Diamond-like carbon (DLC) is a specialized coating material known for its unique combination of properties, including high hardness, low friction, and excellent wear resistance. It is a metastable form of amorphous carbon or hydrogenated amorphous carbon, containing a significant fraction of sp3 bonds, which are diamond-like, and sp2 bonds, which are graphite-like. The ratio of these bonds determines the material's properties, making it suitable for a wide range of applications, from automotive components to biomedical prostheses. DLC coatings are applied using physical vapor deposition (PVD) techniques and are valued for their ability to enhance the performance and longevity of various components.
Key Points Explained:
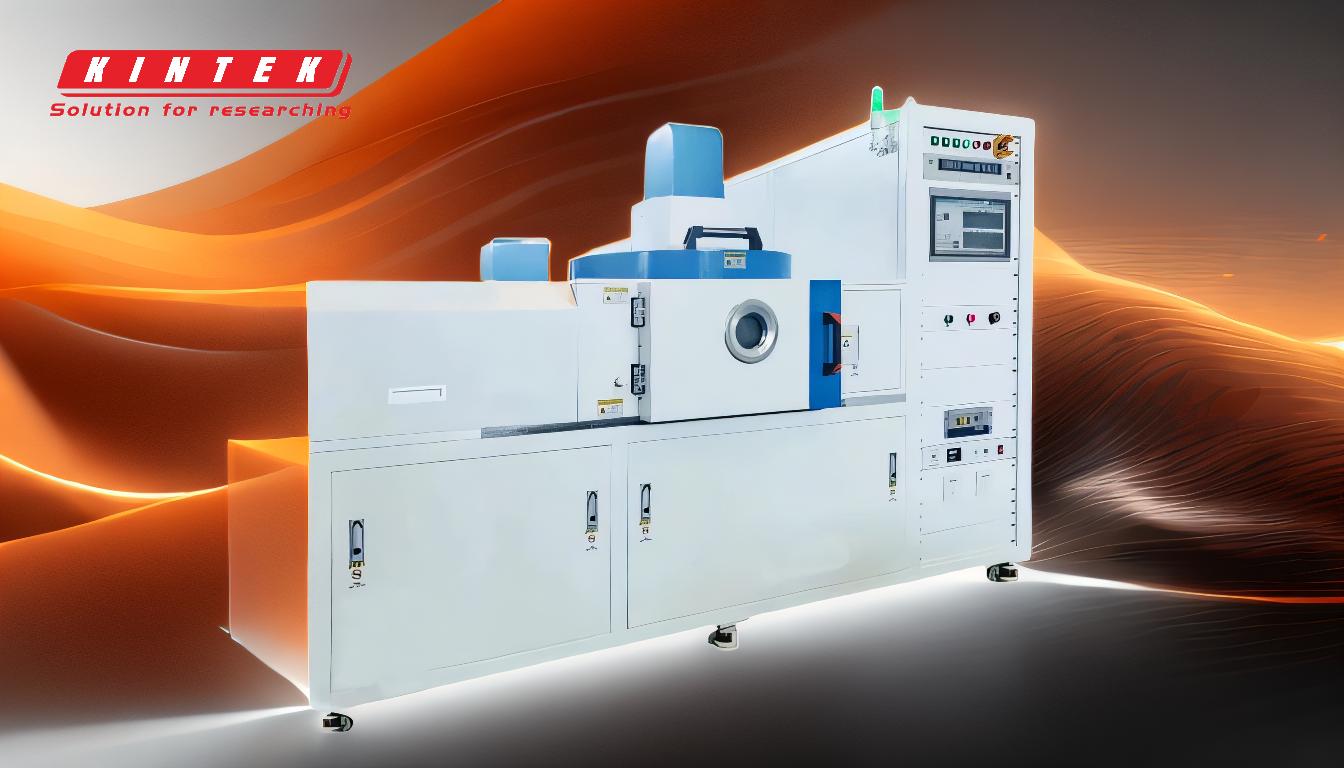
-
Composition of DLC:
- DLC is primarily composed of carbon atoms arranged in a metastable amorphous structure.
