more suitable for smaller-scale, flexible operations, while continuous reactors are better suited for large-scale, high-efficiency production with consistent product quality.
Summary Table:
Feature | Batch Reactors | Continuous Reactors |
---|---|---|
Operation Mode | Cyclic (repeated heating/cooling) | Continuous (uninterrupted operation) |
Efficiency | Lower thermal efficiency | Higher thermal efficiency |
Product Quality | Variable quality due to cyclic process | Consistent quality |
Design Complexity | Simpler design, less automation | Complex design, advanced automation |
Material Pretreatment | Flexible, simpler requirements | Rigorous pretreatment needed |
Investment Cost | Lower | Higher |
Operational Cost | Lower | Higher |
Capacity | Smaller single-machine capacity | Larger single-machine capacity |
Work Intensity | Higher due to cyclic nature | Lower due to continuous operation |
Heating Method | Conduction heating | Hot air heating |
Need help choosing the right pyrolysis reactor for your needs? Contact our experts today for personalized advice!