A sieve shaker is a device used to separate particles by size through vibration or mechanical agitation. Its operating procedure involves setting up the sieve stack, loading the sample, activating the shaker, and analyzing the results. The vibration motor or mechanical system drives the sieves, causing particles smaller than the sieve openings to pass through, while larger particles remain on top. This process ensures accurate particle size distribution analysis, improves efficiency, and complies with industry standards. Below is a detailed explanation of the operating procedure and key points to consider.
Key Points Explained:
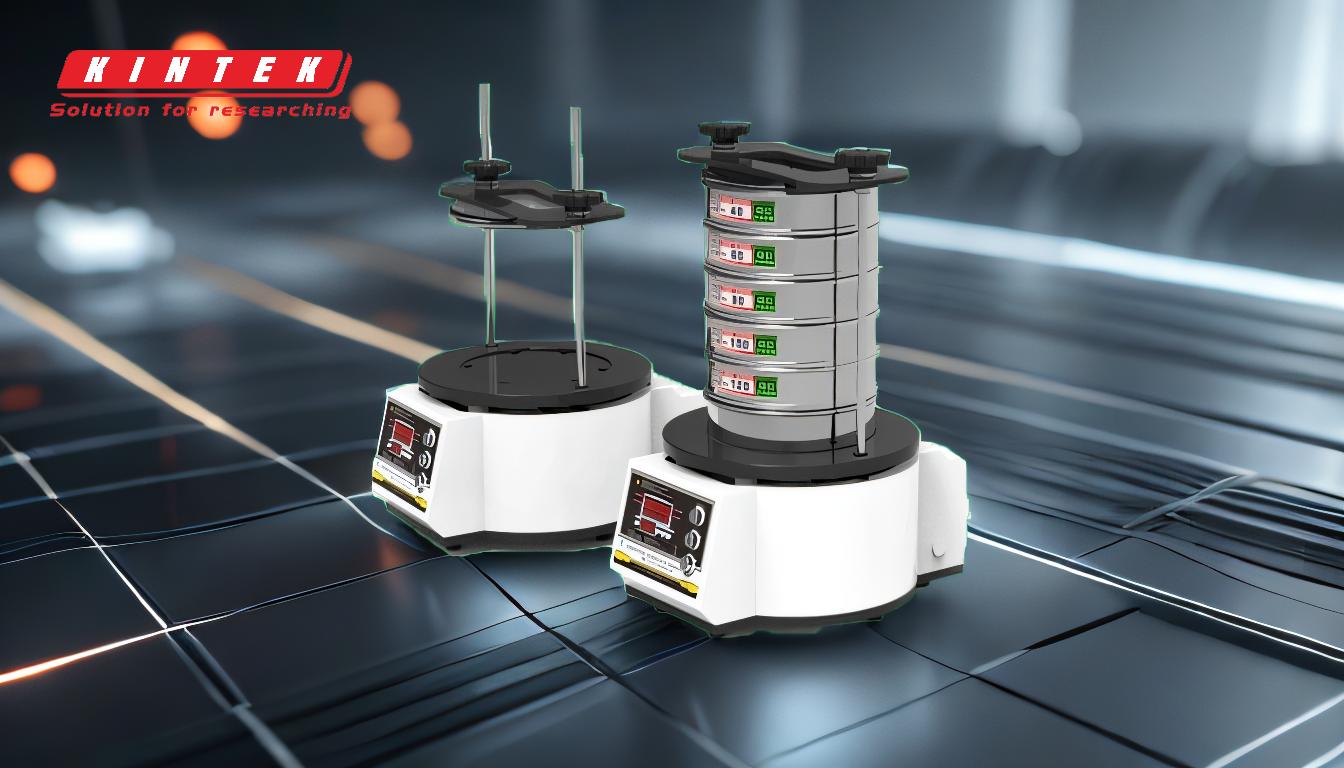
-
Preparation of the Sieve Stack:
- Assemble the sieve stack in descending order of mesh size, with the finest sieve at the bottom and the coarsest at the top.
- Ensure each sieve is securely fastened to prevent movement during operation.
- Place a collection pan or receiver at the bottom to catch particles that pass through the finest sieve.
-
Loading the Sample:
- Weigh the sample accurately to ensure consistency in analysis.
- Distribute the sample evenly across the top sieve to avoid overloading, which can lead to inaccurate results.
- Close the sieve stack with a lid to prevent sample loss during shaking.
-
Activating the Sieve Shaker:
- Place the assembled sieve stack onto the shaker platform.
- Secure the stack using clamps or fasteners to ensure stability.
- Set the desired vibration intensity, duration, and mode (e.g., oscillating, tapping, or agitation) based on the material and analysis requirements.
- Start the shaker and allow it to run for the predetermined time, ensuring consistent and thorough particle separation.
-
Analyzing the Results:
- After the shaking process is complete, carefully disassemble the sieve stack.
- Weigh the material retained on each sieve and the collection pan to determine the particle size distribution.
- Record the data and calculate the percentage of material in each size fraction.
- Clean the sieves thoroughly after use to prevent cross-contamination in future tests.
-
Key Considerations for Optimal Operation:
- Vibration Source: The YZU vertical vibration motor or similar systems ensure consistent and efficient particle separation.
- Sieve Selection: Use sieves with appropriate mesh sizes for the material being tested to achieve accurate results.
- Sample Size: Avoid overloading the sieves, as this can hinder particle movement and reduce accuracy.
- Shaking Time: Adjust the duration based on the material's characteristics to ensure complete separation.
- Maintenance: Regularly inspect and maintain the sieve shaker to ensure consistent performance and longevity.
By following these steps and considerations, the sieve shaker can effectively separate particles by size, providing reliable data for material analysis. This process not only improves efficiency but also ensures compliance with industry standards, making it an essential tool for particle size determination.
Summary Table:
Step | Key Actions | Purpose |
---|---|---|
Preparation | Assemble sieve stack, secure sieves, place collection pan | Ensure proper setup for accurate particle separation |
Loading | Weigh sample, distribute evenly, close with lid | Prevent overloading and sample loss |
Activation | Set vibration intensity, duration, and mode; secure stack; start shaker | Achieve consistent and thorough particle separation |
Analysis | Weigh retained material, calculate size distribution, clean sieves | Determine particle size distribution and ensure future test accuracy |
Key Considerations | Use proper vibration source, sieve selection, sample size, shaking time, maintenance | Optimize performance and ensure compliance with industry standards |
Ready to enhance your particle size analysis? Contact us today for expert guidance on sieve shakers!