Cold isostatic pressing (CIP) is a powder compaction process that applies uniform pressure from all directions using a liquid medium, typically water-based, at ambient temperatures. The pressure range for CIP varies significantly depending on the material being processed, the desired density, and the part geometry. Generally, the pressure ranges from 20 MPa to 400 MPa, with some applications requiring pressures as low as 34.5 MPa (5,000 psi) or as high as 690 MPa (100,000 psi). The process involves placing a powder-filled elastomeric mold into a pressure chamber, filling it with a liquid, and applying pressure uniformly to achieve compaction. The resulting green body is then retrieved after the pressure is released. Key factors influencing the pressure include material properties, part dimensions, and the desired final density.
Key Points Explained:
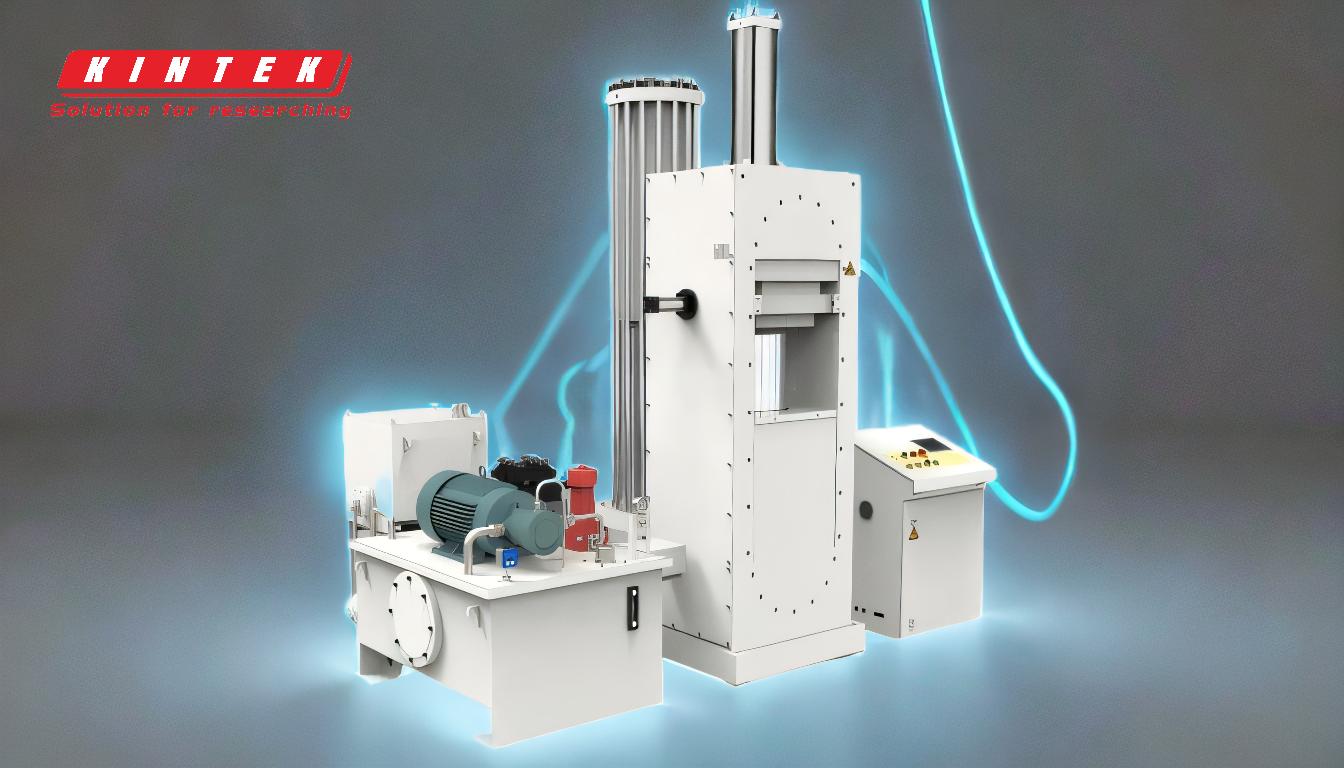
-
Pressure Range in Cold Isostatic Pressing (CIP):
- The pressure applied in CIP typically ranges from 20 MPa to 400 MPa, with some references indicating a broader range of 34.5 MPa to 690 MPa (5,000 psi to 100,000 psi).
- This wide range is due to variations in material properties, part geometry, and the desired density of the final product.
-
Uniform Pressure Application:
- CIP applies pressure uniformly from all directions using a liquid medium, usually water with a corrosion inhibitor.
- This uniform pressure ensures even compaction of the powder, leading to a homogeneous green body with minimal internal stresses.
-
Process Mechanics:
- The powder is placed in an elastomeric mold or container, which is then submerged in the liquid medium within a pressure chamber.
- An external pump pressurizes the liquid, and the chamber is designed to withstand cyclic loading and fatigue failure.
-
Material and Part Geometry Influence:
- The maximum operating pressure required depends on the material being processed and the part geometry.
- For example, denser materials or larger parts may require higher pressures to achieve the desired compaction.
-
Chamber Capacity and Size:
- The capacity of the pressure chamber is determined by its diameter and height, which dictate the maximum dimensions of parts that can be processed.
- Larger chambers can accommodate bigger parts but may require higher pressures for effective compaction.
-
Comparison with Warm Isostatic Pressing:
- In contrast to CIP, warm isostatic pressing (WIP) typically operates at higher pressures, around 300 MPa, and involves elevated temperatures to aid in compaction and sintering.
-
Advantages of CIP:
- CIP allows for the production of complex shapes with uniform density and minimal defects.
- It is particularly useful for materials that are difficult to compact using traditional methods, such as ceramics and certain metals.
-
Applications:
- CIP is widely used in industries such as aerospace, automotive, and medical for producing high-performance components with precise tolerances and uniform properties.
-
Post-Processing:
- After compaction, the liquid is removed, and the elastomeric container returns to its original shape, allowing the green body to be retrieved for further processing, such as sintering.
-
Customization Based on Requirements:
- The pressure and other parameters can be customized based on the specific requirements of the material and the part, ensuring optimal results for each application.
In summary, the pressure used in cold isostatic pressing is highly variable and depends on several factors, including the material, part geometry, and desired density. The process offers significant advantages in terms of uniformity and the ability to produce complex shapes, making it a valuable technique in various high-tech industries.
Summary Table:
Key Aspect | Details |
---|---|
Pressure Range | 20 MPa to 400 MPa (up to 690 MPa in some cases) |
Uniform Pressure | Applied from all directions using a liquid medium (water-based) |
Process Mechanics | Powder-filled elastomeric mold submerged in a pressure chamber |
Material Influence | Pressure depends on material properties, part geometry, and desired density |
Chamber Capacity | Determined by diameter and height, accommodating larger parts |
Advantages | Produces complex shapes with uniform density and minimal defects |
Applications | Aerospace, automotive, and medical industries |
Post-Processing | Green body retrieved for sintering or further processing |
Learn how CIP can enhance your manufacturing process—contact our experts today!