Semiconductors are integral to modern electronics, and the most commonly used materials and equipment in their manufacturing are silicon wafers, photolithography tools, and chemical vapor deposition (CVD) systems. Silicon is the primary material due to its abundance, stability, and excellent semiconductor properties. Photolithography tools are essential for patterning circuits on silicon wafers, while CVD systems are used to deposit thin films of materials necessary for creating semiconductor layers. These components and tools form the backbone of semiconductor fabrication, enabling the production of devices like microprocessors, memory chips, and sensors.
Key Points Explained:
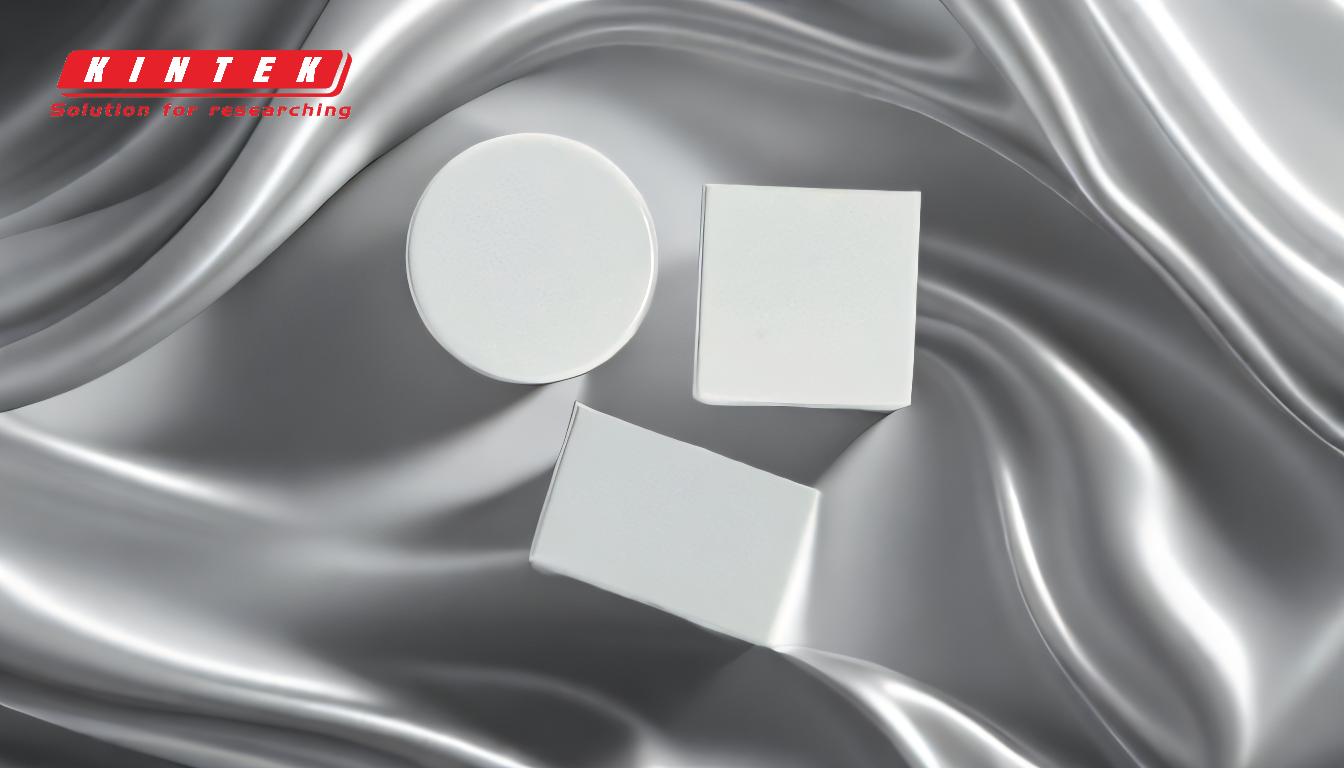
-
Silicon Wafers
- Silicon is the most widely used material in semiconductor manufacturing due to its ideal properties, such as high thermal stability, abundance, and ability to form a natural oxide layer (SiO₂).
- Silicon wafers serve as the substrate for building integrated circuits (ICs). They are sliced from single-crystal silicon ingots and polished to a mirror-like finish.
- The purity of silicon wafers is critical, as even minor impurities can disrupt the electrical properties of the semiconductor.
-
Photolithography Tools
- Photolithography is a key process in semiconductor fabrication, used to transfer circuit patterns onto silicon wafers.
- This process involves coating the wafer with a light-sensitive material called photoresist, exposing it to ultraviolet (UV) light through a photomask, and then developing the pattern.
- Advanced photolithography tools, such as extreme ultraviolet (EUV) lithography systems, are essential for creating smaller and more complex circuit patterns required for modern chips.
-
Chemical Vapor Deposition (CVD) Systems
- CVD systems are used to deposit thin films of materials, such as silicon dioxide, silicon nitride, and metals, onto silicon wafers.
- These films are critical for creating insulating layers, conductive pathways, and protective coatings in semiconductor devices.
- CVD processes are highly controlled to ensure uniform film thickness and quality, which are essential for device performance.
-
Other Commonly Used Equipment and Materials
- Etching Tools: Used to remove material from the wafer surface to create the desired patterns. Wet etching and dry etching (e.g., plasma etching) are common methods.
- Ion Implantation Equipment: Used to introduce dopants into the silicon wafer to modify its electrical properties.
- Metallization Tools: Used to deposit metal layers, such as aluminum or copper, to form interconnects between different parts of the circuit.
- Cleaning and Polishing Systems: Essential for maintaining wafer cleanliness and surface quality throughout the fabrication process.
-
Importance of Precision and Cleanliness
- Semiconductor manufacturing requires an ultra-clean environment, as even microscopic contaminants can cause defects in the final product.
- Cleanrooms with controlled temperature, humidity, and particulate levels are standard in semiconductor fabrication facilities (fabs).
- Precision in every step, from wafer preparation to final packaging, is critical to ensure the performance and reliability of semiconductor devices.
-
Emerging Trends and Alternatives
- While silicon remains dominant, alternative materials like gallium nitride (GaN) and silicon carbide (SiC) are gaining traction for specialized applications, such as high-power and high-frequency devices.
- Advanced packaging techniques, such as 3D chip stacking, are being adopted to meet the demands of increasingly complex and miniaturized electronics.
In summary, silicon wafers, photolithography tools, and CVD systems are the most commonly used components and equipment in semiconductor manufacturing. These elements, along with other critical tools and processes, enable the production of the advanced electronic devices that power modern technology.
Summary Table:
Component/Equipment | Key Role |
---|---|
Silicon Wafers | Serve as the substrate for integrated circuits; high purity is critical. |
Photolithography Tools | Transfer circuit patterns onto wafers using UV light and photoresist. |
CVD Systems | Deposit thin films for insulating layers, conductive pathways, and coatings. |
Etching Tools | Remove material to create patterns on wafers. |
Ion Implantation Equipment | Introduce dopants to modify electrical properties. |
Metallization Tools | Deposit metal layers for interconnects. |
Cleaning Systems | Maintain wafer cleanliness and surface quality. |
Interested in semiconductor manufacturing solutions? Contact us today to learn more!