A colloidal mill in pharmaceutical engineering operates on the rotor-stator principle, where a rapidly rotating cone (rotor) and a static cone (stator) create a small gap. This gap generates high shear forces that break down solid materials into fine particles, dispersing them into a liquid medium. The mill is particularly effective for comminution, emulsification, homogenization, and dispersion of materials, especially those with solids not easily moistened by the dispersion medium. Its design ensures precision, low maintenance, and compliance with pharmaceutical standards, making it a versatile tool for creating suspensions and achieving superfine grinding results.
Key Points Explained:
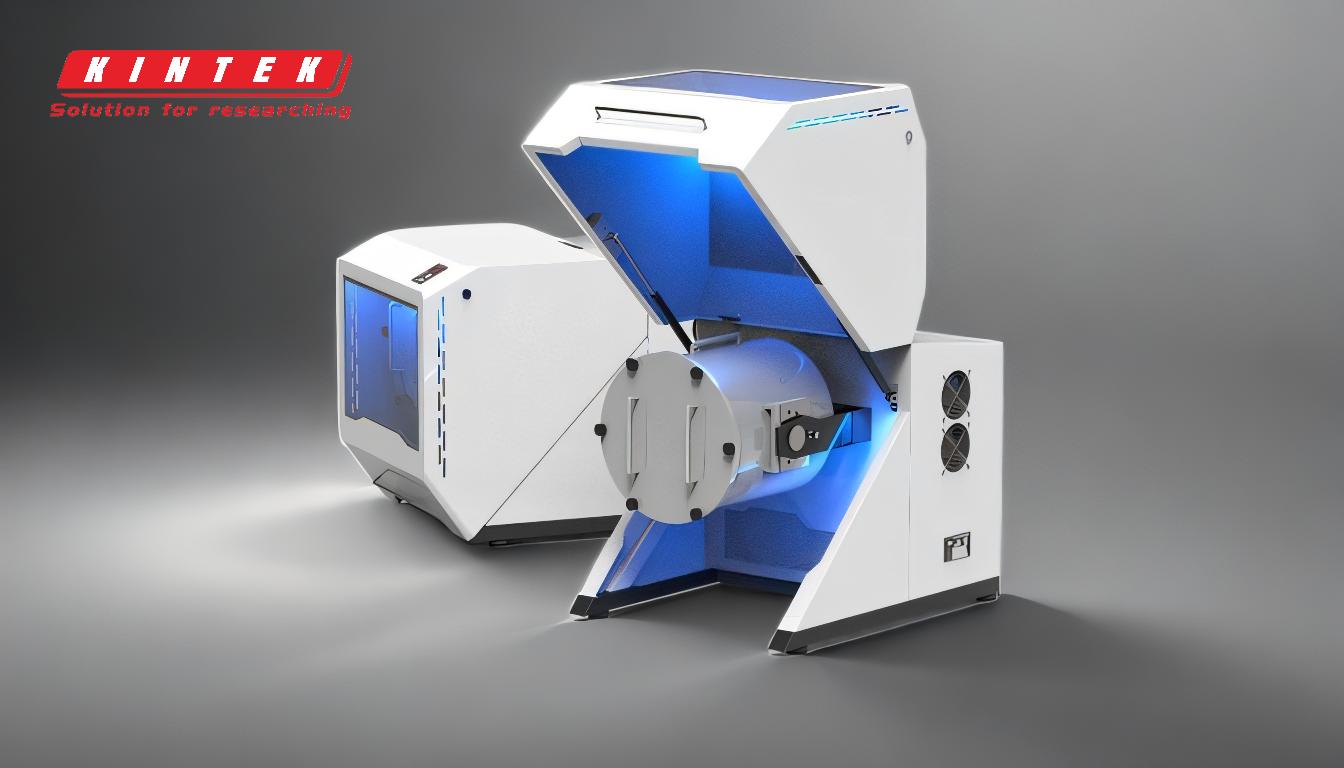
-
Rotor-Stator Principle:
- The colloidal mill operates using a rotor-stator mechanism. The rotor is a rapidly rotating cone, while the stator is a static cone. The small gap between them generates high shear forces.
- This principle is crucial for breaking down solid materials into fine particles and dispersing them uniformly in a liquid medium.
-
Shearing Mechanism:
- The high shear forces created in the gap between the rotor and stator are responsible for the comminution (size reduction) of solid materials.
- This mechanism is particularly effective for materials that are not easily moistened by the dispersion medium, ensuring a uniform suspension.
-
Applications in Pharmaceutical Engineering:
- Comminution: Reducing solid particles to a fine size, which is essential for creating uniform suspensions.
- Emulsification: Creating stable emulsions by dispersing one liquid into another.
- Homogenization: Ensuring a uniform mixture of different components.
- Dispersion: Evenly distributing solid particles in a liquid medium.
-
Simultaneous Processes:
- The colloidal mill can perform multiple processes like grinding, emulsifying, homogenizing, and dispersing in a single cycle.
- This multifunctionality makes it highly efficient and time-saving in pharmaceutical applications.
-
Design and Features:
- Compact and Low Maintenance: The mill is designed to be compact with a small footprint, making it easy to use and maintain.
- cGMP Compliance: Ensures that the mill meets the stringent standards required in pharmaceutical manufacturing.
- Material Construction: All contact parts are made from Stainless Steel 316, with moving parts covered in Stainless Steel 304, ensuring durability and hygiene.
- Food-Grade Seals: Prevent contamination, which is critical in pharmaceutical applications.
- Adjustable Gap: The gap between the rotor and stator can be easily adjusted to achieve the desired particle size.
- Mobility: Equipped with castor wheels for easy movement and optional overload pressure release mechanisms for safety.
-
Versatility:
- The colloidal mill is versatile and can handle highly viscous materials, making it suitable for a wide range of pharmaceutical applications.
- Its ability to achieve superfine grinding results along with simultaneous emulsifying, homogenizing, and dispersing makes it a valuable tool in the pharmaceutical industry.
By understanding these key points, a pharmaceutical equipment purchaser can appreciate the efficiency, versatility, and compliance of the colloidal mill, making it an essential piece of equipment for various pharmaceutical processes.
Summary Table:
Key Feature | Description |
---|---|
Rotor-Stator Principle | High shear forces break down solids into fine particles for uniform dispersion. |
Shearing Mechanism | Effective for materials not easily moistened by the dispersion medium. |
Applications | Comminution, emulsification, homogenization, and dispersion. |
Simultaneous Processes | Grinding, emulsifying, homogenizing, and dispersing in a single cycle. |
Design & Features | Compact, low maintenance, cGMP compliant, adjustable gap, and mobile. |
Versatility | Handles highly viscous materials and achieves superfine grinding results. |
Discover how a colloidal mill can optimize your pharmaceutical processes—contact us today!