Vacuum thermoforming is a manufacturing process used to shape plastic materials into specific forms by heating a plastic sheet and using vacuum pressure to mold it around a single mold. The process involves heating the plastic until it becomes pliable, positioning it over a mold, and applying vacuum suction to draw the material tightly around the mold's contours. Once the material cools, it retains the shape of the mold, resulting in a high-quality, flexible product. This method is widely used for creating custom designs and prototypes due to its cost-effectiveness and versatility.
Key Points Explained:
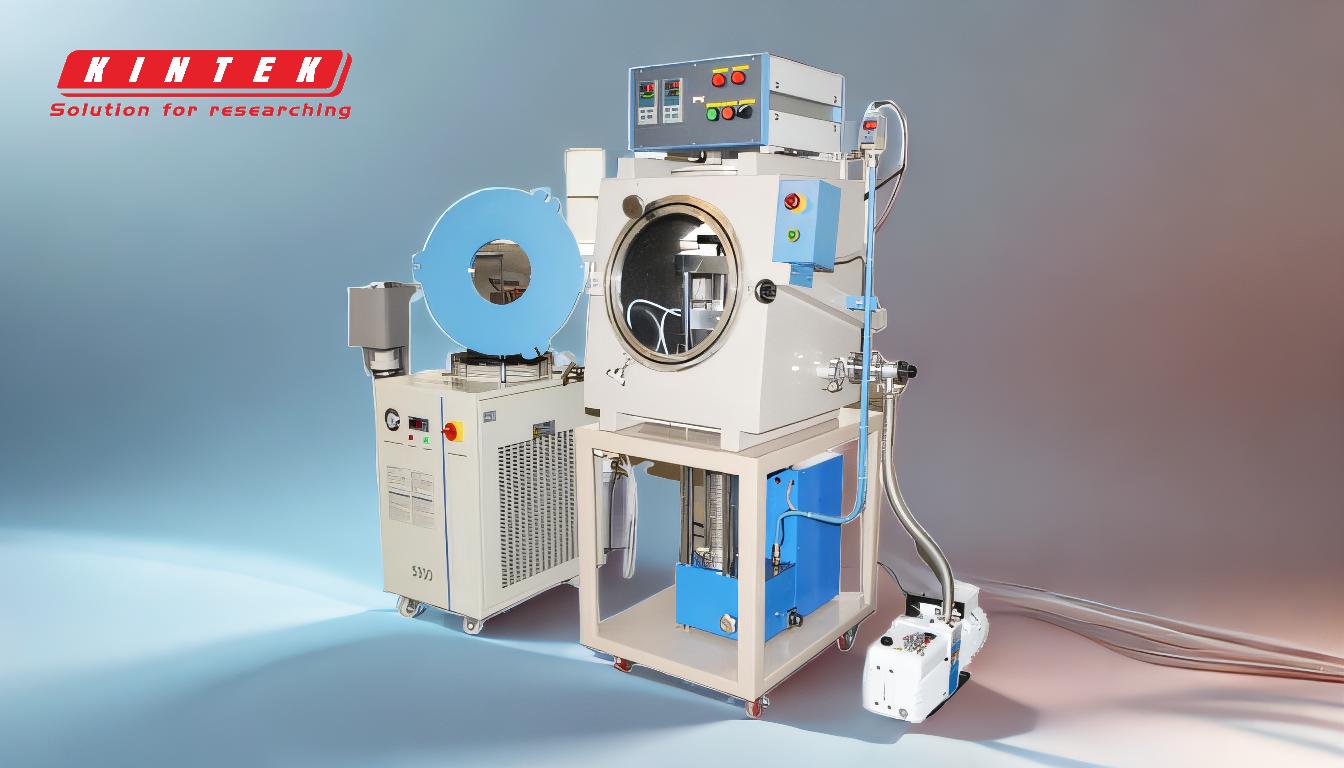
-
Material Preparation:
- A flat sheet of thermoplastic material is selected based on the desired properties of the final product, such as thickness, flexibility, and durability.
- The sheet is clamped into a frame to hold it securely in place during the heating and forming stages.
-
Heating the Plastic Sheet:
- The plastic sheet is heated uniformly using radiant heaters until it reaches its optimal forming temperature. This temperature varies depending on the type of plastic used.
- Heating makes the plastic pliable and easier to shape without cracking or tearing.
-
Positioning Over the Mold:
- Once heated, the plastic sheet is positioned directly above the mold. The mold is typically made of wood, aluminum, or composite materials and is designed to match the desired final shape.
- Proper alignment ensures that the plastic will conform accurately to the mold's contours.
-
Applying Vacuum Pressure:
- A vacuum pump is activated, creating suction that pulls the heated plastic sheet tightly around the mold. This step ensures that the plastic takes on the exact shape of the mold, including fine details and complex geometries.
- The vacuum pressure must be strong enough to eliminate air pockets and ensure a smooth, even surface.
-
Cooling and Solidification:
- After the plastic has been formed, it is allowed to cool and solidify while still under vacuum pressure. Cooling can be accelerated using fans or water sprays.
- Once cooled, the plastic retains the shape of the mold and becomes rigid.
-
Removing the Formed Part:
- The vacuum is released, and the formed plastic part is removed from the mold. Excess material, known as flash, is trimmed away to achieve the final product.
- The part may undergo additional finishing processes, such as painting, drilling, or assembly, depending on its intended use.
-
Advantages of Vacuum Thermoforming:
- Cost-Effectiveness: Lower tooling costs compared to other molding methods, making it ideal for prototyping and low-volume production.
- Design Flexibility: Allows for complex shapes and intricate details.
- Material Efficiency: Minimal waste, as excess material can often be recycled.
- Speed: Faster production cycles compared to injection molding.
-
Applications:
- Vacuum thermoforming is used in various industries, including packaging (e.g., blister packs, trays), automotive (e.g., interior panels), medical (e.g., equipment housings), and consumer goods (e.g., toys, displays).
By following these steps, vacuum thermoforming provides a versatile and efficient method for producing high-quality plastic parts with precise shapes and details.
Summary Table:
Step | Description |
---|---|
Material Preparation | Select thermoplastic sheet based on thickness, flexibility, and durability. Clamp securely. |
Heating | Heat uniformly until pliable. Temperature varies by plastic type. |
Positioning Over Mold | Align heated sheet over mold (wood, aluminum, or composite) for accurate shaping. |
Vacuum Pressure | Apply suction to draw plastic tightly around mold, ensuring fine details and smooth surfaces. |
Cooling | Allow plastic to cool and solidify under vacuum pressure. Accelerate with fans or water sprays. |
Removing Part | Release vacuum, trim excess material, and perform finishing processes (e.g., painting, drilling). |
Advantages | Cost-effective, design flexibility, material efficiency, and fast production cycles. |
Applications | Packaging, automotive, medical, and consumer goods industries. |
Discover how vacuum thermoforming can streamline your production—contact us today for expert guidance!