Sieving is a fundamental process in chemistry and industrial applications, playing a critical role in ensuring the quality, consistency, and performance of materials. It involves separating particles based on their size, which is essential for analyzing raw materials, additives, and other supplies. By achieving accurate particle size distribution, sieving ensures that chemical reactions proceed efficiently, products meet quality standards, and processes remain reproducible. This process is particularly important in industries such as pharmaceuticals, food production, and materials science, where particle size directly impacts the final product's properties. Below, we explore the importance of sieving in chemistry in greater detail.
Key Points Explained:
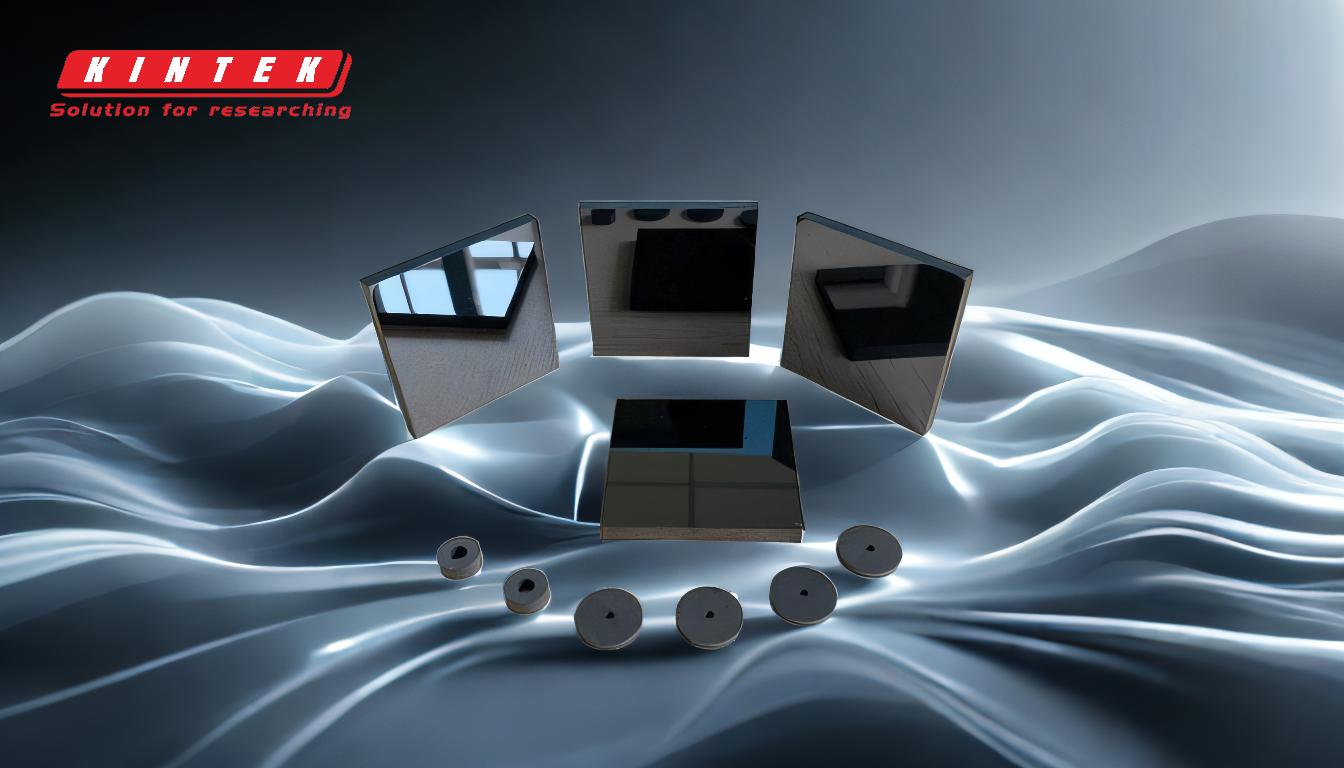
-
Ensuring Material Consistency and Quality
- Sieving helps achieve uniform particle size distribution, which is critical for consistent chemical reactions and product quality.
