The moisture content of pyrolysis oil typically ranges between 20-30% by weight, as it is composed of a complex mixture of oxygenated hydrocarbons and water. This high moisture content, combined with its high oxygen content (up to 40% by weight), contributes to its unique properties such as low heating value, poor volatility, and high viscosity. Pyrolysis oil is also thermally unstable, corrosive, and prone to polymerization, which limits its direct use as a fuel without further refining or upgrading. The moisture content and other properties can vary depending on the feedstock and pyrolysis conditions, but the water content remains a defining characteristic of pyrolysis oil.
Key Points Explained:
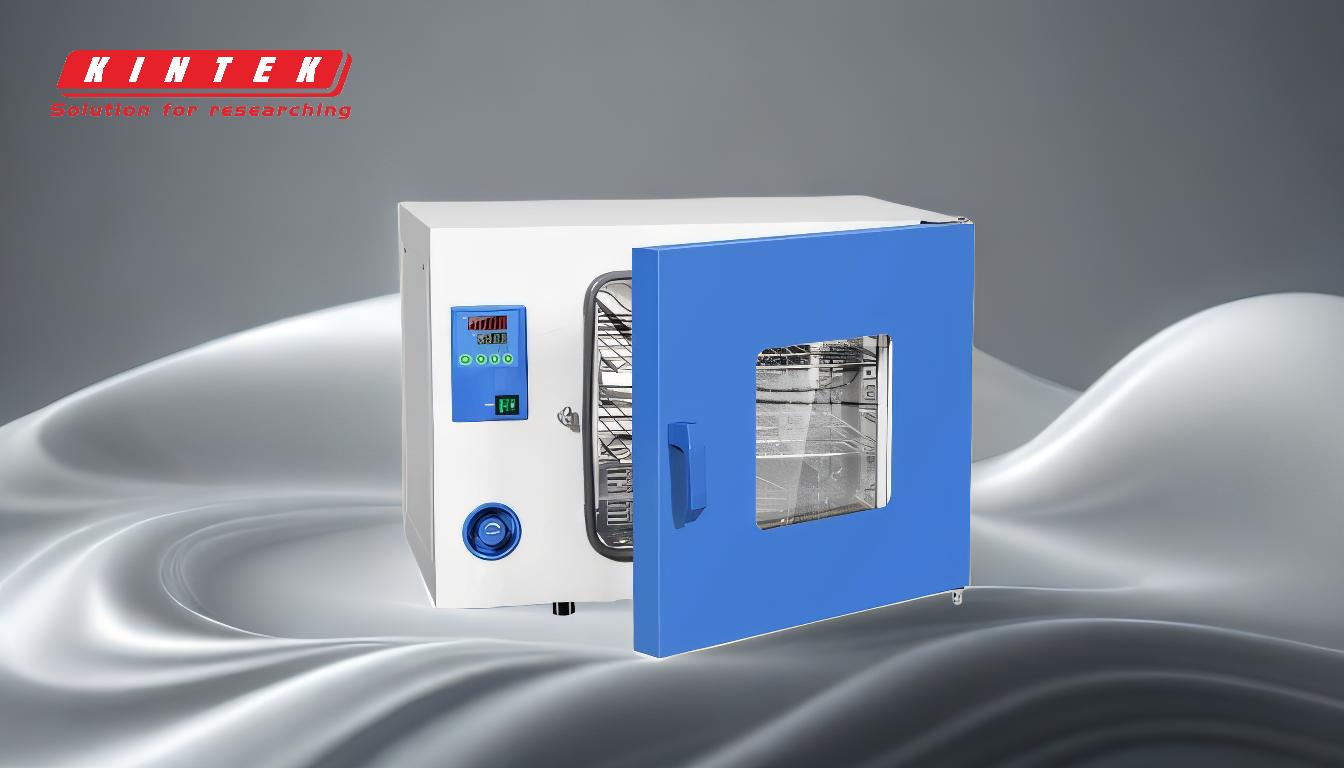
-
Moisture Content of Pyrolysis Oil:
- Pyrolysis oil contains a significant proportion of water, typically between 20-30% by weight. This high moisture content is a result of the pyrolysis process, which breaks down biomass into a mixture of oxygenated hydrocarbons and water.
- The presence of water affects the oil's properties, including its energy density, viscosity, and stability.
-
Impact of Moisture on Pyrolysis Oil Properties:
- Low Heating Value: The high moisture content reduces the energy density of pyrolysis oil, resulting in a lower heating value compared to conventional fossil fuels.
- High Viscosity: Water contributes to the oil's high viscosity, making it less fluid and harder to handle.
- Thermal Instability: The presence of water, along with oxygenated compounds, makes pyrolysis oil thermally unstable, leading to polymerization and increased viscosity over time.
-
Composition and Characteristics:
- Pyrolysis oil is a complex mixture of oxygenated organic compounds, polymers, and water. It contains up to 40% oxygen by weight, which makes it highly reactive and corrosive.
- The oil includes a wide range of chemicals, from low molecular weight compounds (e.g., formaldehyde, acetic acid) to high molecular weight compounds (e.g., phenols, anhydrosugars, oligosaccharides).
-
Applications and Limitations:
- Pyrolysis oil is primarily used as a fuel in boilers and furnaces, but its high moisture content and instability limit its direct use in engines or turbines.
- It can be refined into diesel or other fuels using distillation or catalytic upgrading processes, which reduce moisture and improve stability.
-
Standards and Quality Control:
- There are few established standards for pyrolysis oil due to its limited production and variability. However, ASTM provides some guidelines for its characterization and use.
- The quality of pyrolysis oil can be improved by using catalysts during the pyrolysis process, which can reduce moisture content and enhance stability.
-
Comparison to Fossil Fuels:
- Pyrolysis oil has a viscosity and heating value similar to diesel fuel, but it has a higher sulfur content and a lower flashpoint.
- Its high moisture and oxygen content make it immiscible with fossil fuels, limiting its direct blending or substitution in existing fuel systems.
-
Handling and Storage Considerations:
- Due to its corrosive nature and high moisture content, pyrolysis oil requires specialized storage and handling equipment to prevent degradation and safety hazards.
- The oil's instability over time necessitates careful management to avoid issues like increased viscosity or polymerization.
By understanding the moisture content and its effects on pyrolysis oil, purchasers can make informed decisions about its use, storage, and potential upgrading for specific applications.
Summary Table:
Aspect | Details |
---|---|
Moisture Content | 20-30% by weight |
Oxygen Content | Up to 40% by weight |
Key Properties | Low heating value, high viscosity, thermal instability, and corrosiveness |
Applications | Primarily used in boilers and furnaces; requires refining for engine use |
Storage Requirements | Specialized equipment to prevent degradation and safety hazards |
Discover how pyrolysis oil can meet your energy needs—contact our experts today for tailored solutions!