Rotary kilns are widely used in industries such as cement, lime, and chemical production due to their ability to handle high-temperature processes efficiently. The energy efficiency of a rotary kiln depends on various factors, including design parameters, operational settings, and the use of energy recovery systems. Key factors influencing efficiency include the inclination angle, rotation speed, material flow rate, and temperature profiles. Modern designs incorporate heat recuperators, such as pre-heaters and coolers, to maximize thermal efficiency by recovering energy from exhaust gases and cooling processes. Electrically heated rotary kilns achieve energy efficiencies of over 95% due to minimal heat losses. Improvements in understanding transport phenomena within the kiln, such as particle motion and heating rates, can further enhance performance. Overall, rotary kilns are highly efficient systems when optimized for specific industrial applications.
Key Points Explained:
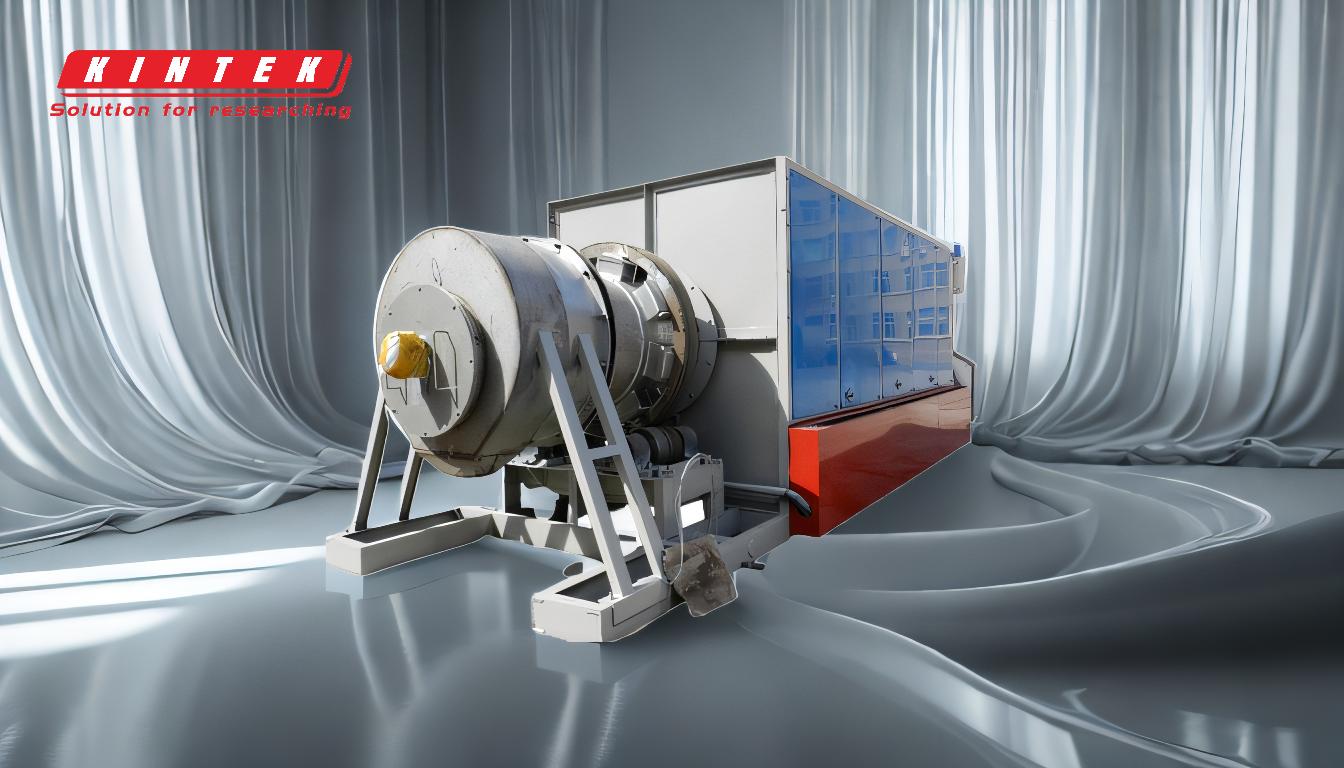
-
Operational Parameters Affecting Efficiency:
- The energy efficiency of a rotary kiln is influenced by operational parameters such as:
- Inclination angle: Determines the material's residence time in the kiln.
