The fast pyrolysis process is a thermal decomposition method that rapidly heats biomass or organic materials in the absence of oxygen to produce bio-oil, biochar, and syngas. It is characterized by high heating rates, short residence times, and moderate temperatures, typically ranging from 400°C to 600°C. This process is widely used in pyrolysis plants to convert waste materials like oil sludge, plastics, and biomass into valuable products such as fuel oil, char, and gas. The process is efficient, environmentally friendly, and offers a sustainable solution for waste management and energy recovery.
Key Points Explained:
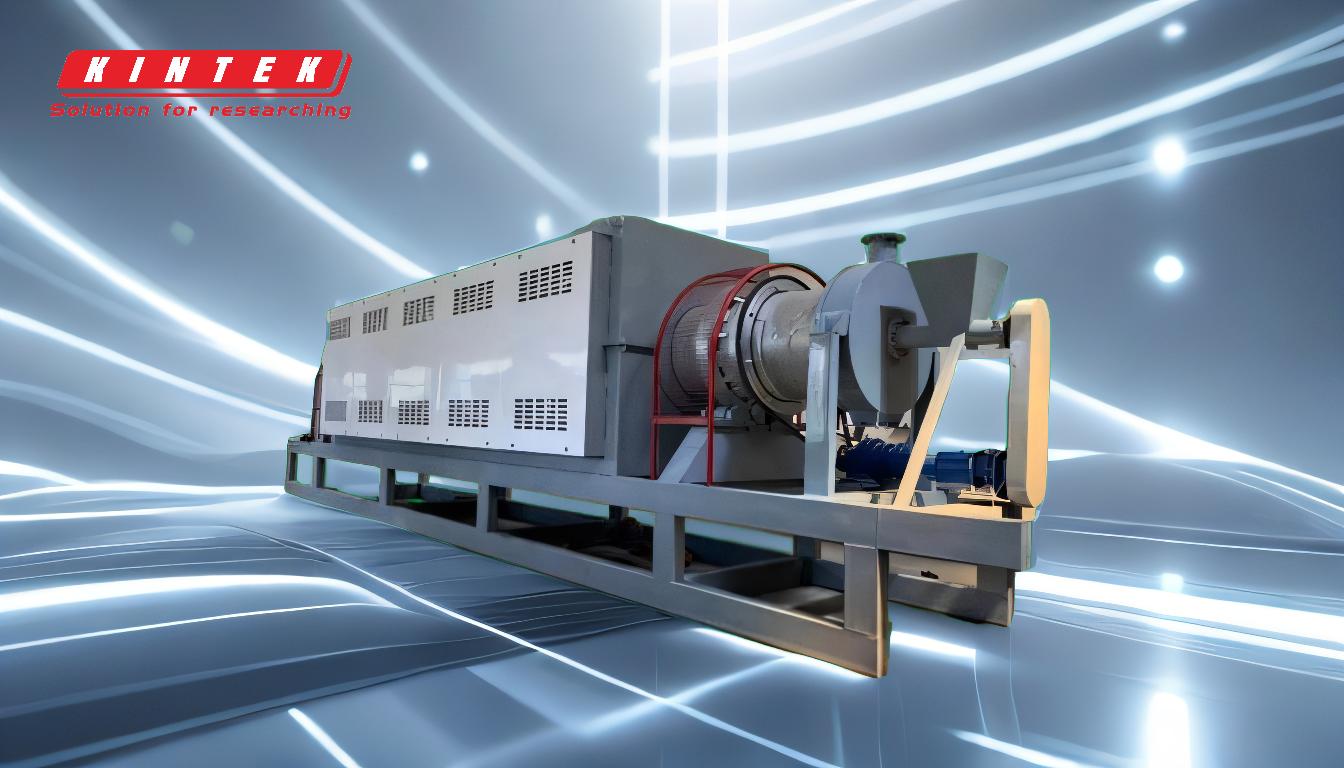
-
Definition and Purpose of Fast Pyrolysis:
- Fast pyrolysis is a thermochemical process that decomposes organic materials at high temperatures in the absence of oxygen.
- The primary goal is to maximize the production of bio-oil, a liquid fuel that can be used for energy generation or further refined into chemicals.
-
Key Steps in the Fast Pyrolysis Process:
- Feeding: Raw materials, such as oil sludge, biomass, or plastics, are fed into the reactor. In the case of oil sludge, a sealed screw conveyor ensures a continuous and controlled feed.
- Heating: The reactor is heated using external fuel sources, reaching temperatures between 400°C and 600°C. This rapid heating causes the organic material to break down into smaller molecules, producing oil gas.
- Cooling: The oil gas is then condensed into liquid fuel oil. Uncondensable gases, such as methane and hydrogen, are recycled to provide heat for the reactor, improving energy efficiency.
- Slag Discharge: Solid residues, primarily soil or char, are automatically discharged from the reactor. These residues can be further processed or used as soil amendments.
-
Advantages of Fast Pyrolysis:
- High Efficiency: The process converts a significant portion of the feedstock into usable products, minimizing waste.
- Environmental Benefits: By recycling waste materials, fast pyrolysis reduces landfill use and greenhouse gas emissions.
- Versatility: It can process a wide range of feedstocks, including agricultural waste, plastics, and industrial sludge.
-
Applications of Fast Pyrolysis:
- Energy Production: The bio-oil produced can be used as a renewable fuel for heating, electricity generation, or transportation.
- Chemical Industry: Bio-oil can be refined into chemicals and solvents, offering a sustainable alternative to petroleum-based products.
- Waste Management: Fast pyrolysis provides an effective solution for managing hazardous waste, such as oil sludge, by converting it into valuable resources.
-
Comparison with Other Pyrolysis Methods:
- Slow Pyrolysis: This method operates at lower temperatures and longer residence times, producing more biochar and less bio-oil. It is suitable for applications where biochar is the desired product.
- Gasification: Unlike fast pyrolysis, gasification produces primarily syngas (a mixture of hydrogen and carbon monoxide) and is used for power generation or synthetic fuel production.
-
Challenges and Considerations:
- Feedstock Quality: The efficiency of fast pyrolysis depends on the composition and moisture content of the feedstock. Pre-treatment may be required to optimize the process.
- Reactor Design: Advanced reactor designs are needed to ensure uniform heating and efficient heat transfer, which are critical for maximizing bio-oil yield.
- Economic Viability: The cost of setting up and operating a pyrolysis plant can be high, but the long-term benefits of waste reduction and energy recovery often justify the investment.
In summary, fast pyrolysis is a highly efficient and versatile process for converting organic waste into valuable products. Its ability to handle diverse feedstocks and produce renewable energy makes it a key technology in sustainable waste management and energy production.
Summary Table:
Aspect | Details |
---|---|
Definition | Thermal decomposition of organic materials in the absence of oxygen. |
Temperature Range | 400°C to 600°C |
Key Products | Bio-oil, biochar, and syngas |
Main Steps | Feeding, heating, cooling, and slag discharge |
Advantages | High efficiency, environmental benefits, and versatility |
Applications | Energy production, chemical industry, and waste management |
Challenges | Feedstock quality, reactor design, and economic viability |
Discover how fast pyrolysis can transform your waste into valuable resources—contact us today!