The first step in converting biomass into energy is the collection and preparation of biomass materials. This involves gathering organic materials such as wood, straw, agricultural residues, or other plant-based matter, and preparing them for further processing. Preparation may include drying, crushing, or chopping the biomass to ensure it is in a suitable form for the chosen conversion process, whether it be direct combustion, thermochemical conversion, chemical conversion, or biological conversion. This initial step is critical as it ensures the efficiency and effectiveness of the subsequent energy conversion processes.
Key Points Explained:
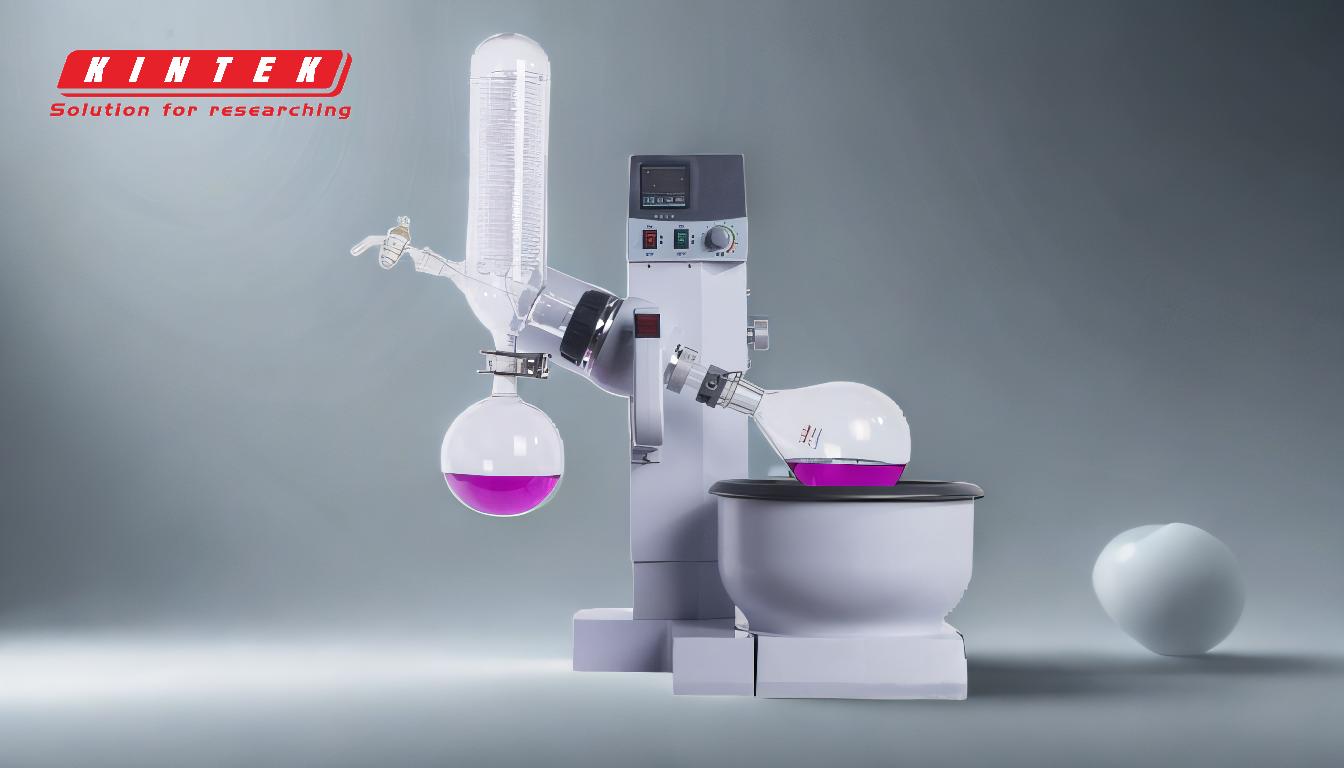
-
Collection of Biomass Materials:
- Explanation: Biomass materials are collected from various sources, including forests, agricultural fields, and industrial waste streams. Common materials include wood, straw, crop residues, and organic waste.
- Importance: The type and quality of biomass collected can significantly influence the efficiency and output of the energy conversion process.
-
Preparation of Biomass:
- Drying: Biomass often contains moisture, which can reduce the efficiency of combustion or other conversion processes. Drying the biomass reduces moisture content, making it more suitable for energy production.
- Crushing/Chopping: Biomass is often crushed or chopped into smaller pieces to increase the surface area, which facilitates more efficient combustion or chemical reactions during conversion.
- Importance: Proper preparation ensures that the biomass can be processed efficiently, leading to higher energy yields and reduced waste.
-
Selection of Conversion Method:
- Explanation: Depending on the type of biomass and the desired energy output, different conversion methods may be chosen, such as direct combustion, thermochemical conversion (e.g., pyrolysis, gasification), chemical conversion, or biological conversion (e.g., anaerobic digestion, fermentation).
- Importance: The choice of conversion method affects the efficiency, cost, and environmental impact of the energy production process.
-
Pre-Treatment for Specific Processes:
- Explanation: For certain conversion methods, additional pre-treatment steps may be required. For example, in pyrolysis, biomass may need to be dried and crushed before being heated in the absence of oxygen.
- Importance: Pre-treatment ensures that the biomass is in the optimal condition for the specific conversion process, leading to better results and fewer byproducts.
-
Transportation and Storage:
- Explanation: After collection and preparation, biomass is transported to the conversion facility and stored until it is needed. Proper storage conditions are essential to prevent degradation or loss of energy content.
- Importance: Efficient transportation and storage minimize losses and ensure a steady supply of biomass for continuous energy production.
-
Environmental and Economic Considerations:
- Explanation: The collection and preparation of biomass must be done in a way that is environmentally sustainable and economically viable. This includes considering the carbon footprint of transportation and the impact of biomass harvesting on ecosystems.
- Importance: Sustainable practices ensure that biomass energy remains a renewable and environmentally friendly energy source.
In summary, the first step in converting biomass into energy is a critical phase that involves the collection and preparation of biomass materials. This step sets the stage for the entire energy conversion process, influencing the efficiency, cost, and environmental impact of the final energy output. Proper handling and preparation of biomass are essential to ensure that the subsequent conversion processes are as effective and sustainable as possible.
Summary Table:
Step | Details | Importance |
---|---|---|
Collection | Gather organic materials like wood, straw, and agricultural residues. | Influences efficiency and output of energy conversion. |
Preparation | Dry, crush, or chop biomass to optimize it for conversion processes. | Ensures efficient processing and higher energy yields. |
Conversion Method | Choose methods like combustion, thermochemical, chemical, or biological. | Affects efficiency, cost, and environmental impact. |
Pre-Treatment | Additional steps like drying or crushing for specific processes (e.g., pyrolysis). | Optimizes biomass for specific conversion methods. |
Transportation/Storage | Transport and store biomass properly to prevent degradation. | Minimizes losses and ensures a steady supply for energy production. |
Environmental/Economic | Ensure sustainable and economically viable collection and preparation. | Maintains biomass energy as a renewable and eco-friendly energy source. |
Ready to optimize your biomass energy conversion process? Contact us today for expert guidance!