- Rotation speed: Affects mixing and heat transfer.
- Temperature profiles: Ensure optimal heat distribution for the process.
- Material flow rate and discharge rate: Impact the uniformity of material processing and energy consumption.
- The energy efficiency of a rotary kiln is influenced by operational parameters such as:
-
Design Considerations:
- The design of a rotary kiln must account for material properties, including:
- Particle size distribution: Influences heat transfer and material flow.
- Bulk density and abrasiveness: Affect the kiln's structural design and wear resistance.
- Thermal properties (specific heat, thermal conductivity): Determine heat requirements and energy efficiency.
- Proper design ensures the kiln operates efficiently under specific process conditions.
- The design of a rotary kiln must account for material properties, including:
-
Heat Recovery Systems:
- Modern rotary kilns incorporate heat recuperation systems to improve thermal efficiency:
- Pre-heaters: Recover energy from exhaust gases to preheat incoming material.
- Coolers: Extract heat from the product to preheat combustion air or meet other energy needs.
- These systems reduce overall energy consumption and improve process sustainability.
- Modern rotary kilns incorporate heat recuperation systems to improve thermal efficiency:
-
Electrically Heated Kilns:
- Electrically heated rotary kilns achieve energy efficiencies of over 95% due to:
- No gas flow: Eliminates energy losses associated with combustion gases.
- Minimal heat losses: Efficient insulation and precise temperature control.
- These kilns are ideal for processes requiring high-temperature precision and low environmental impact.
- Electrically heated rotary kilns achieve energy efficiencies of over 95% due to:
-
Improvements in Transport Phenomena:
- Enhancing rotary kiln performance requires a better understanding of:
- Momentum transport: Controls particle motion and mixing within the kiln.
- Energy transport: Determines the heating rate of individual particles.
- Research in these areas can lead to optimized designs and operational strategies for improved efficiency.
- Enhancing rotary kiln performance requires a better understanding of:
-
Refractory Lining Enhancements:
- Adding a layer of refractory ceramic fiber to the kiln lining improves thermal efficiency by:
- Reducing heat losses through the kiln walls.
- Enhancing insulation and maintaining higher internal temperatures.
- This modification can significantly reduce energy consumption during operation.
- Adding a layer of refractory ceramic fiber to the kiln lining improves thermal efficiency by:
-
Industrial Applications and Efficiency:
- Rotary kilns contribute to industrial efficiency by enabling processes such as:
- Calcination: Essential for cement and lime production.
- Material transformation: Used in chemical and metallurgical industries.
- Their development has been driven by the need for infrastructure projects, leading to advancements in design and energy efficiency.
- Rotary kilns contribute to industrial efficiency by enabling processes such as:
By optimizing these factors and incorporating advanced technologies, rotary kilns can achieve high energy efficiency, making them indispensable in various industrial applications.
Summary Table:
Factor | Impact on Efficiency |
---|---|
Inclination Angle | Determines material residence time and heat exposure. |
Rotation Speed | Affects mixing and heat transfer efficiency. |
Temperature Profiles | Ensures optimal heat distribution for uniform processing. |
Material Flow Rate | Influences energy consumption and processing uniformity. |
Heat Recovery Systems | Pre-heaters and coolers recover energy, reducing overall consumption. |
Refractory Lining | Enhances insulation, reducing heat loss and improving efficiency. |
Electrically Heated Kilns | Achieve >95% efficiency with minimal heat losses and precise temperature control. |
Ready to optimize your rotary kiln's efficiency? Contact our experts today for tailored solutions!