The formula for calculating the dry film thickness (DFT) of a coating is derived from the wet film thickness (WFT) and the volume solids (VS) of the coating material. The formula is straightforward: DFT = WFT × VS / 100. This equation allows you to determine the final thickness of the coating after it has dried, which is crucial for ensuring proper performance and durability of the coating. The calculation is particularly useful in reverse scenarios where you know the WFT and VS but need to determine the DFT.
Key Points Explained:
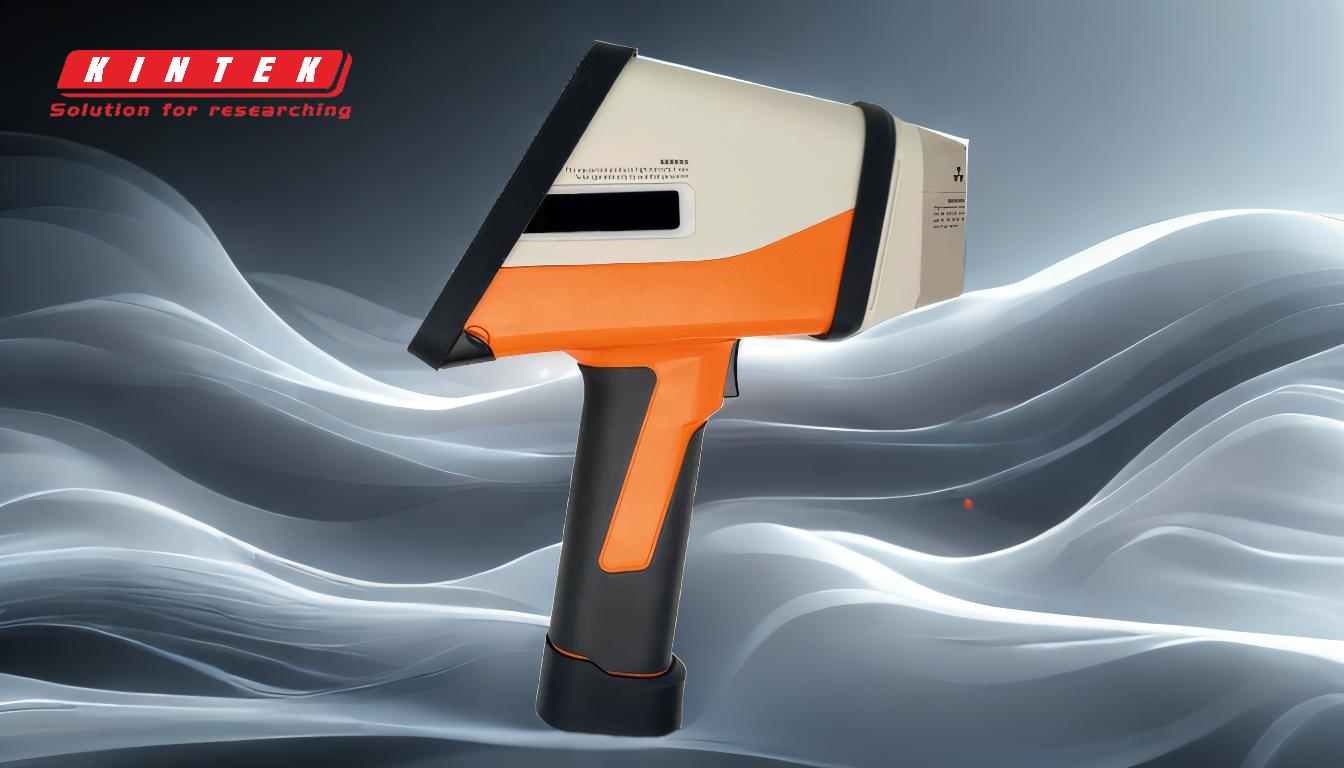
-
Understanding the Formula:
- The formula DFT = WFT × VS / 100 is used to calculate the dry film thickness.
- WFT stands for Wet Film Thickness, which is the thickness of the coating immediately after application.
- VS stands for Volume Solids, which is the percentage of the coating that remains as a solid film after the solvent or carrier has evaporated.
- DFT stands for Dry Film Thickness, which is the final thickness of the coating after drying.
-
Importance of Volume Solids (VS):
- Volume Solids is a critical factor in determining the final thickness of the coating. It represents the proportion of the coating that will form the solid film.
- For example, if a coating has a VS of 60%, it means that 60% of the wet coating will remain as a solid film after drying.
-
Example Calculation:
- Using the provided example: If the Wet Film Thickness (WFT) is 150 microns and the Volume Solids (VS) is 60%, the calculation would be:
- DFT = 150 × 60 / 100 = 90 microns.
- This means that after the coating dries, the final thickness will be 90 microns.
- Using the provided example: If the Wet Film Thickness (WFT) is 150 microns and the Volume Solids (VS) is 60%, the calculation would be:
-
Practical Application:
- This formula is essential for ensuring that the coating meets the required specifications for protection and performance.
- It is particularly useful in quality control processes, where precise measurements of coating thickness are necessary to ensure compliance with industry standards.
-
Reverse Calculation:
- The formula can also be used in reverse to determine the required Wet Film Thickness (WFT) if the desired Dry Film Thickness (DFT) and Volume Solids (VS) are known.
- For example, if you need a DFT of 90 microns and the VS is 60%, you can calculate the required WFT as:
- WFT = (DFT × 100) / VS = (90 × 100) / 60 = 150 microns.
-
Factors Affecting Accuracy:
- The accuracy of the DFT calculation depends on the precision of the WFT and VS measurements.
- Environmental factors such as temperature and humidity can also affect the drying process and, consequently, the final DFT.
-
Industry Standards:
- Many industries have specific standards for coating thickness, which are often based on the DFT.
- Understanding and applying this formula ensures that coatings meet these standards, providing the necessary protection and performance.
By using this formula, you can ensure that your coating application meets the required thickness specifications, which is critical for the longevity and effectiveness of the coating.
Summary Table:
Term | Definition |
---|---|
WFT | Wet Film Thickness: Thickness of the coating immediately after application. |
VS | Volume Solids: Percentage of the coating that remains as a solid film after drying. |
DFT | Dry Film Thickness: Final thickness of the coating after drying. |
Formula | DFT = WFT × VS / 100 |
Example | WFT = 150 microns, VS = 60% → DFT = 90 microns |
Need help with coating thickness calculations? Contact our experts today for tailored solutions!