The efficiency of a vibrating screen is a critical factor in determining its performance and suitability for specific applications. Efficiency refers to the ability of the screen to separate materials accurately and effectively, ensuring that the desired particle sizes are screened while minimizing waste and energy consumption. Several factors influence the efficiency of a vibrating screen, including the design of the screen, the vibration frequency and amplitude, the material properties, and the operational conditions. Understanding these factors can help optimize the screening process and achieve the desired outcomes.
Key Points Explained:
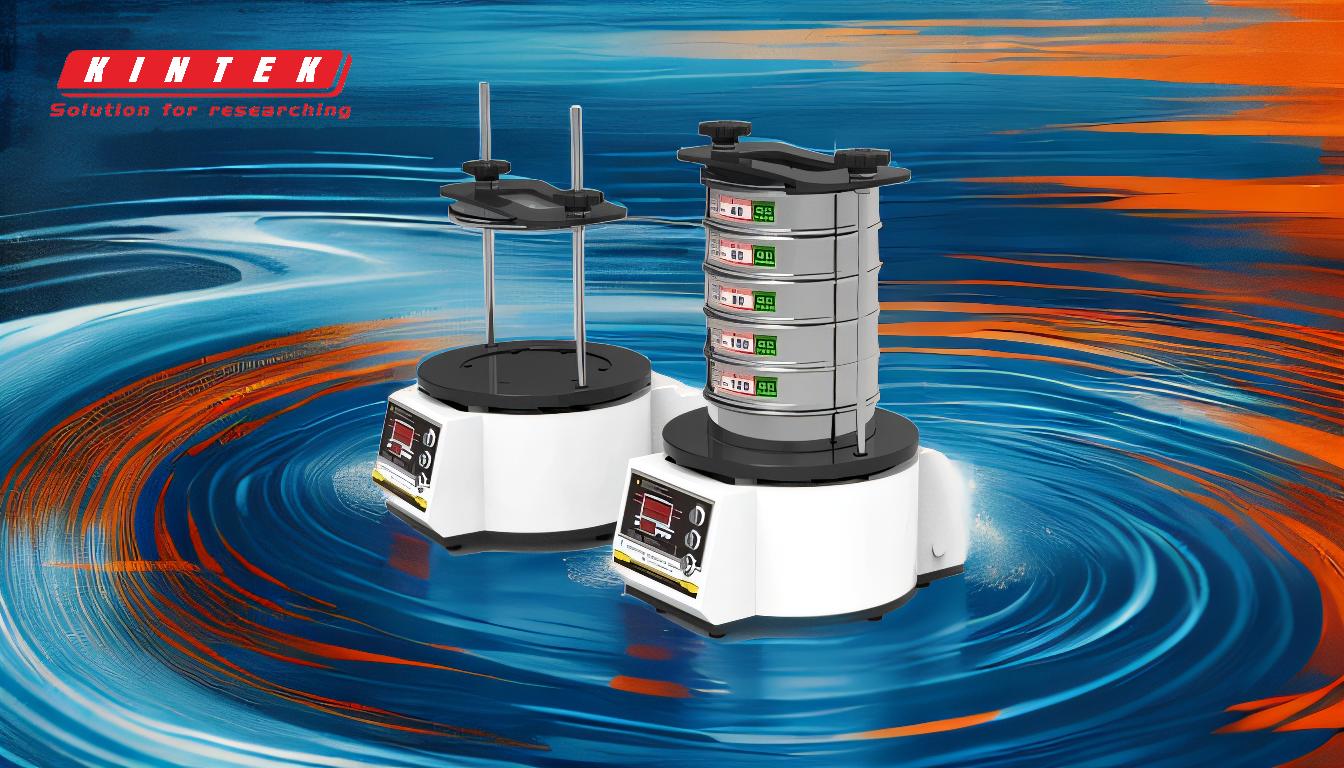
-
Definition of Efficiency in Vibrating Screens:
- Efficiency in vibrating screens refers to the percentage of material that successfully passes through the screen relative to the total amount of material fed into the screen. It measures how effectively the screen separates materials based on size.
- High efficiency means that a larger proportion of the desired material passes through the screen, while low efficiency indicates that a significant amount of material is either retained on the screen or improperly separated.
-
Factors Affecting Efficiency:
- Screen Design: The design of the screen, including the size and shape of the screen openings, plays a crucial role in determining efficiency. Screens with appropriately sized openings for the material being processed will have higher efficiency.
- Vibration Frequency and Amplitude: The frequency and amplitude of the vibrations affect how materials move across the screen. Optimal vibration settings ensure that materials are properly agitated and separated, leading to higher efficiency.
- Material Properties: The characteristics of the material being screened, such as particle size, shape, and moisture content, can impact efficiency. Materials with uniform particle sizes and shapes are generally easier to screen efficiently.
- Operational Conditions: Factors such as the feed rate, screen inclination, and the presence of moisture or contaminants can influence efficiency. Properly managing these conditions is essential for maintaining high efficiency.
-
Importance of Efficiency:
- Cost-Effectiveness: High efficiency reduces the amount of material that needs to be reprocessed or discarded, leading to cost savings in terms of energy consumption and material waste.
- Product Quality: Efficient screening ensures that the final product meets the required specifications, which is crucial for industries where product quality is paramount.
- Operational Productivity: Efficient screens can process larger volumes of material in less time, increasing overall productivity and throughput.
-
Challenges and Limitations:
- Screen Blinding: This occurs when particles block the screen openings, reducing efficiency. Regular maintenance and the use of anti-blinding devices can mitigate this issue.
- Noise and Vibration: Excessive noise and vibration can be a concern, especially in environments where noise pollution is a problem. Proper design and insulation can help reduce these effects.
- Material Contamination: Contaminants in the material can reduce efficiency by clogging the screen or altering the screening process. Pre-cleaning or pre-screening steps can help address this issue.
-
Optimizing Efficiency:
- Regular Maintenance: Keeping the screen clean and well-maintained ensures that it operates at peak efficiency. This includes checking for wear and tear, replacing damaged screens, and ensuring that all components are functioning correctly.
- Adjusting Operational Parameters: Fine-tuning the vibration frequency, amplitude, and feed rate can help optimize efficiency for specific materials and conditions.
- Using Advanced Technologies: Incorporating advanced technologies, such as automated control systems and high-performance screen materials, can enhance efficiency and overall performance.
In conclusion, the efficiency of a vibrating screen is influenced by a combination of design, operational, and material factors. By understanding and optimizing these factors, it is possible to achieve high screening efficiency, leading to cost savings, improved product quality, and increased productivity. Regular maintenance and the use of advanced technologies can further enhance the efficiency of vibrating screens, making them a valuable tool in various industrial applications.
Summary Table:
Key Aspect | Description |
---|---|
Efficiency Definition | Percentage of material passing through the screen relative to total feed. |
Factors Affecting Efficiency | Screen design, vibration settings, material properties, operational conditions. |
Importance | Cost-effectiveness, product quality, and operational productivity. |
Challenges | Screen blinding, noise, vibration, and material contamination. |
Optimization Tips | Regular maintenance, adjusting parameters, and using advanced technologies. |
Want to enhance your vibrating screen efficiency? Contact our experts today for tailored solutions!