- Inconsistent particle sizes can lead to uneven mixing, incomplete reactions, or variations in product performance.
- For example, in pharmaceutical manufacturing, sieving ensures that active ingredients are evenly distributed in tablets, ensuring consistent dosage and efficacy.
-
Facilitating Efficient Chemical Reactions
- Particle size directly affects the surface area available for reactions. Smaller particles have a larger surface area, which can enhance reaction rates.
- Sieving ensures that reactants are of the appropriate size, optimizing reaction conditions and improving process efficiency.
- This is particularly important in catalysis, where the size of catalyst particles can significantly influence reaction kinetics.
-
Supporting Quality Control and Compliance
- Sieving is a key step in quality control processes, ensuring that materials meet specified size standards.
- Regulatory bodies often require precise particle size distributions for certain products, such as pharmaceuticals or food additives.
- By using sieving machines, manufacturers can ensure compliance with industry standards and avoid costly rejections or recalls.
-
Improving Product Performance
- In many industries, the performance of a product is directly tied to its particle size.
- For example, in the production of paints and coatings, sieving ensures that pigments are finely dispersed, resulting in better color consistency and coverage.
- Similarly, in the food industry, sieving can improve the texture and mouthfeel of products like flour or powdered beverages.
-
Enhancing Process Reproducibility
- Sieving provides a standardized method for preparing materials, ensuring that processes are reproducible across batches.
- This is crucial for industries where consistency is paramount, such as in the production of advanced materials or specialty chemicals.
- By maintaining consistent particle sizes, manufacturers can reduce variability and improve overall process reliability.
-
Applications in Various Industries
- Pharmaceuticals: Sieving ensures uniform particle size for active pharmaceutical ingredients (APIs) and excipients, which is critical for drug efficacy and safety.
- Food Production: Sieving is used to remove impurities, ensure consistent texture, and improve product quality.
- Materials Science: Sieving helps in the production of powders, ceramics, and composites, where particle size affects mechanical and thermal properties.
- Environmental Chemistry: Sieving is used to analyze soil and sediment samples, providing insights into environmental conditions and contamination levels.
-
Types of Sieving Techniques
- Dry Sieving: Used for free-flowing materials that do not clump or stick together.
- Wet Sieving: Suitable for materials that require liquid to disperse particles effectively.
- Air Jet Sieving: Ideal for fine powders that are difficult to separate using traditional methods.
- Each technique has specific applications and advantages, depending on the material being processed and the desired outcome.
-
Role in Research and Development
- Sieving is a critical tool in R&D, enabling scientists to study the effects of particle size on material properties and performance.
- It helps in developing new formulations, optimizing processes, and scaling up production.
- For example, in nanotechnology, sieving is used to isolate nanoparticles with specific sizes for use in advanced applications.
In conclusion, sieving is a vital process in chemistry and industrial applications, ensuring material consistency, optimizing reactions, and supporting quality control. Its importance extends across various industries, from pharmaceuticals to food production, where it plays a key role in achieving high-quality, reproducible results. By understanding and leveraging the benefits of sieving, manufacturers and researchers can enhance product performance, comply with regulatory standards, and drive innovation in their respective fields.
Summary Table:
Key Benefits of Sieving | Applications |
---|---|
Ensures uniform particle size | Pharmaceuticals: Consistent dosage and efficacy in tablets |
Optimizes chemical reaction rates | Food Production: Improved texture and quality of products |
Supports regulatory compliance | Materials Science: Enhanced mechanical and thermal properties |
Improves product performance | Environmental Chemistry: Analysis of soil and sediment samples |
Enhances process reproducibility | Research & Development: Development of new formulations and scaling production |
Learn how sieving can improve your processes—contact us today for expert advice!