The industrial process of pyrolysis is a thermochemical decomposition of organic materials at elevated temperatures in the absence of oxygen. It involves several stages, including pre-treatment of the feedstock, heating in a reactor, and separation of the resulting products such as biochar, bio-oil, and syngas. The process is widely used for converting waste materials like biomass, plastics, and tires into valuable products such as fuels, chemicals, and soil amendments. Pyrolysis operates at temperatures ranging from 200°C to 900°C, depending on the feedstock and desired outputs. The process is energy-efficient and environmentally friendly, as it recycles waste and reduces reliance on fossil fuels.
Key Points Explained:
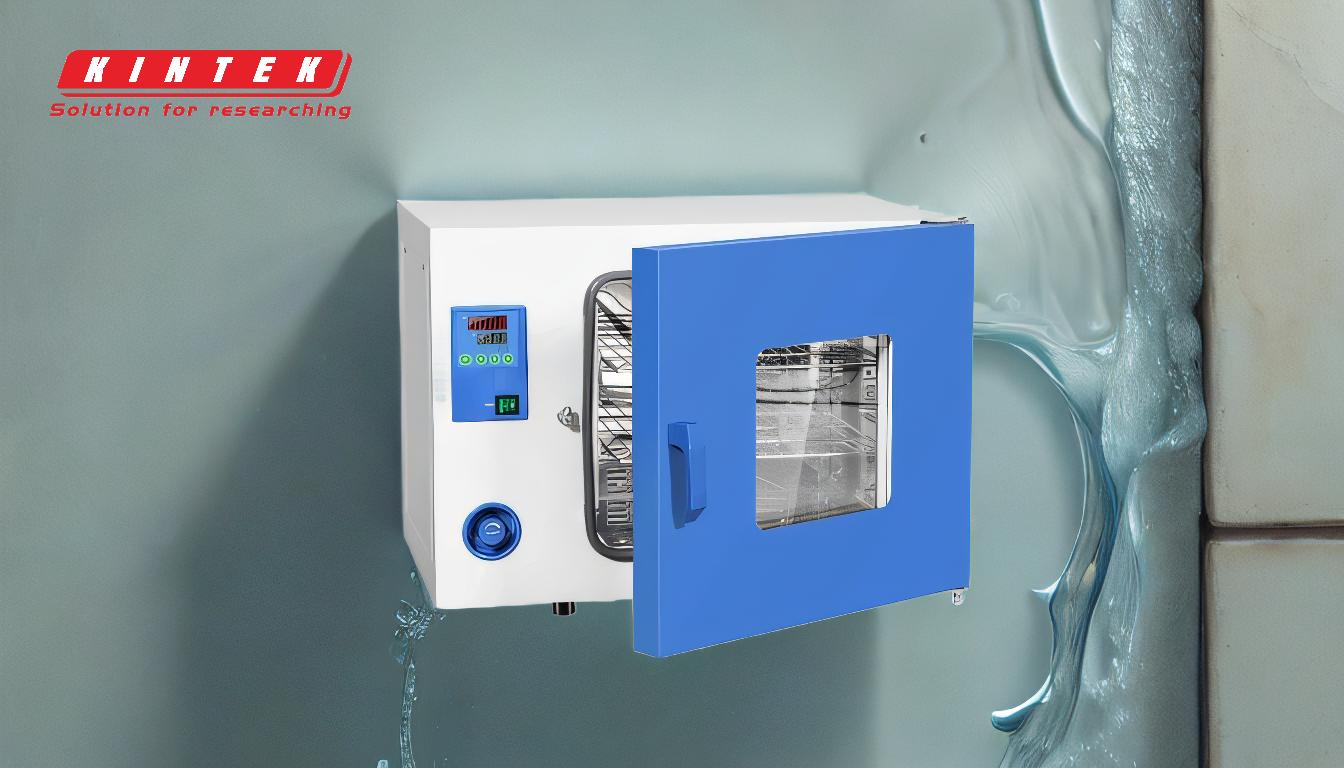
-
Feedstock Preparation:
- Pre-treatment: The feedstock, whether biomass, plastic, or tires, undergoes pre-treatment to remove impurities and ensure uniformity. This includes drying, grinding, and sizing the material to optimize the pyrolysis process.
- Importance: Proper pre-treatment ensures efficient decomposition and consistent product quality.
-
Pyrolysis Reactor:
- Heating Process: The prepared feedstock is fed into a pyrolysis reactor, where it is heated to temperatures between 200°C and 900°C in the absence of oxygen. This thermal decomposition breaks down the larger molecules into smaller components.
- Types of Reactors: Common reactor types include fixed-bed, fluidized-bed, and rotary kiln reactors, each suited for different feedstocks and scales of operation.
-
Product Separation:
- Biochar: Solid residue, known as biochar, settles at the bottom of the reactor. It can be used as a soil amendment or sorbent.
- Bio-oil: Vapors produced during pyrolysis are condensed into liquid bio-oil, which can be refined for use as fuel or in industrial applications.
- Syngas: Non-condensable gases, or syngas, are collected and can be recycled to provide heat for the pyrolysis process or used as a fuel.
-
Heat Supply and Control:
- Combustion Chamber: Heat is supplied via a combustion chamber, often using part of the syngas produced during pyrolysis.
- Temperature Control: Precise temperature control is crucial to optimize the yield and quality of the products. Advanced control systems ensure safe and efficient operation.
-
Environmental and Safety Considerations:
- Emission Control: Exhaust gases are treated to reduce harmful emissions, ensuring the process is environmentally friendly.
- Safety Systems: Modern pyrolysis plants are equipped with safety systems to handle high temperatures and pressures, preventing accidents and ensuring operator safety.
-
Applications of Pyrolysis Products:
- Biochar: Used in agriculture to improve soil health and as a carbon sequestration method.
- Bio-oil: Refined for use in transportation fuels, industrial chemicals, and as a renewable energy source.
- Syngas: Utilized as a fuel for heating or electricity generation, and as a feedstock for producing chemicals like methanol.
-
Recycling and Efficiency:
- Closed-loop System: Non-condensable syngas is often recycled back to the combustion chamber, enhancing the energy efficiency of the process.
- Waste Reduction: Pyrolysis effectively converts waste materials into valuable products, reducing landfill use and environmental pollution.
By following these steps, the industrial pyrolysis process efficiently converts waste materials into useful products, contributing to a circular economy and sustainable resource management.
Summary Table:
Stage | Description |
---|---|
Feedstock Preparation | Pre-treatment includes drying, grinding, and sizing to ensure uniformity. |
Pyrolysis Reactor | Heated to 200°C–900°C in the absence of oxygen; uses fixed-bed, fluidized-bed, or rotary kiln reactors. |
Product Separation | Produces biochar (soil amendment), bio-oil (fuel), and syngas (energy source). |
Heat Supply & Control | Uses syngas for heat; precise temperature control optimizes product yield. |
Environmental Safety | Emission control and safety systems ensure eco-friendly and safe operations. |
Applications | Biochar for soil health, bio-oil for fuels, and syngas for energy and chemicals. |
Recycling & Efficiency | Closed-loop system recycles syngas, reducing waste and enhancing efficiency. |
Discover how pyrolysis can transform waste into valuable resources—contact us today to learn more!