Optical coating is a specialized process used to apply thin layers of materials onto optical components like lenses, mirrors, and filters to enhance their performance. The process involves several critical steps, including surface preparation, deposition of coating materials, and curing or finishing. Optical coatings are designed to modify the reflection, transmission, or absorption properties of light, making them essential for applications in optics, photonics, and laser systems. The process requires precision and control to achieve the desired optical properties, such as anti-reflective coatings, high-reflective mirrors, or beam splitters.
Key Points Explained:
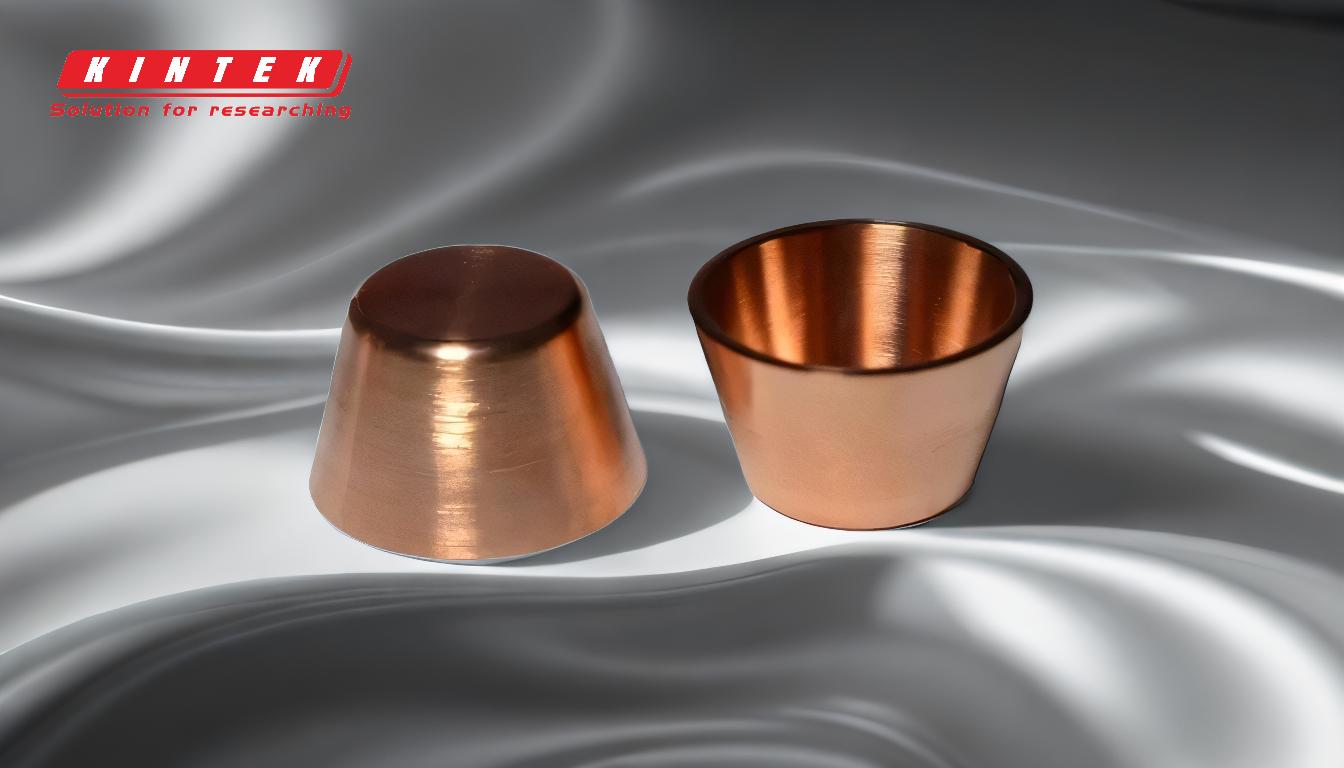
-
Purpose of Optical Coatings:
- Optical coatings are applied to improve the performance of optical components by controlling how light interacts with their surfaces.
- Common types of coatings include anti-reflective coatings, high-reflective coatings, and beam splitters.
- These coatings are used in lenses, mirrors, filters, and other optical devices to enhance functionality in scientific, industrial, and consumer applications.
-
Surface Preparation:
- Before applying the coating, the optical component must be thoroughly cleaned to remove any contaminants, such as dust, oils, or residues.
- Cleaning methods may include ultrasonic cleaning, solvent cleaning, or abrasive cleaning with specialized liquids.
- Proper surface preparation ensures strong adhesion of the coating and prevents defects like bubbles or uneven layers.
-
Deposition Techniques:
- The coating material is deposited onto the optical component using specialized techniques. Common methods include:
- Physical Vapor Deposition (PVD): Involves vaporizing the coating material in a vacuum and allowing it to condense onto the surface of the component.
- Chemical Vapor Deposition (CVD): Uses chemical reactions to deposit a solid material onto the surface.
- Sputtering: A PVD technique where atoms are ejected from a solid target material and deposited onto the component.
- The choice of deposition method depends on the desired coating properties, such as thickness, uniformity, and material compatibility.
- The coating material is deposited onto the optical component using specialized techniques. Common methods include:
-
Coating Materials:
- The materials used for optical coatings are selected based on their optical properties, such as refractive index, transparency, and durability.
- Common materials include:
- Dielectrics: Used for anti-reflective coatings and beam splitters.
- Metals: Used for high-reflective mirrors (e.g., aluminum, silver, or gold).
- Multilayer Stacks: Combine multiple materials to achieve specific optical effects, such as interference filters.
-
Curing and Finishing:
- After deposition, the coating may undergo curing or finishing processes to enhance its durability and performance.
- Curing can involve heat treatment or exposure to ultraviolet light to solidify the coating.
- Finishing steps may include polishing or additional cleaning to ensure the coating meets the required specifications.
-
Quality Control and Testing:
- Optical coatings are subjected to rigorous quality control to ensure they meet the desired optical and mechanical properties.
- Testing methods include:
- Spectrophotometry: Measures the transmission and reflection properties of the coating.
- Adhesion Testing: Ensures the coating is firmly bonded to the substrate.
- Environmental Testing: Evaluates the coating's resistance to factors like humidity, temperature, and abrasion.
-
Applications of Optical Coatings:
- Optical coatings are used in a wide range of applications, including:
- Consumer Electronics: Anti-reflective coatings on camera lenses and smartphone screens.
- Scientific Instruments: High-reflective mirrors for telescopes and laser systems.
- Industrial Equipment: Filters and beam splitters for imaging and sensing systems.
- Optical coatings are used in a wide range of applications, including:
By following these steps, optical coating processes create high-performance optical components that meet the stringent requirements of modern technology and scientific research.
Summary Table:
Key Aspect | Details |
---|---|
Purpose | Improve light interaction (reflection, transmission, absorption) |
Common Coatings | Anti-reflective, high-reflective, beam splitters |
Surface Preparation | Cleaning methods: ultrasonic, solvent, abrasive |
Deposition Techniques | PVD, CVD, sputtering |
Coating Materials | Dielectrics, metals (aluminum, silver, gold), multilayer stacks |
Curing & Finishing | Heat treatment, UV exposure, polishing |
Quality Control | Spectrophotometry, adhesion testing, environmental testing |
Applications | Consumer electronics, scientific instruments, industrial equipment |
Ready to enhance your optical components? Contact our experts today for tailored solutions!