Thin film deposition by sputtering is a widely used Physical Vapor Deposition (PVD) technique that involves the ejection of atoms from a solid target material due to bombardment by high-energy ions. These ejected atoms then deposit onto a substrate to form a thin film. The process occurs in a vacuum chamber, where a controlled gas, typically argon, is introduced. A voltage is applied to generate a plasma, and the gas atoms become positively charged ions. These ions are accelerated toward the target material, causing atoms to be ejected and deposited onto the substrate. The process is highly controllable and produces uniform, high-quality thin films.
Key Points Explained:
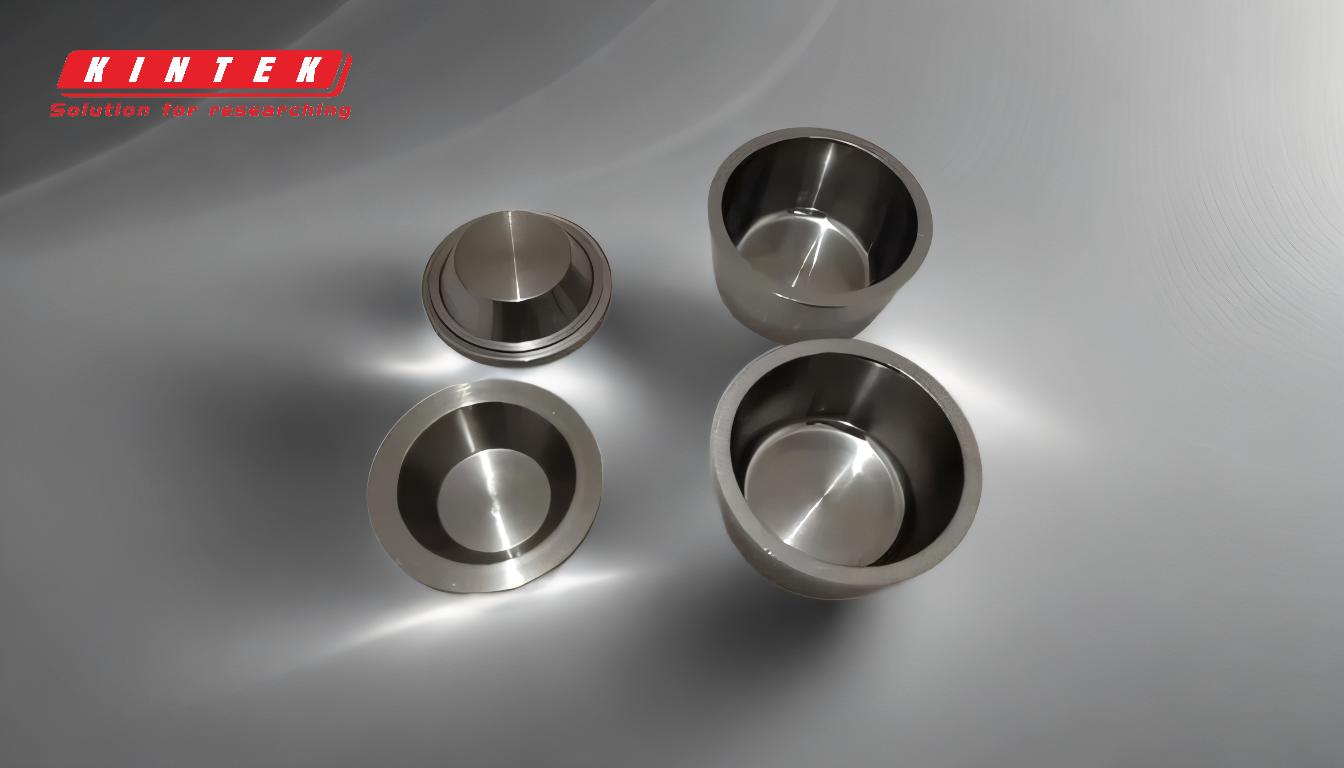
-
Vacuum Chamber Setup:
- The sputtering process begins in a vacuum chamber to minimize contamination and ensure a controlled environment.
- A controlled gas, typically argon, is introduced into the chamber at low pressure.
-
Generation of Plasma:
- A high voltage is applied between the vacuum chamber and an electrode (target) made of the material to be deposited.
- This voltage ionizes the argon gas, creating a plasma consisting of positively charged argon ions and free electrons.
-
Ion Bombardment:
- The positively charged argon ions are accelerated toward the negatively charged target (cathode) due to the applied voltage.
- When these high-energy ions collide with the target, they transfer their momentum to the target atoms, ejecting them from the surface.
-
Ejection of Target Atoms:
- The collision between the argon ions and the target material causes atoms or molecules of the target to be ejected in a process known as sputtering.
- These ejected atoms form a vapor stream within the vacuum chamber.
-
Deposition onto Substrate:
- The ejected target atoms travel ballistically through the vacuum and deposit onto the substrate placed within the chamber.
- The substrate is typically positioned opposite the target to ensure uniform deposition.
-
Formation of Thin Film:
- The deposited atoms accumulate on the substrate, forming a thin film layer by layer.
- The thickness and uniformity of the film can be controlled by adjusting parameters such as the sputtering time, power, and gas pressure.
-
Role of Momentum Transfer:
- Momentum transfer between the argon ions and the target atoms is crucial for the sputtering process.
- This transfer ensures the efficient ejection of target atoms and their subsequent deposition onto the substrate.
-
Re-Sputtering and Surface Adhesion:
- In some cases, re-sputtering may occur, where deposited material is bombarded again, improving film adhesion and quality.
- The process ensures that the thin film adheres securely to the substrate surface.
-
Advantages of Sputtering:
- Sputtering allows for the deposition of a wide range of materials, including metals, alloys, and ceramics.
- It produces films with excellent uniformity, density, and adhesion, making it suitable for applications in electronics, optics, and coatings.
-
Comparison with Other Deposition Techniques:
- Unlike Chemical Vapor Deposition (CVD), which relies on chemical reactions, sputtering is a purely physical process.
- Sputtering offers better control over film composition and structure compared to techniques like spray pyrolysis.
In summary, sputtering is a versatile and precise method for thin film deposition, leveraging high-energy ion bombardment to eject target atoms and deposit them onto a substrate. Its ability to produce high-quality, uniform films makes it a preferred choice in various industries.
Summary Table:
Key Step | Description |
---|---|
Vacuum Chamber Setup | Process occurs in a vacuum to minimize contamination; argon gas is introduced. |
Plasma Generation | High voltage ionizes argon gas, creating a plasma of argon ions and electrons. |
Ion Bombardment | Argon ions accelerate toward the target, ejecting atoms via momentum transfer. |
Ejection of Atoms | Target atoms are ejected, forming a vapor stream in the chamber. |
Deposition onto Substrate | Ejected atoms deposit onto the substrate, forming a thin film layer by layer. |
Film Formation | Film thickness and uniformity are controlled by sputtering time, power, and gas pressure. |
Advantages | Produces uniform, dense, and adherent films for electronics, optics, and coatings. |
Discover how sputtering can enhance your thin film applications—contact our experts today!