Preventive maintenance of a ball mill involves a series of routine checks, inspections, and actions aimed at ensuring the equipment operates efficiently and reliably over its lifespan. This includes regular lubrication of moving parts, inspection of wear components like liners and grinding media, monitoring of motor and drive systems, and ensuring proper alignment and balance. Additionally, preventive maintenance involves cleaning the mill, checking for leaks, and verifying the integrity of seals and bearings. By adhering to a structured maintenance schedule, potential issues can be identified and addressed before they lead to costly downtime or equipment failure.
Key Points Explained:
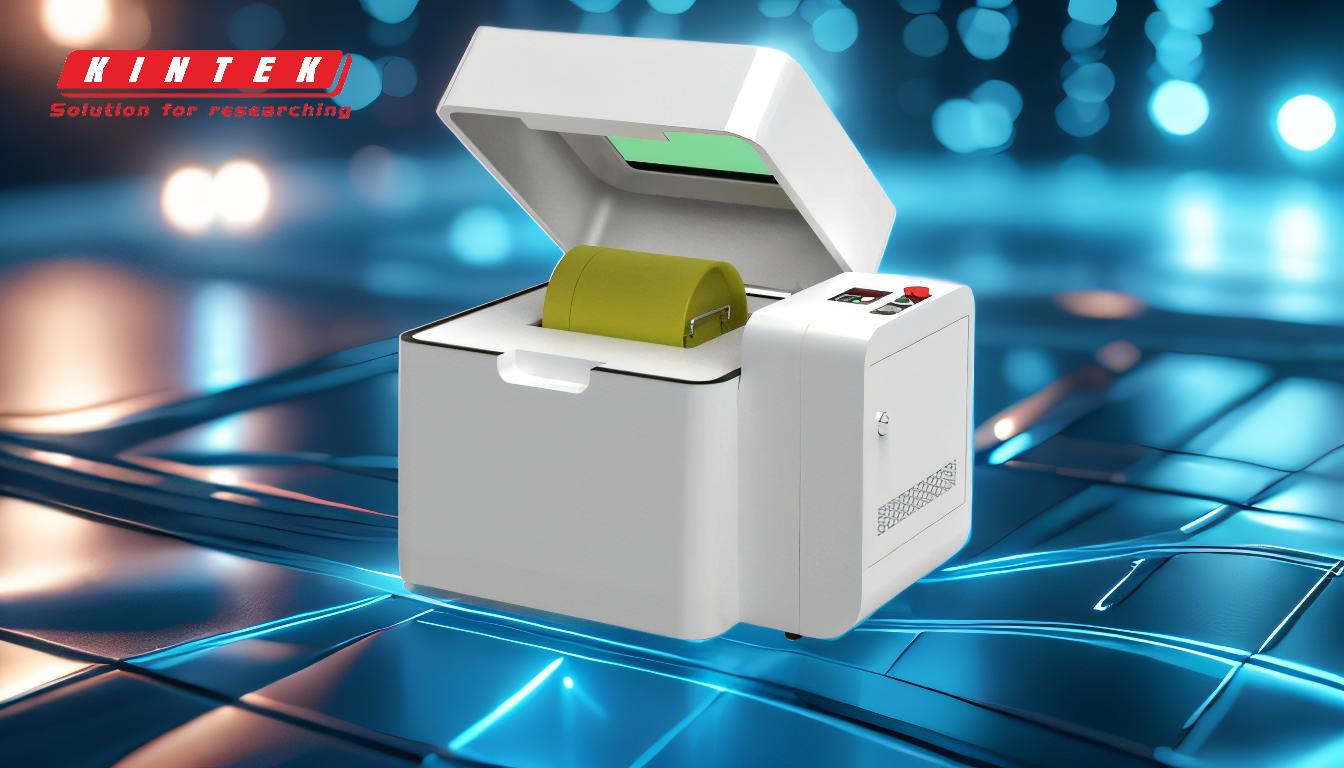
-
Lubrication of Moving Parts
- Regular lubrication is critical for reducing friction and wear on moving components such as bearings, gears, and trunnions.
- Use the correct type and amount of lubricant as specified by the manufacturer.
- Monitor oil levels and quality to ensure optimal performance.
-
Inspection of Wear Components
- Regularly inspect the mill liners, grinding media, and other wear-prone parts for signs of wear or damage.
- Replace worn-out liners and grinding balls to maintain grinding efficiency and prevent damage to the mill shell.
- Keep a record of wear rates to predict replacement intervals.
-
Monitoring Motor and Drive Systems
- Check the motor and drive systems for proper alignment, vibration, and temperature.
- Ensure that belts, couplings, and gears are in good condition and properly tensioned.
- Address any unusual noises or vibrations immediately to prevent further damage.
-
Alignment and Balance Checks
- Verify that the mill is properly aligned and balanced to avoid excessive vibration and uneven wear.
- Misalignment can lead to premature failure of bearings and other components.
-
Cleaning and Leak Inspection
- Regularly clean the mill to remove buildup of material that can affect performance.
- Inspect for leaks in the lubrication system or seals, which can lead to contamination or insufficient lubrication.
-
Seal and Bearing Integrity
- Inspect seals and bearings for signs of wear, damage, or contamination.
- Replace faulty seals and bearings promptly to prevent leaks and ensure smooth operation.
-
Scheduled Maintenance Plan
- Develop and adhere to a preventive maintenance schedule based on the manufacturer’s recommendations and operational conditions.
- Document all maintenance activities to track the condition of the mill and identify recurring issues.
-
Training and Safety
- Ensure that maintenance personnel are properly trained and follow safety protocols.
- Use appropriate personal protective equipment (PPE) when performing maintenance tasks.
By following these preventive maintenance practices, the ball mill can operate efficiently, reduce downtime, and extend its service life.
Summary Table:
Key Maintenance Task | Details |
---|---|
Lubrication of Moving Parts | Regular lubrication reduces friction; monitor oil levels and quality. |
Inspection of Wear Components | Check liners, grinding media, and wear-prone parts; replace as needed. |
Monitoring Motor and Drive Systems | Ensure alignment, check belts, couplings, and gears; address vibrations. |
Alignment and Balance Checks | Verify proper alignment to prevent uneven wear and premature failure. |
Cleaning and Leak Inspection | Clean the mill regularly; inspect for leaks in seals and lubrication systems. |
Seal and Bearing Integrity | Inspect and replace faulty seals and bearings to ensure smooth operation. |
Scheduled Maintenance Plan | Follow a structured schedule; document all activities for tracking. |
Training and Safety | Train personnel; use PPE and follow safety protocols during maintenance. |
Optimize your ball mill's performance—contact our experts today for a tailored maintenance plan!