Crushing and pulverization are both mechanical processes used to reduce the size of solid materials, but they differ in their mechanisms, applications, and outcomes. Crushing involves applying force to break down large materials into smaller, coarse fragments, often using compressive forces. It is commonly used in industries like mining and construction. Pulverization, on the other hand, involves grinding materials into fine powders or particles, often using impact, shear, or attrition forces. It is widely used in laboratories, pharmaceuticals, and food processing. While crushing focuses on size reduction to manageable chunks, pulverization aims for a much finer, uniform particle size suitable for specific applications.
Key Points Explained:
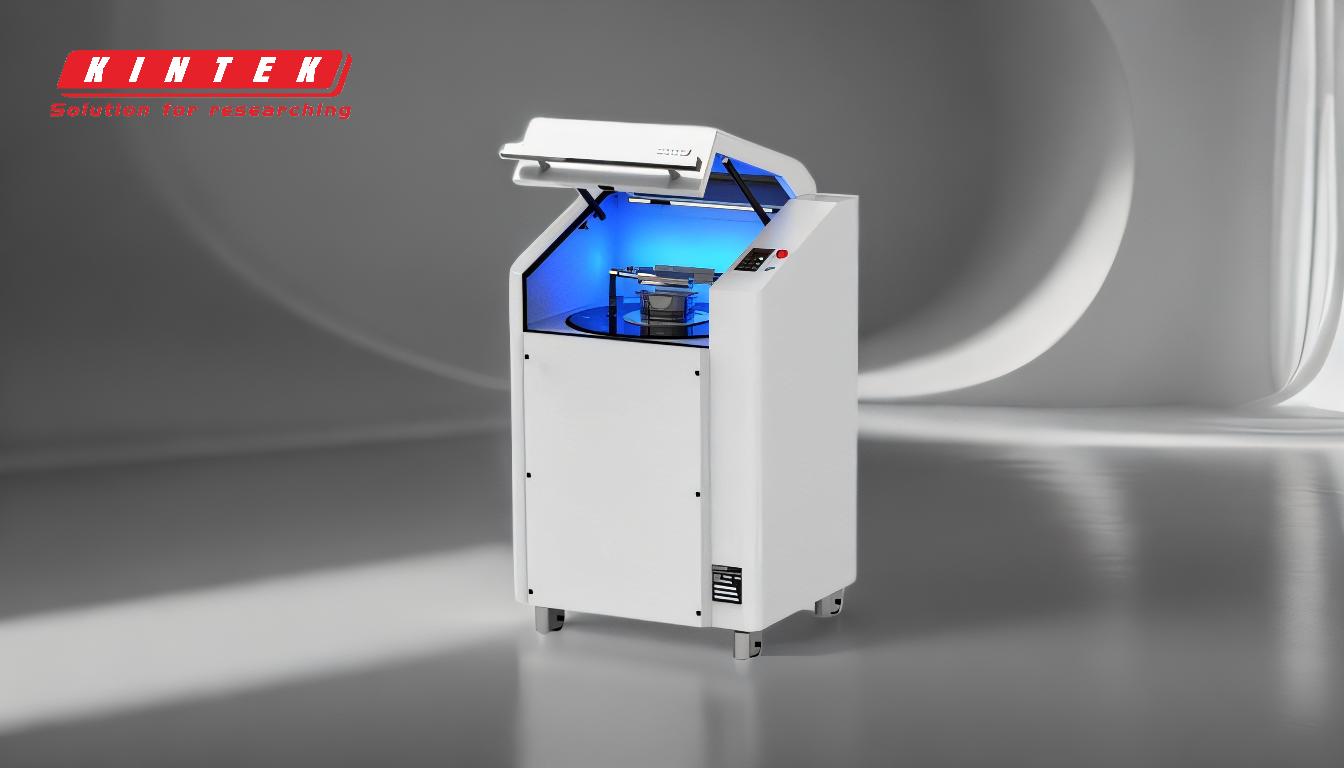
-
Definition and Mechanism:
- Crushing: A process that applies compressive force to break down large materials into smaller, coarse fragments. It is typically used for reducing the size of rocks, ores, or other hard materials.
- Pulverization: A grinding process that reduces materials into fine powders or particles using impact, shear, or attrition forces. It is used to achieve a uniform, fine particle size.
-
Applications:
- Crushing: Commonly used in industries like mining, construction, and recycling to break down large materials into smaller, manageable pieces for further processing or use.
- Pulverization: Widely used in laboratories, pharmaceuticals, food processing, and chemical industries to create fine powders for precise formulations or analyses.
-
Equipment Used:
- Crushing: Equipment includes jaw crushers, cone crushers, and roll crushers, which apply compressive force to break materials.
- Pulverization: Equipment includes ball mills, hammer mills, and jet mills, which use grinding, impact, or shear forces to reduce materials to fine particles.
-
Outcome and Particle Size:
- Crushing: Produces coarse fragments with a wide range of particle sizes, often suitable for further processing or direct use in construction.
- Pulverization: Produces fine, uniform particles with a narrow size distribution, ideal for applications requiring precise particle sizes.
-
Energy and Efficiency:
- Crushing: Generally requires less energy compared to pulverization, as it focuses on breaking materials into larger fragments.
- Pulverization: Requires more energy to achieve fine particle sizes, especially for hard or brittle materials.
-
Material Suitability:
- Crushing: Suitable for hard, dense materials like rocks, ores, and concrete.
- Pulverization: Suitable for softer materials or those requiring fine particle sizes, such as pharmaceuticals, spices, or chemicals.
By understanding these differences, equipment and consumable purchasers can select the appropriate process and machinery for their specific needs, ensuring optimal results and efficiency.
Summary Table:
Aspect | Crushing | Pulverization |
---|---|---|
Mechanism | Compressive force to break materials into coarse fragments. | Grinding, impact, or shear forces to reduce materials into fine particles. |
Applications | Mining, construction, recycling. | Laboratories, pharmaceuticals, food processing, chemical industries. |
Equipment | Jaw crushers, cone crushers, roll crushers. | Ball mills, hammer mills, jet mills. |
Particle Size | Coarse fragments with a wide size range. | Fine, uniform particles with a narrow size distribution. |
Energy Efficiency | Requires less energy. | Requires more energy for fine particle sizes. |
Material Suitability | Hard, dense materials like rocks, ores, and concrete. | Softer materials or those requiring fine particle sizes, e.g., pharmaceuticals, spices. |
Need help choosing the right process for your material processing? Contact our experts today for tailored solutions!