Single-loop controllers are designed to handle simple systems where only one variable needs to be controlled, such as maintaining the temperature in a single room. They are straightforward, cost-effective, and easy to implement for basic applications. In contrast, multi-loop controllers are used for more complex systems that involve multiple interdependent variables, such as controlling both temperature and humidity in a climate control system. These controllers offer advanced functionalities, including the ability to manage interactions between different control loops, making them suitable for sophisticated industrial processes. The choice between the two depends on the complexity of the system and the level of control required.
Key Points Explained:
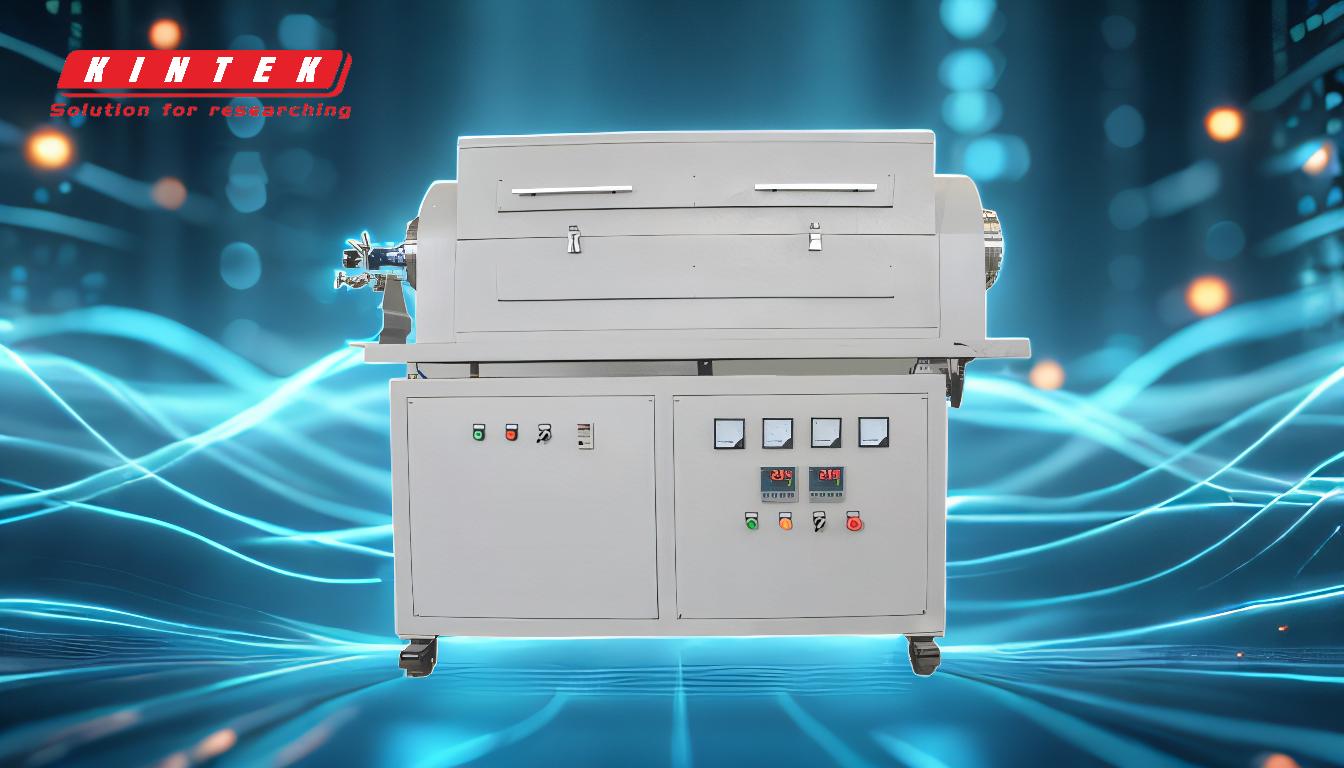
-
Definition and Purpose:
- Single-Loop Controller: A single-loop controller is designed to regulate one process variable (e.g., temperature, pressure, or flow rate) in a system. It operates by comparing the measured value of the variable with a setpoint and adjusting the control output accordingly.
