Magnetron sputtering is a physical vapor deposition (PVD) technique used to deposit thin films onto substrates. The process involves creating a plasma in a high-vacuum environment, where argon gas is ionized by applying a high negative voltage between a cathode (target material) and an anode. Positive argon ions are accelerated toward the negatively charged target, causing atoms to be ejected from the target surface. These ejected atoms then travel in a line-of-sight trajectory and condense on the substrate to form a thin film. A magnetic field is used to confine electrons near the target surface, increasing plasma density and deposition efficiency while protecting the substrate from ion bombardment. This method is widely used for producing high-quality, uniform coatings in industries such as semiconductors, optics, and decorative coatings.
Key Points Explained:
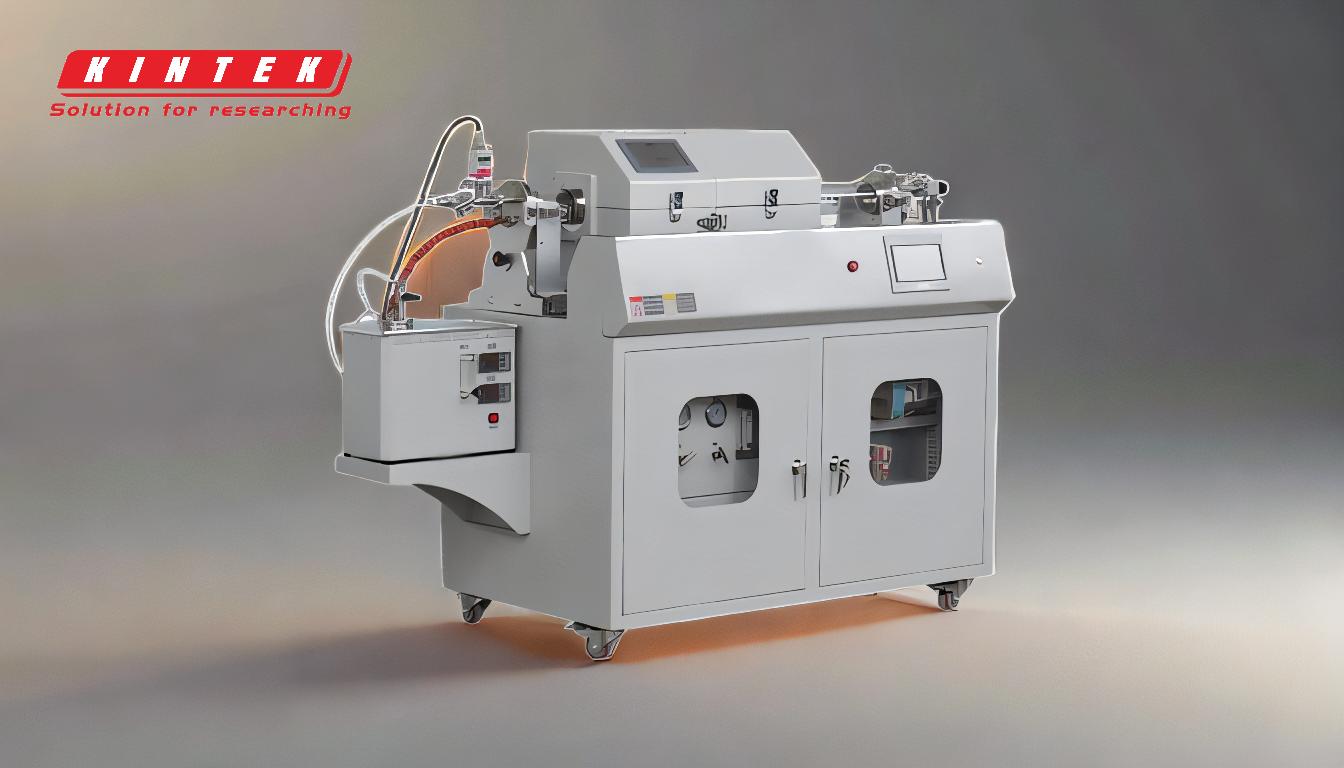
-
Basic Principle of Magnetron Sputtering:
- Magnetron sputtering is a PVD technique where a target material is bombarded by high-energy ions, causing atoms to be ejected from the target surface.
- These ejected atoms travel through a vacuum and deposit onto a substrate, forming a thin film.
-
Role of Plasma and Ionization:
- The process occurs in a high-vacuum chamber filled with inert gas, typically argon.
- A high negative voltage is applied between the cathode (target) and anode, ionizing the argon gas and creating a plasma.
- The plasma consists of positively charged argon ions and free electrons, which are essential for the sputtering process.
-
Magnetic Field Confinement:
- A strong magnetic field is applied near the target surface to trap electrons in a circular trajectory.
- This confinement increases the residence time of electrons in the plasma, enhancing collisions with argon atoms and boosting ionization.
- The increased plasma density improves the efficiency of the sputtering process.
-
Sputtering Mechanism:
- Positive argon ions from the plasma are accelerated toward the negatively charged target due to the applied voltage.
- When these ions collide with the target surface, they transfer kinetic energy to the target atoms.
- If the energy is sufficient, target atoms are ejected from the surface in a process called sputtering.
-
Deposition of Thin Films:
- The ejected target atoms travel in a line-of-sight trajectory and condense on the substrate surface.
- The deposition process results in a uniform, high-quality thin film with precise control over thickness and composition.
-
Advantages of Magnetron Sputtering:
- High deposition rates due to increased plasma density.
- Ability to deposit a wide range of materials, including metals, alloys, and ceramics.
- Excellent film uniformity and adhesion.
- Minimal substrate damage due to controlled ion bombardment.
-
Applications of Magnetron Sputtering:
- Semiconductor manufacturing: Deposition of conductive and insulating layers.
- Optical coatings: Anti-reflective and reflective coatings for lenses and mirrors.
- Decorative coatings: Thin films for aesthetic purposes on consumer products.
- Hard coatings: Wear-resistant coatings for tools and industrial components.
-
Process Parameters:
- Vacuum pressure: Typically maintained at low levels (10^-3 to 10^-6 Torr) to ensure a clean environment and reduce contamination.
- Power supply: High negative voltage (several hundred to several thousand volts) is applied to the target.
- Magnetic field strength: Optimized to balance electron confinement and plasma density.
- Gas flow rate: Controlled to maintain consistent plasma conditions.
By understanding these key points, equipment and consumable purchasers can make informed decisions about the suitability of magnetron sputtering for specific applications and ensure optimal process conditions for high-quality thin film deposition.
Summary Table:
Aspect | Details |
---|---|
Basic Principle | High-energy ions eject target atoms, which deposit as thin films on substrates. |
Plasma & Ionization | Argon gas ionized in a vacuum creates plasma for efficient sputtering. |
Magnetic Field Confinement | Traps electrons near the target, increasing plasma density and efficiency. |
Advantages | High deposition rates, material versatility, uniform coatings, minimal substrate damage. |
Applications | Semiconductors, optical coatings, decorative films, and hard coatings. |
Process Parameters | Vacuum pressure, power supply, magnetic field strength, and gas flow rate. |
Discover how magnetron sputtering can enhance your thin film processes—contact our experts today!