- It contains a mixture of sp3 (diamond-like) and sp2 (graphite-like) bonds. The sp3 bonds contribute to the material's hardness, while the sp2 bonds provide lubricity.
- The ratio of sp3 to sp2 bonds can be adjusted to tailor the properties of the DLC coating for specific applications.
-
Types of DLC:
- ta-C (Tetrahedral Amorphous Carbon): This form of DLC has a high fraction of sp3 bonds, making it extremely hard and suitable for high-wear applications.
- a-C (Amorphous Carbon): This is a more general form of DLC with a balanced mix of sp3 and sp2 bonds, offering a good combination of hardness and lubricity.
- H-terminated DLC: This type of DLC contains hydrogen, which can further reduce the coefficient of friction, making it ideal for applications requiring low friction.
-
Properties of DLC:
- High Hardness: DLC coatings typically have a hardness ranging from 1500 to 3000 HV, making them suitable for wear-resistant applications.
- Low Coefficient of Friction: The presence of sp2 bonds gives DLC a low friction coefficient, which is beneficial for sliding and moving parts.
- Corrosion Resistance: DLC coatings perform well in corrosive environments, making them suitable for use in harsh conditions.
- Biocompatibility: DLC is used in biomedical applications, such as prostheses, due to its biocompatibility and wear resistance.
-
Applications of DLC:
- Automotive Industry: DLC coatings are used in power trains, bearings, camshafts, and other components to reduce friction and wear, thereby improving energy efficiency and longevity.
- Machinery: DLC is applied to machine parts that require high wear resistance and low friction, such as gears and bearings.
- Optical Components: DLC coatings are used on optical components to protect against wear and reduce friction.
- Magnetic Memory Discs: DLC is used to protect magnetic memory discs from wear and corrosion.
- Biomedical Prostheses: The biocompatibility and wear resistance of DLC make it suitable for use in biomedical prostheses.
- Watches and Jewelry: DLC coatings are used on watches to enhance their functional properties while maintaining a luxurious appearance.
-
Deposition Techniques:
- DLC coatings are typically applied using Physical Vapor Deposition (PVD) techniques. PVD allows for precise control over the coating's thickness and properties, making it suitable for a wide range of applications.
- The PVD process involves vaporizing the carbon source material in a vacuum and depositing it onto the substrate, forming a thin, uniform coating.
-
Advantages of DLC:
- Enhanced Performance: DLC coatings significantly improve the performance of components by reducing wear and friction.
- Extended Lifespan: Components coated with DLC have a longer service life due to the material's wear resistance.
- Versatility: DLC can be tailored to meet the specific requirements of different industries, making it a versatile coating material.
In summary, Diamond-like carbon (DLC) is a highly versatile and valuable material used in various industries due to its unique combination of hardness, low friction, and wear resistance. Its composition, which includes a mix of sp3 and sp2 bonds, allows for customization to meet specific application needs. DLC coatings are applied using PVD techniques and are used in automotive, machinery, optical, and biomedical applications, among others. The material's properties make it an excellent choice for enhancing the performance and longevity of components in demanding environments.
Summary Table:
Aspect | Details |
---|---|
Composition | Mixture of sp3 (diamond-like) and sp2 (graphite-like) bonds. |
Types | ta-C (high sp3), a-C (balanced sp3/sp2), H-terminated (low friction). |
Properties | High hardness (1500-3000 HV), low friction, corrosion resistance. |
Applications | Automotive, machinery, optical components, biomedical prostheses, jewelry. |
Deposition Technique | Physical Vapor Deposition (PVD). |
Advantages | Enhanced performance, extended lifespan, versatility. |
Unlock the potential of DLC coatings for your industry—contact us today to learn more!