- Multi-Loop Controller: A multi-loop controller manages multiple process variables simultaneously. It is capable of handling complex systems where variables are interdependent, ensuring coordinated control across all loops.
-
Application Scope:
- Single-Loop Controller: Best suited for simple, standalone systems where only one variable needs to be controlled. Examples include basic temperature control in a water heater or pressure control in a single pipeline.
- Multi-Loop Controller: Ideal for complex systems with multiple interacting variables. Examples include climate control systems (temperature and humidity), chemical reactors (temperature, pressure, and flow rate), and advanced manufacturing processes.
-
Complexity and Functionality:
- Single-Loop Controller: Simple in design and functionality, focusing on a single control loop. It is easier to configure, operate, and maintain, making it suitable for applications where simplicity and cost-effectiveness are priorities.
- Multi-Loop Controller: Offers advanced functionalities, such as the ability to manage interactions between different control loops. It can handle more sophisticated control strategies, including cascade control, feedforward control, and multivariable control, making it suitable for complex industrial processes.
-
Cost and Implementation:
- Single-Loop Controller: Generally more cost-effective due to its simpler design and lower hardware requirements. It is easier to implement and requires less expertise to set up and maintain.
- Multi-Loop Controller: Typically more expensive due to its advanced features and higher hardware requirements. It requires more expertise to configure, operate, and maintain, making it more suitable for complex industrial applications.
-
Performance and Efficiency:
- Single-Loop Controller: Provides adequate performance for simple control tasks but may not be sufficient for systems with multiple interacting variables. It may struggle to maintain optimal control in complex scenarios.
- Multi-Loop Controller: Offers superior performance and efficiency in managing complex systems. It can handle interactions between variables more effectively, ensuring better overall system performance and stability.
-
Scalability and Flexibility:
- Single-Loop Controller: Limited scalability and flexibility, as it is designed for single-variable control. It may not be easily adaptable to more complex systems or additional control requirements.
- Multi-Loop Controller: Highly scalable and flexible, capable of accommodating additional control loops and more complex control strategies. It can be adapted to a wide range of applications and system requirements.
-
Maintenance and Troubleshooting:
- Single-Loop Controller: Easier to maintain and troubleshoot due to its simpler design and fewer components. Issues can often be resolved quickly with minimal downtime.
- Multi-Loop Controller: More complex to maintain and troubleshoot due to its advanced features and multiple control loops. It may require more specialized knowledge and tools to diagnose and resolve issues.
-
User Interface and Ease of Use:
- Single-Loop Controller: Typically features a straightforward user interface, making it easy to set up and operate. It is user-friendly and requires minimal training.
- Multi-Loop Controller: May have a more complex user interface due to its advanced functionalities. It may require more training and expertise to operate effectively.
In summary, the choice between single-loop and multi-loop controllers depends on the complexity of the system and the level of control required. Single-loop controllers are suitable for simple, single-variable control tasks, while multi-loop controllers are designed for managing complex systems with multiple interdependent variables. Each type of controller has its own advantages and limitations, and the decision should be based on the specific requirements of the application.
Summary Table:
Feature | Single-Loop Controller | Multi-Loop Controller |
---|---|---|
Control Variables | Single variable (e.g., temperature) | Multiple interdependent variables |
Application Scope | Simple systems (e.g., water heater) | Complex systems (e.g., climate control) |
Complexity | Simple design, easy to implement | Advanced functionalities, complex setup |
Cost | Cost-effective | More expensive |
Performance | Adequate for simple tasks | Superior for complex systems |
Scalability | Limited | Highly scalable |
Maintenance | Easier to maintain | Requires specialized knowledge |
User Interface | Simple and user-friendly | More complex, requires training |
Need help choosing the right controller for your system? Contact our experts today for personalized advice!