Plastic pyrolysis is a promising technology for converting plastic waste into valuable products like fuel oil, but it faces several technical and operational challenges. These include energy inefficiencies, heat transfer issues, feedstock contamination, and reactor design limitations. Addressing these problems is crucial for improving the economic viability and environmental sustainability of pyrolysis operations. Key areas of concern include optimizing energy recovery, enhancing reactor performance, managing feedstock quality, and minimizing heat loss during the process.
Key Points Explained:
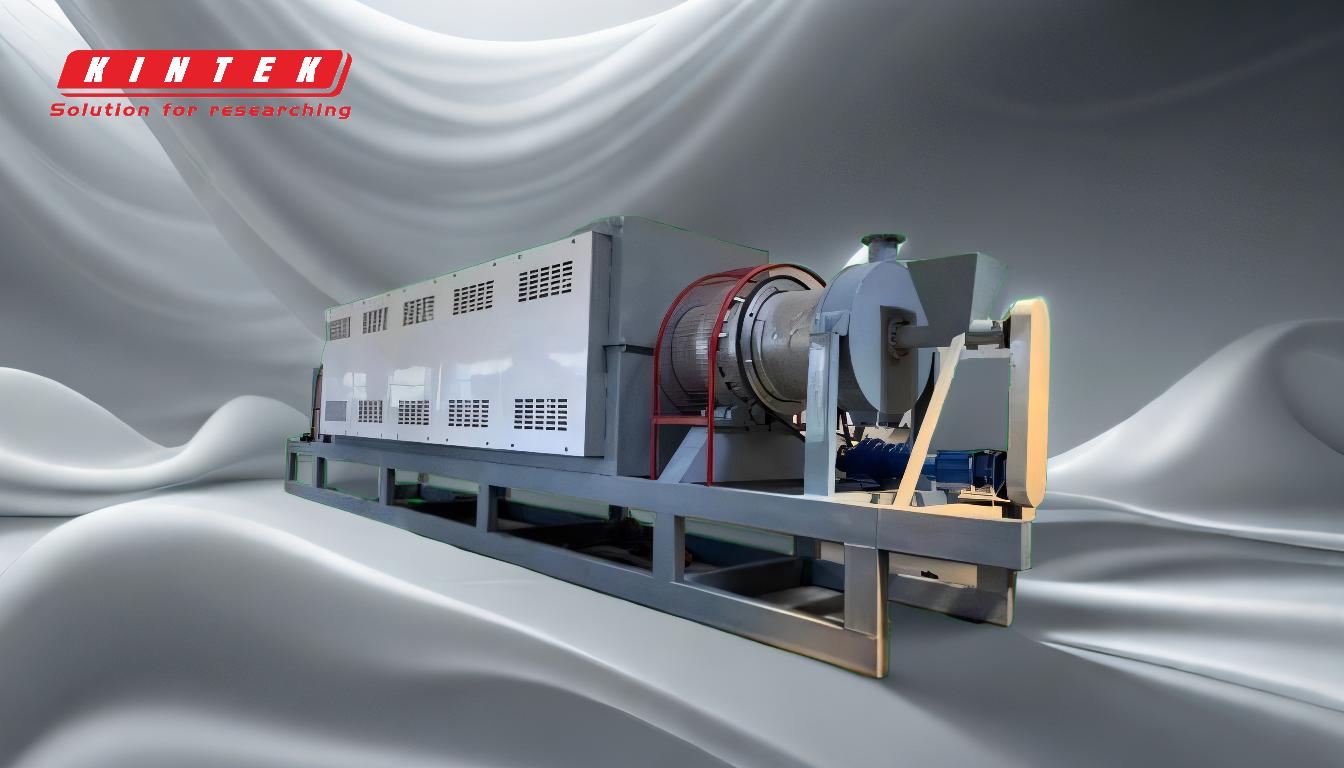
-
Energy Efficiency and Heat Transfer Challenges:
- Pyrolysis requires significant energy input to heat the plastic waste to temperatures between 200-900°C. Achieving efficient heat transfer into the plastic particles is a major challenge.
- Solutions include using solid heat carriers, hot gas streams, or indirect heat exchange through reactor walls or built-in tubes/plates. These methods aim to improve heat distribution and reduce energy losses.
- Energy efficiency directly impacts profitability, as inefficient energy recovery increases operational costs and reduces the economic viability of pyrolysis plants.
-
Reactor Design and Performance:
- The design of the pyrolysis reactor plays a critical role in determining the efficiency and effectiveness of the process. Poor reactor designs can lead to uneven heating, incomplete pyrolysis, and lower yields of usable products.
- Technical challenges include reducing parasitic energy losses, improving heat distribution, and preventing the accumulation of metal and ash in reactor bed materials, which can impede the process and reduce bio-oil yields.
- Insulated reactor casings are essential for minimizing heat loss, reducing fuel consumption, and improving overall energy efficiency.
-
Feedstock Quality and Pretreatment:
- Plastic waste often contains impurities such as metals, dirt, and non-plastic materials, which can interfere with the pyrolysis process and reduce the quality of the end products.
- Pretreatment steps, including shredding, drying, and separating non-plastics, are necessary to ensure consistent feedstock quality. However, these steps add complexity and cost to the process.
- Contaminated feedstock can lead to clogging, increased maintenance requirements, and lower yields of pyrolysis oil.
-
Product Quality and Refinement:
- The pyrolysis process produces a mixture of liquid oil, gases, and solid residues. The quality of the pyrolysis oil depends on the feedstock and process conditions.
- Distillation and purification are required to refine the pyrolysis oil into usable fuel. However, these steps can be energy-intensive and may reduce the overall efficiency of the process.
- Inconsistent product quality can limit the marketability of pyrolysis oil and affect the economic feasibility of the operation.
-
Environmental and Economic Considerations:
- While pyrolysis offers a way to recycle plastic waste, the process itself can generate emissions and waste, requiring proper management to minimize environmental impact.
- The economic viability of pyrolysis depends on factors such as feedstock availability, energy costs, and the market value of the end products. High operational costs and low product yields can make it difficult to achieve profitability.
By addressing these challenges through improved reactor designs, better feedstock management, and enhanced energy recovery, the plastic pyrolysis process can become more efficient, sustainable, and economically viable.
Summary Table:
Challenge | Key Issues | Solutions |
---|---|---|
Energy Efficiency | High energy input, inefficient heat transfer | Use solid heat carriers, hot gas streams, or indirect heat exchange |
Reactor Design | Uneven heating, incomplete pyrolysis, parasitic energy losses | Insulated casings, improved heat distribution, and reactor bed management |
Feedstock Quality | Contamination with metals, dirt, and non-plastics | Pretreatment steps like shredding, drying, and separation |
Product Quality | Inconsistent pyrolysis oil quality, energy-intensive refinement | Distillation and purification processes |
Economic Viability | High operational costs, low product yields, marketability issues | Optimize feedstock availability, energy costs, and product value |
Discover how to overcome plastic pyrolysis challenges—contact our experts today for tailored solutions!