The product size achieved by a hammer mill is primarily determined by the screen size installed and the hammer speed. Laboratory hammer mills are capable of grinding materials to sizes under 1mm, depending on these factors. These mills are available in 6” and 8” wide models and can process between 50 to 150 pounds of material per hour, depending on the material type. This flexibility makes them suitable for a variety of applications where precise particle size reduction is required.
Key Points Explained:
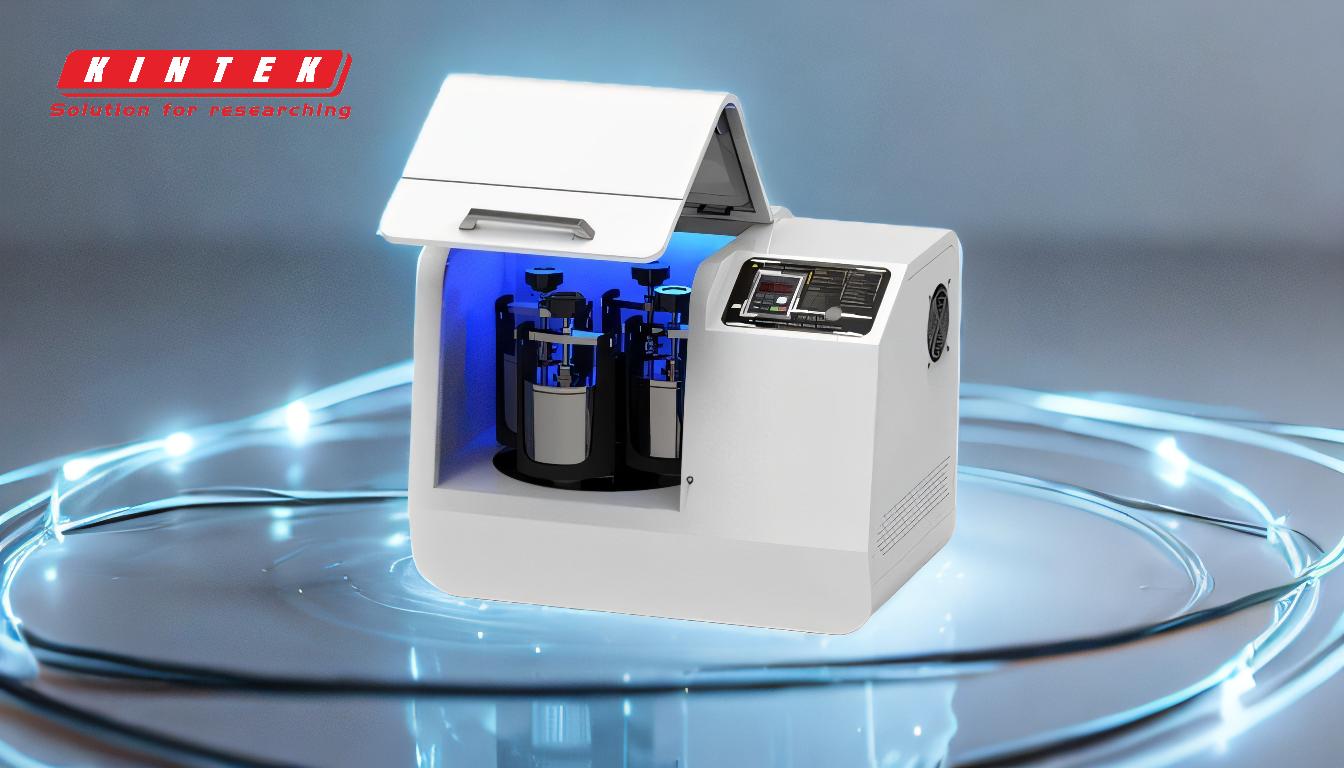
-
Determinants of Product Size:
- Screen Size: The screen size installed in the hammer mill is a critical factor in determining the final product size. Smaller screen sizes result in finer particles, while larger screens allow for coarser particles.
- Hammer Speed: The speed at which the hammers rotate also affects the particle size. Higher speeds can lead to finer grinding, while lower speeds may result in coarser particles.
-
Product Size Range:
- The laboratory hammer mill is capable of grinding materials to sizes under 1mm. This fine grinding capability is essential for applications requiring precise particle size control, such as in pharmaceuticals, food processing, and material science research.
-
Model Variability:
- 6” and 8” Models: The laboratory hammer mill is available in two widths, 6” and 8”. The choice between these models depends on the volume of material to be processed and the desired throughput. The 8” model, being wider, can handle larger quantities of material compared to the 6” model.
-
Processing Capacity:
- Throughput: The hammer mill can process between 50 to 150 pounds of material per hour. This throughput varies based on the type of material being processed. For example, softer materials may be processed at the higher end of this range, while harder materials may require more time and result in lower throughput.
-
Applications:
- The ability to achieve fine particle sizes makes the laboratory hammer mill suitable for a wide range of applications. These include but are not limited to:
- Pharmaceuticals: For grinding active pharmaceutical ingredients to precise sizes.
- Food Processing: For creating fine powders from food products.
- Material Science: For research and development requiring controlled particle sizes.
- The ability to achieve fine particle sizes makes the laboratory hammer mill suitable for a wide range of applications. These include but are not limited to:
-
Operational Considerations:
- Material Type: The type of material being processed significantly impacts the efficiency and output of the hammer mill. Harder materials may require more energy and time to achieve the desired particle size.
- Maintenance: Regular maintenance of the hammer mill, including checking and replacing screens and hammers, is essential to maintain consistent product size and throughput.
In summary, the product size achieved by a laboratory hammer mill is a function of the screen size and hammer speed, with the capability to grind materials to under 1mm. The availability of 6” and 8” models, along with a processing capacity of 50-150 pounds per hour, makes it a versatile tool for various industries requiring precise particle size reduction.
Summary Table:
Factor | Impact on Product Size |
---|---|
Screen Size | Smaller screens produce finer particles; larger screens allow for coarser particles. |
Hammer Speed | Higher speeds result in finer grinding; lower speeds produce coarser particles. |
Product Size Range | Capable of grinding materials to sizes under 1mm. |
Model Variability | Available in 6” and 8” models to handle different material volumes. |
Processing Capacity | Processes 50-150 pounds per hour, depending on material type. |
Applications | Pharmaceuticals, food processing, and material science research. |
Need a hammer mill for precise particle size reduction? Contact our experts today to find the perfect solution for your needs!